The Flap Disk Revolution Transforming Industrial Grinding
In the world of industrial grinding and surface preparation, flap discs have emerged as a revolutionary tool, transforming how professionals approach metalworking tasks. These versatile products offer unique advantages over traditional grinding wheels and other abrasive tools, leading to increased efficiency, safety, and superior results. This article delves into the design, application, and benefits of flap discs, particularly focusing on their role in modern machining environments.
What is a Flap Disk?
A flap disk is an abrasive tool constructed from overlapping flaps of coated abrasive material. These flaps are attached to a rigid backing plate, and they can be made from a variety of abrasives, including aluminum oxide, zirconia alumina, and ceramic. The design allows for a larger surface area during operation, which contributes to a more gradual, controlled grinding process compared to traditional grinding wheels. Furthermore, the innovative arrangement of the flaps enhances the cooling effect, reducing the heat generated during grinding, which in turn minimizes the risk of damaging the workpiece.
Applications Across Industries
Flap discs find their application in numerous sectors, including automotive, aerospace, construction, and metal fabrication. They are particularly effective in edge grinding, surface blending, deburring, and finishing tasks. One of the key benefits of flap discs is their ability to conform to complex shapes and contours, making them ideal for applications requiring precision and flexibility.
In the automotive industry, for instance, flap discs are used for the preparation and finishing of body panels, allowing for a smooth surface ready for painting. In metal fabrication, they excel in removing weld seams while providing a finish that reduces the need for subsequent polishing processes. These discs are also valuable in the aerospace sector, where weight reduction and surface integrity are critical.
flap disk 4
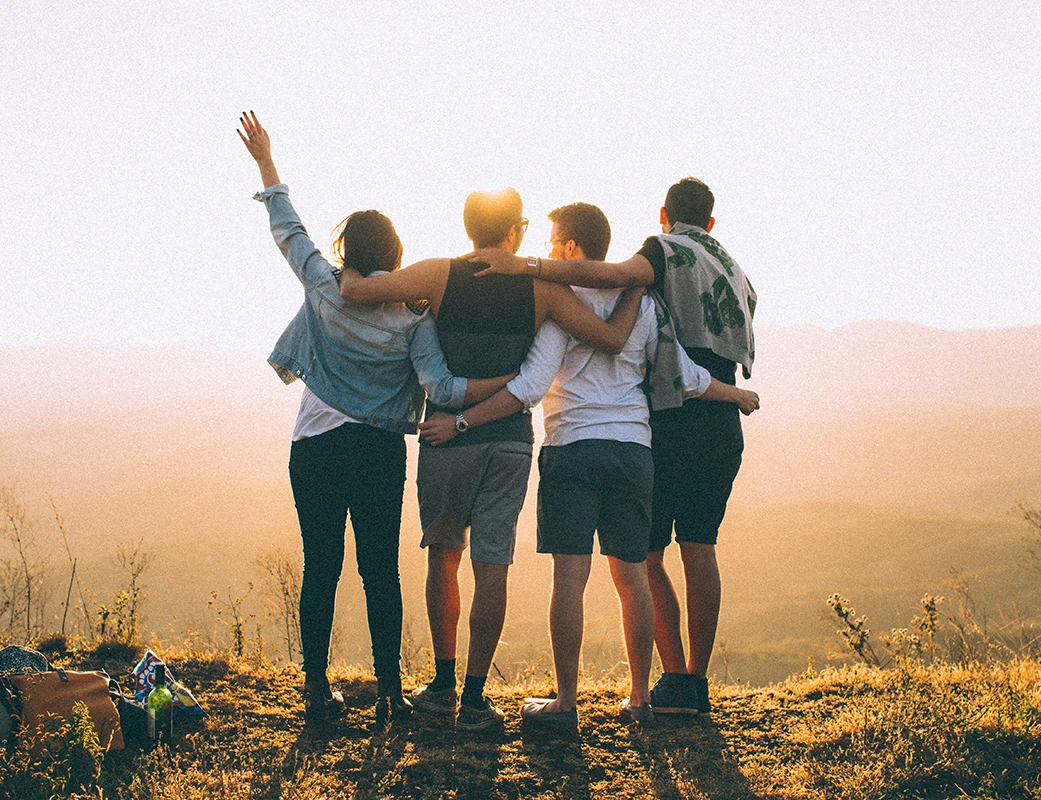
The Advantages of Flap Disks
1. Efficiency and Longevity Flap discs provide a higher material removal rate compared to traditional grinding wheels. Their unique design allows for consistent performance, leading to longer tool life and reduced costs over time. Users often find that flap discs can outperform conventional abrasives, resulting in fewer replacements and lower operational expenses.
2. Heat Management The open structure and cooling action of flap discs help to dissipate heat during use. This is particularly advantageous when working with heat-sensitive materials, such as aluminum and certain alloys, which may warp or become brittle under excessive heat.
3. Safety Flap discs are generally considered safer to use than rigid grinding wheels. The flexible nature of the flaps allows for greater control, reducing the risk of kickback. Additionally, flap discs are less prone to breaking, providing an added layer of safety for operators.
4. Versatility One of the standout features of flap discs is their versatility. They come in different grits and configurations to tackle various applications, from heavy grinding to fine finishing. This adaptability makes them a go-to choice for many professionals, as they can rely on a single tool for a range of tasks.
Conclusion
Flap discs represent a significant advancement in abrasive technology, catering to the diverse needs of modern industrial environments. As professionals continue to seek solutions that enhance productivity while ensuring safety and precision, flap discs are poised to remain a staple in the toolkit of metalworkers around the globe. Their innovative design, coupled with distinct advantages over traditional grinding methods, positions flap discs as an essential component in the future of industrial grinding and surface preparation. Whether you're engaged in heavy-duty metal fabrication or fine finishing applications, embracing flap discs can enhance your efficiency and effectiveness in the workshop.
Post time:Nov - 20 - 2024