Flap Disc vs. Fiber Disc A Comparative Analysis
When it comes to abrasive discs used in grinding and polishing applications, two prominent types come to the forefront flap discs and fiber discs. While both serve the primary purpose of surface preparation and finishing, they possess distinct characteristics that make them suitable for different tasks. Understanding these differences is crucial for selecting the right abrasive tool for your project.
Composition and Structure
Flap discs are composed of multiple layers of abrasive material, typically arranged in a radial fashion around a central hub. Each flap is made from a piece of sandpaper or coated abrasive that is fixed to a backing plate. This design allows for flexibility during use, providing a conforming surface that can reach into contours and irregular shapes. The layered flaps also promote a cooler grinding action, which minimizes heat buildup and extends the life of both the disc and the workpiece.
On the other hand, fiber discs are made from a single piece of abrasive material bonded to a fiber backing. These discs can either be rigid or flexible, but they generally offer a more aggressive cutting action compared to flap discs. The solid construction allows for increased pressure to be applied, making fiber discs suitable for more demanding applications, such as heavy stock removal and surface leveling.
Performance Characteristics
When comparing the performance of flap discs and fiber discs, several factors come into play. Flap discs tend to provide a finer finish thanks to their smoother grinding action. They are excellent for blending, finishing, and deburring applications, making them popular choices for metalworking and automotive industries. Their ability to grind and polish simultaneously adds to their versatility, allowing users to achieve desired surface qualities in fewer steps.
flap disc vs fiber disc
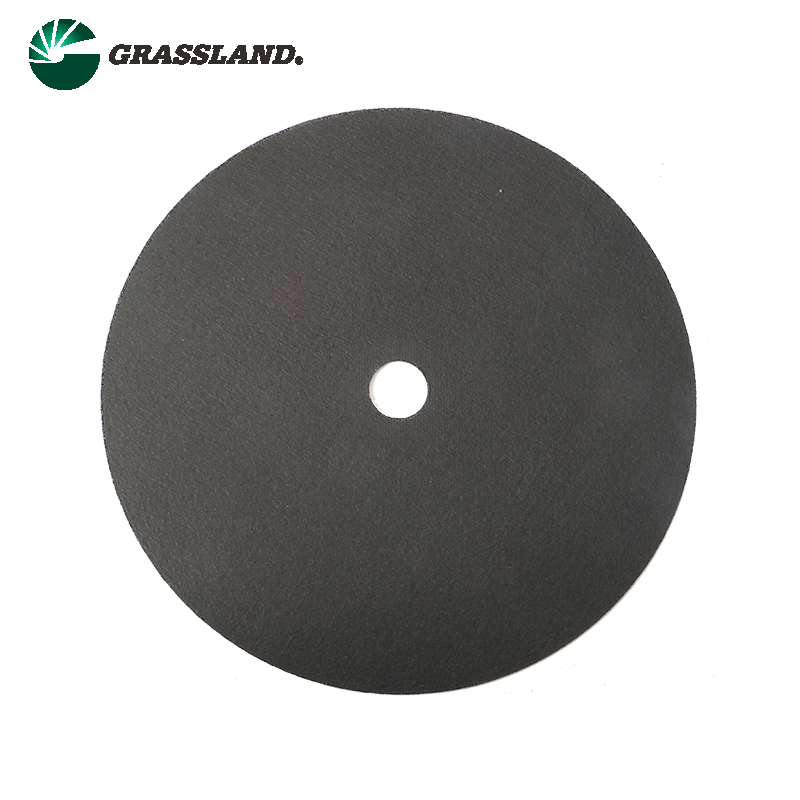
In contrast, fiber discs excel in aggressive material removal. Their solid structure enables them to abrade surfaces quickly, making them ideal for heavy-duty tasks like weld grinding and surface preparation before coating. However, this aggressive cutting action can sometimes lead to a rougher finish compared to flap discs. Therefore, while fiber discs are highly effective for initial stock removal, additional steps may be necessary to achieve a finer surface finish.
Versatility and Applications
One of the significant advantages of flap discs is their versatility. They can be used on a variety of materials, including metals, plastics, and composites. They are also available in different grit sizes, allowing users to choose the appropriate disc for specific applications. Flap discs are particularly useful for tasks that require a combination of grinding and finishing, such as preparing stainless steel surfaces or handling intricate designs.
Fiber discs, while also versatile, thrive in high-intensity applications. They are better suited for situations that demand maximum material removal in a shorter time frame. Industries that require heavy-duty grinding, such as shipbuilding or metal fabrication, often favor fiber discs over flap discs due to their robustness and efficiency. Nevertheless, users should be mindful of the potential finish quality when utilizing fiber discs, especially on sensitive materials.
Conclusion
In summary, both flap discs and fiber discs have their unique strengths and applications in the realm of abrasive tooling. Flap discs are favored for their finesse and versatility, making them ideal for finishing tasks and projects requiring a meticulous touch. In contrast, fiber discs shine in scenarios demanding swift material removal and aggressiveness. Ultimately, the choice between flap discs and fiber discs will depend on the specific requirements of the task at hand. Understanding their differences empowers users to make informed decisions that enhance productivity and achieve superior results in their grinding and polishing endeavors. The right tool can make all the difference in ensuring quality work and efficiency in any project.
Post time:Dec - 12 - 2024