Understanding Flap Disc Types A Comprehensive Guide
Flap discs have become an indispensable tool in various industries, particularly in metalworking, woodworking, and construction. Their versatility and efficiency make them essential for tasks such as grinding, polishing, and rust removal. The efficacy of flap discs is largely determined by their types, which vary in material, design, and intended use. This article aims to elucidate the different types of flap discs available in the market, helping users select the right type for their specific applications.
Types of Flap Discs
1. Ceramic Flap Discs
Ceramic flap discs are renowned for their durability and long-lasting performance. They are particularly effective for grinding hard materials like stainless steel and high-alloy steels. The ceramic grain used in these discs provides excellent heat resistance and reduces the wear on the abrasive surface. Professionals in metal fabrication and welding often prefer ceramic flap discs for their aggressive cutting ability and longevity.
Aluminum oxide is one of the most commonly used materials for flap discs. These discs are ideal for general-purpose grinding applications and are suitable for use on both ferrous and non-ferrous metals. They provide a good balance between performance and cost, making them popular among DIY enthusiasts and professional tradespeople alike. Aluminum oxide flap discs are available in various grit sizes, allowing users to choose the ideal disc for their specific task.
3. Zirconia Flap Discs
Zirconia flap discs are designed for heavy-duty applications and are especially effective for grinding tough metals. The zirconia grain cuts more aggressively than aluminum oxide, making these discs suitable for high-volume work. They are often used in metalworking industries where speed and efficiency are top priorities. Additionally, zirconia discs maintain their cutting effectiveness even at high temperatures, enhancing their longevity and performance.
flap disc types
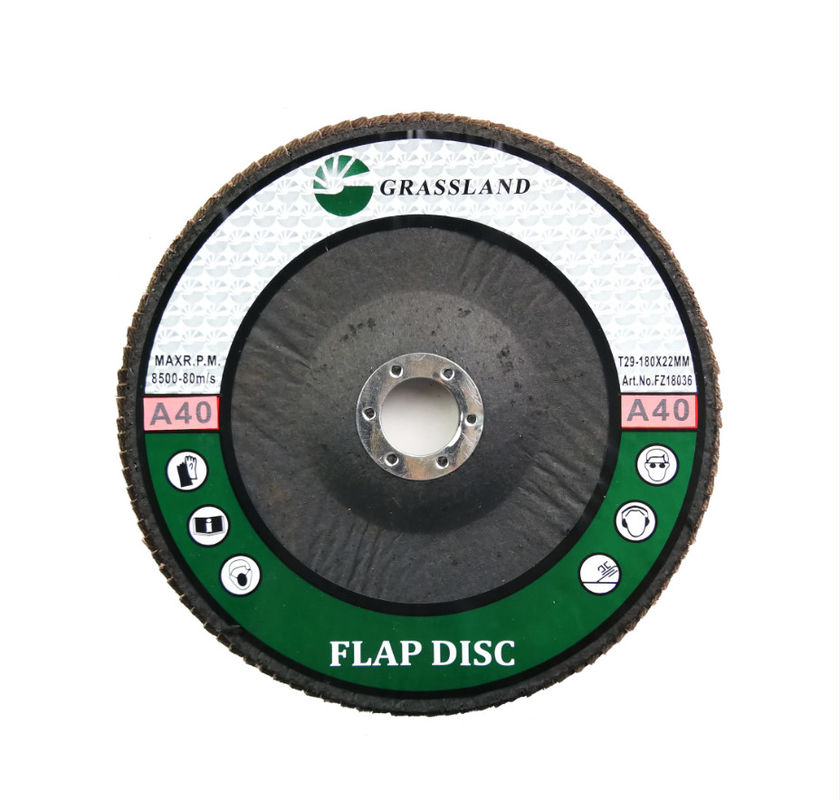
4. Silicon Carbide Flap Discs
Silicon carbide flap discs are less common but serve specific applications, especially in grinding softer materials like fiberglass and plastic. They offer exceptional performance in these areas due to their sharp cutting edges. While silicon carbide is not as durable as other abrasive materials, these discs provide a fine finish and are often employed in the finishing stages of a project.
5. Non-Woven Flap Discs
Non-woven flap discs, also known as surface conditioning discs, are designed for polishing and finishing applications. They do not have a rigid structure and are made from synthetic fibers, making them ideal for achieving a smooth finish without removing too much material. Non-woven flap discs are particularly popular for cleaning, deburring, and surface preparation.
Choosing the Right Flap Disc
When selecting a flap disc, users should consider several factors, including the material being worked on, the specific application (e.g., grinding vs. finishing), and the grit size required. A higher grit size will yield a smoother finish, while a lower grit size is suited for aggressive material removal. Additionally, choosing the right backing plate is essential; flat discs are ideal for flat surfaces, while conical discs are better for edge work and contours.
Conclusion
In summary, flap discs are vital tools for numerous applications across various industries. Understanding the different types of flap discs—ceramic, aluminum oxide, zirconia, silicon carbide, and non-woven—can significantly enhance efficiency and output in manufacturing and construction tasks. By selecting the appropriate flap disc, users can optimize their work process, ensuring they achieve the desired results with minimal effort. Whether for professional use or personal projects, investing time in choosing the right flap disc can lead to more productive and successful outcomes.
Post time:Nov - 29 - 2024