Understanding Flap Disc Types A Comprehensive Guide
Flap discs have become an essential tool in metalworking and other industries, primarily recognized for their efficiency in grinding, blending, and finishing surfaces. They consist of overlapping flaps made from abrasive materials, typically positioned on a backing plate. Their versatile nature makes them suitable for various applications, but it's important to choose the right type for your specific needs. This article delves into the different types of flap discs available, highlighting their features, advantages, and ideal usage.
1. Type of Flap Disc Standard Flap Discs
Standard flap discs are designed with overlapping flaps of abrasive material, usually arranged at an angle of 15 to 30 degrees on a rigid or flexible backing. These discs are commonly used for general-purpose grinding and finishing but can be applied to various materials, including wood and metal. Their construction allows for a more aggressive cut, making them ideal for heavy material removal while providing a smooth finish.
Advantages - High durability and longevity. - Suitable for both grinding and finishing. - Effective for contouring and edge work.
2. Type of Flap Disc T29 (Conical) Flap Discs
T29 flap discs, also known as conical flap discs, have a slightly angled shape, which enhances their performance in specific applications. The conical design allows for better control and precision, making them perfect for weld blending, surface preparation, and more intricate finishing tasks.
Advantages - Improved grinding control and accuracy. - Highly effective for contouring and corners. - Excellent for blending welds and other irregular surfaces.
3
. Type of Flap Disc T27 (Flat) Flap DiscsT27 flap discs, or flat flap discs, possess a flat face which makes them suitable for larger flat surfaces. This design is particularly beneficial when working with flat materials and allows for a more extensive surface area contact, ensuring an even and consistent finish.
Advantages - Ideal for flat and level surfaces. - Provides a smooth, uniform finish. - Excellent for finishing work post-grinding.
flap disc types
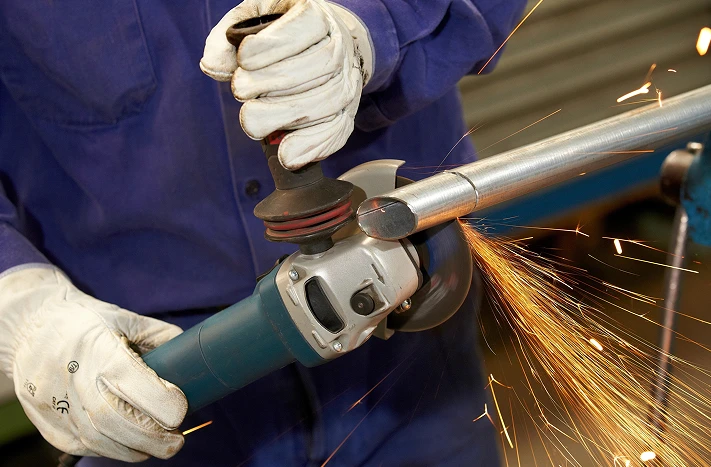
4. Type of Flap Disc Ceramic Flap Discs
Ceramic flap discs are known for their exceptional performance and longevity. They are typically constructed with ceramic abrasives, making them suitable for high-speed applications and tougher materials like stainless steel and high-alloy metals. These discs resist wear better than traditional aluminum oxide discs, leading to quicker stock removal and a cooler grinding process, which minimizes heat damage to project materials.
Advantages - Long-lasting and suitable for heavy-duty applications. - Effective for hard-to-grind materials. - Reduced heat buildup for enhanced material integrity.
5. Type of Flap Disc Zirconia Flap Discs
Zirconia flap discs are an excellent choice for those looking for a balance between performance and cost. Made from zirconia oxide, these discs provide a reliable solution for metalworking tasks and are effective for both grinding and finishing. They can handle a range of materials and are particularly known for their durability.
Advantages - Good performance on various materials. - Cost-effective for medium to heavy grinding tasks. - Suitable for both grinding and surface finishing applications.
6. Choosing the Right Flap Disc
When selecting a flap disc, consider factors such as the material you will be working on, the type of job (e.g., grinding, finishing, or both), and the specific requirements of your project. Different flap disc types have varying abrasive materials, grits, and designs that influence their effectiveness for particular tasks.
Conclusion
Flap discs are versatile tools in metalworking and other related industries. By understanding the different types available, including standard, conical (T29), flat (T27), ceramic, and zirconia flap discs, users can make informed choices to enhance their productivity and achieve superior results. Whether you're removing material, blending surfaces, or achieving a fine finish, selecting the right flap disc is crucial for efficiency and quality. Always remember to consider the specific requirements of your project and the characteristics of the materials you're working with to choose the most suitable flap disc.
Post time:Nov - 27 - 2024