Understanding Flap Wheel Discs The Essential Tool for Metalworking and Finishing
Flap wheel discs have become an indispensable tool in the metalworking and finishing industries. Their unique structure and versatile applications make them a go-to choice for professionals and hobbyists alike, whether for deburring, sanding, polishing, or cleaning various surfaces. This article will delve into the characteristics, applications, and benefits of flap wheel discs, illuminating why they are favored in workshops around the world.
What Are Flap Wheel Discs?
Flap wheel discs consist of multiple overlapping abrasive flaps attached to a central hub. These flaps are made from various materials, including aluminum oxide, silicon carbide, and ceramic. Each material has its unique properties, lending itself to different applications and types of work. The flaps are arranged radially around the hub, allowing for efficient sanding and polishing without the risk of damaging the workpiece. This design allows flap wheels to conform to curves and contours more effectively than traditional grinding wheels.
Applications of Flap Wheel Discs
Flap wheel discs are incredibly versatile and can be used in various applications. Some of the most common uses include
1. Deburring After cutting or machining metal parts, burrs often form on the edges. Flap wheel discs are ideal for removing these imperfections, ensuring a smooth and safe finish. 2. Sanding Whether working with wood, metal, or plastic, flap wheels can provide a fine finish by removing surface imperfections and preparing surfaces for painting or finishing.
3. Polishing Flap wheels can be used with polishing compounds to achieve a mirror-like finish on metals. This application is particularly useful in jewelry making and automotive detailing.
4. Cleaning In industrial settings, flap discs can remove rust, oxidation, and old paint from surfaces, restoring them to optimal condition.
Advantages of Using Flap Wheel Discs
flap wheel disc
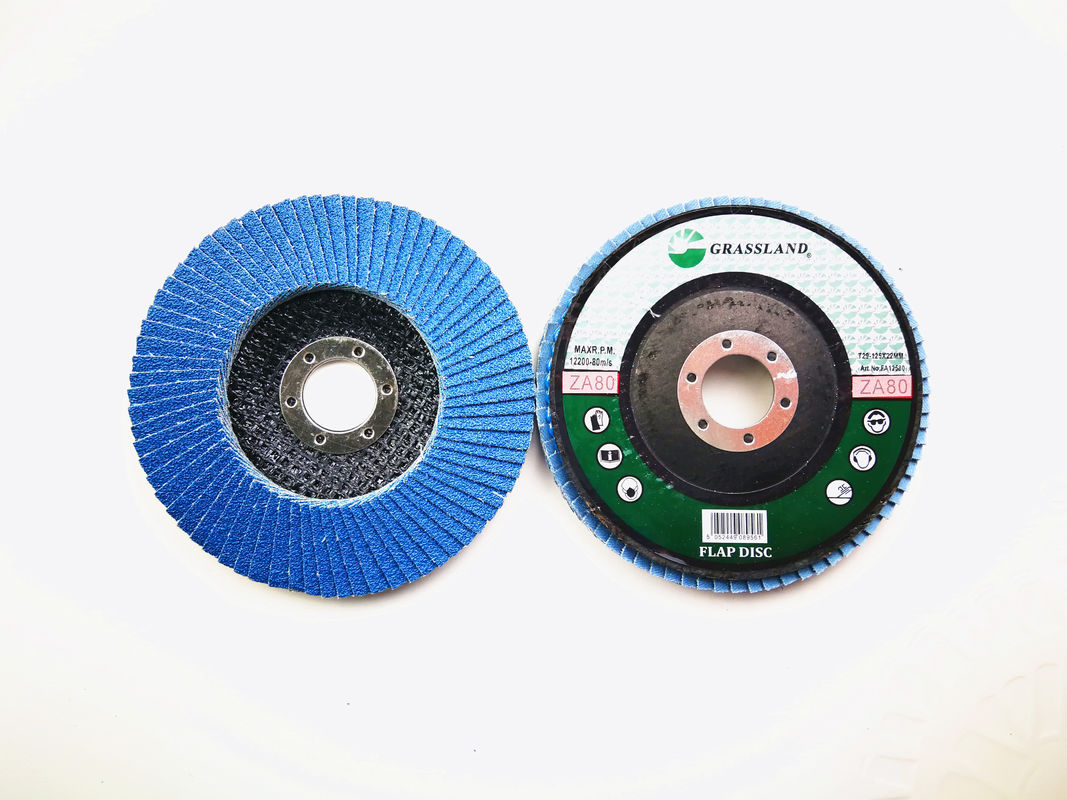
Flap wheels offer several advantages over traditional abrasives, making them a preferred choice in many applications
1. Flexibility The overlapping flaps provide exceptional flexibility, enabling the user to follow the contours of the workpiece better than rigid wheels or disks.
2. Cooler Operation Flap wheels typically run cooler than solid abrasive wheels. This feature is crucial because excessive heat can damage sensitive materials or alter the properties of the workpiece.
3. Longer Life The design of flap wheels allows for an even wear pattern, which extends their life compared to standard abrasive wheels that can wear unevenly.
4. Less Aggressive on Surfaces Flap wheels can provide a gentle touch, making them perfect for applications where the material surface should not be overly abraded or damaged.
5. Diverse Range They are available in a wide range of sizes, grits, and materials, making it easy to find the right flap wheel for any specific task.
Choosing the Right Flap Wheel Disc
When selecting a flap wheel disc, it's essential to consider several factors such as the material of the workpiece, the desired finish, and the type of machine you will be using. Grit size is crucial; finer grits are better for polishing and finishing, while coarser grits work well for heavy material removal. Material selection also plays a critical role—ceramic flap wheels might be preferable for high-performance applications, while aluminum oxide is often sufficient for general-purpose use.
Conclusion
Flap wheel discs are a vital tool in the arsenal of metalworkers, woodworkers, and craftsmen. Their versatility and effectiveness in various applications make them a popular choice across many industries. Understanding how to choose and use flap wheel discs effectively can significantly enhance the quality of your work and streamline your processes. As technology evolves, so too will the designs and applications of these indispensable tools, ensuring they remain a vital component of metalworking and finishing for years to come.
Post time:Dec - 18 - 2024