Understanding the Importance of Flap Wheels in Industrial Applications
In the realm of industrial manufacturing and surface finishing, flap wheels have emerged as indispensable tools. Specifically, the flap wheel, often categorized by its specific type such as flap wheel 4, has garnered attention for its efficiency and versatility. This article explores the features, benefits, applications, and maintenance of flap wheels, providing a comprehensive understanding of their importance in various industries.
What is a Flap Wheel?
Flap wheels are abrasive wheels made up of multiple overlapping flaps of abrasive material, typically arranged around a central hub. This design allows for a flexible and adaptable tool that can be used in various applications, including grinding, sanding, and polishing. The flap wheel 4 refers to a specific size and type, often characterized by its diameter and grit versatility, making it suitable for a range of tasks.
Key Features
1. Flexible Design The overlapping flaps enable the wheel to conform to different shapes and surfaces, ensuring even contact and consistent results. 2. Variety of Grains Flap wheels come in different abrasive materials, such as aluminum oxide, silicon carbide, and ceramic, allowing for custom applications based on the material being worked on.
3. Multiple Grit Options This tool is available in various grits, catering to different stages of surface preparation from heavy grinding to fine finishing.
4. Heat Dissipation The flap design allows air to circulate, helping to dissipate heat during operation, which minimizes the risk of warping or damaging the workpiece.
Benefits of Using Flap Wheels
The advantages of flap wheels, particularly flap wheel 4, are numerous
- Efficiency The design facilitates faster material removal and reduces the time spent on finishing tasks, increasing overall productivity.
- Consistent Finish The gentle pressure applied by the flaps ensures that the finish is uniform and smooth, which is crucial in high-precision applications.
flap wheel 4
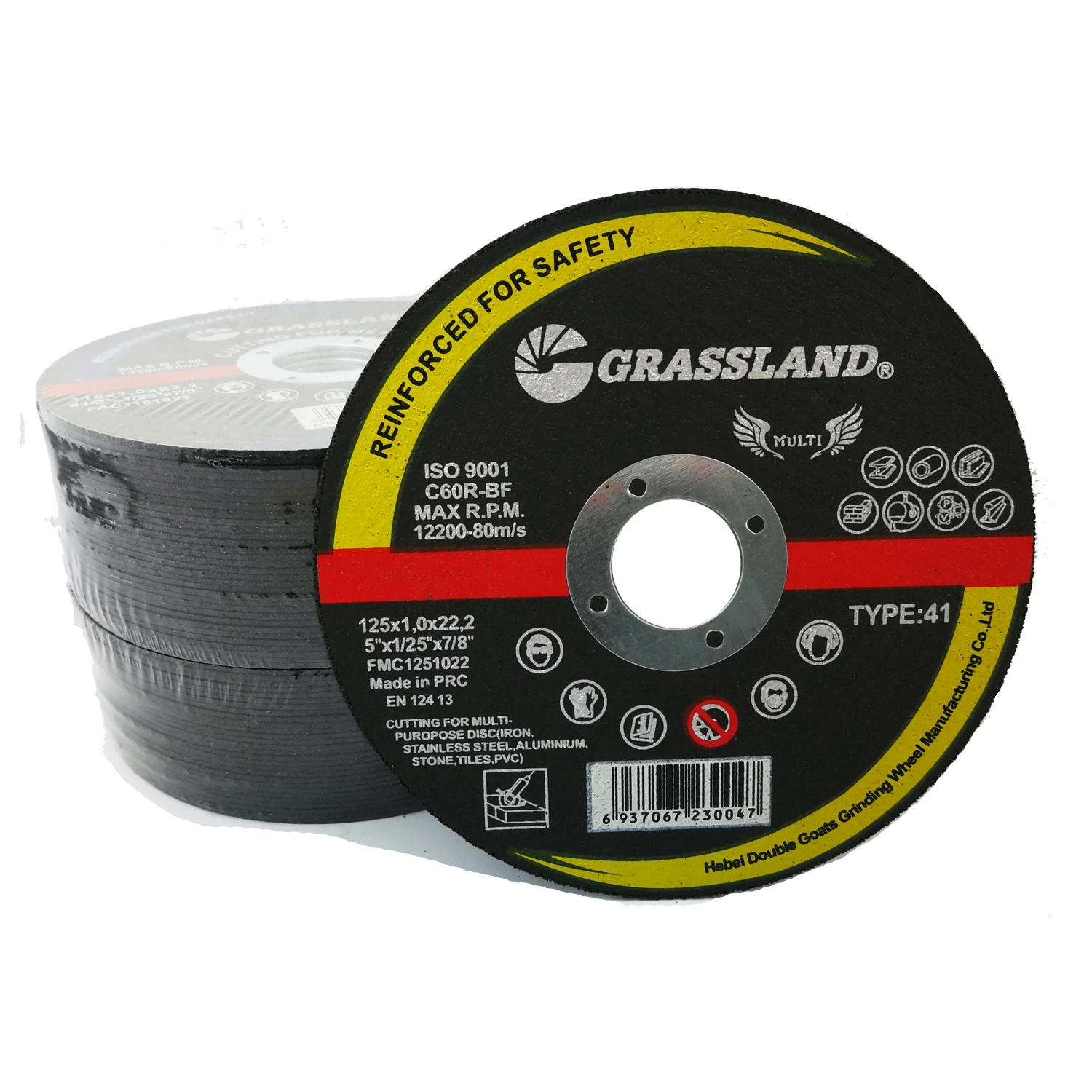
- Versatility Flap wheels are suitable for use on various materials, including metals, wood, plastic, and composites, making them a go-to solution for many industries.
- Ease of Use They can be easily mounted on different types of tools, such as angle grinders and rotary tools, making them accessible to both professionals and DIY enthusiasts.
Applications of Flap Wheels
Flap wheels find application across a wide array of industries, including
- Metalworking They are often used for deburring, polishing, and finishing metals, ensuring smooth edges and surfaces that are free from imperfections.
- Woodworking In the woodworking industry, flap wheels are utilized for sanding and finishing wooden surfaces, providing a quality finish that enhances the appearance of the final product.
- Automotive The automotive industry employs flap wheels for tasks ranging from bodywork to engine component finishing, where a fine surface finish is critical.
- Aerospace Given their precision, flap wheels are also used in aerospace for the preparation and finishing of parts that require strict adherence to specifications.
Maintenance and Safety Tips
To maximize the lifespan and performance of flap wheels, proper maintenance is essential. Regularly inspect flap wheels for wear and replace them as needed to ensure optimal performance. Moreover, always adhere to safety guidelines, such as wearing protective eyewear and using the tools in accordance with manufacturer recommendations, to prevent accidents.
Conclusion
In conclusion, flap wheels, including flap wheel 4, play a crucial role in various industrial applications. Their unique design and versatility make them an essential tool for achieving high-quality finishes on a wide range of materials. Understanding their features, benefits, and proper maintenance can help users harness the full potential of flap wheels, ultimately enhancing productivity and quality in their projects. As industries continue to evolve, the relevance of flap wheels in achieving precision and efficiency will remain significant, marking them as essential tools in the manufacturing landscape.
Post time:Dec - 05 - 2024