Understanding Flap Wheel Discs Essential Tools for Surface Finishing
Flap wheel discs are indispensable tools in the realm of surface finishing and material preparation. These versatile abrasives are commonly used in various industries, including metal fabrication, automotive, woodworking, and even jewelry making. Their design and functionality set them apart, making them a preferred choice for many professionals and hobbyists alike.
What Are Flap Wheel Discs?
Flap wheel discs consist of multiple overlapping segments or flaps made from an abrasive material, usually aluminum oxide or zirconia. These flaps are attached to a central spindle or hub, allowing them to flex and conform to the surface being worked on. The unique arrangement of the flaps not only increases the surface area for contact but also provides a consistent sanding effect, minimizing the risk of gouging the material.
The design of flap wheel discs allows them to deliver flexibility and durability. When used on surface materials, they can adapt to contours and irregularities, making them ideal for finishing uneven surfaces. As the flaps wear down, they expose fresh abrasive material, ensuring that the disc maintains its effectiveness over time.
Types of Flap Wheel Discs
There are several types of flap wheel discs available, designed for specific applications. The primary variations include
1. Coarse Flap Wheels These are used for aggressive material removal. Their larger and rougher abrasive grains help in removing old paint, rust, or corrosion from metal surfaces. These discs are ideal for initial sanding or shaping before finishing.
2. Medium Flap Wheels With a balanced abrasive grit, medium flap wheels are suitable for both material removal and finishing. They are commonly used in automotive bodywork and metal fabrication processes, where moderate grinding and smoothing are required.
flap wheel disc
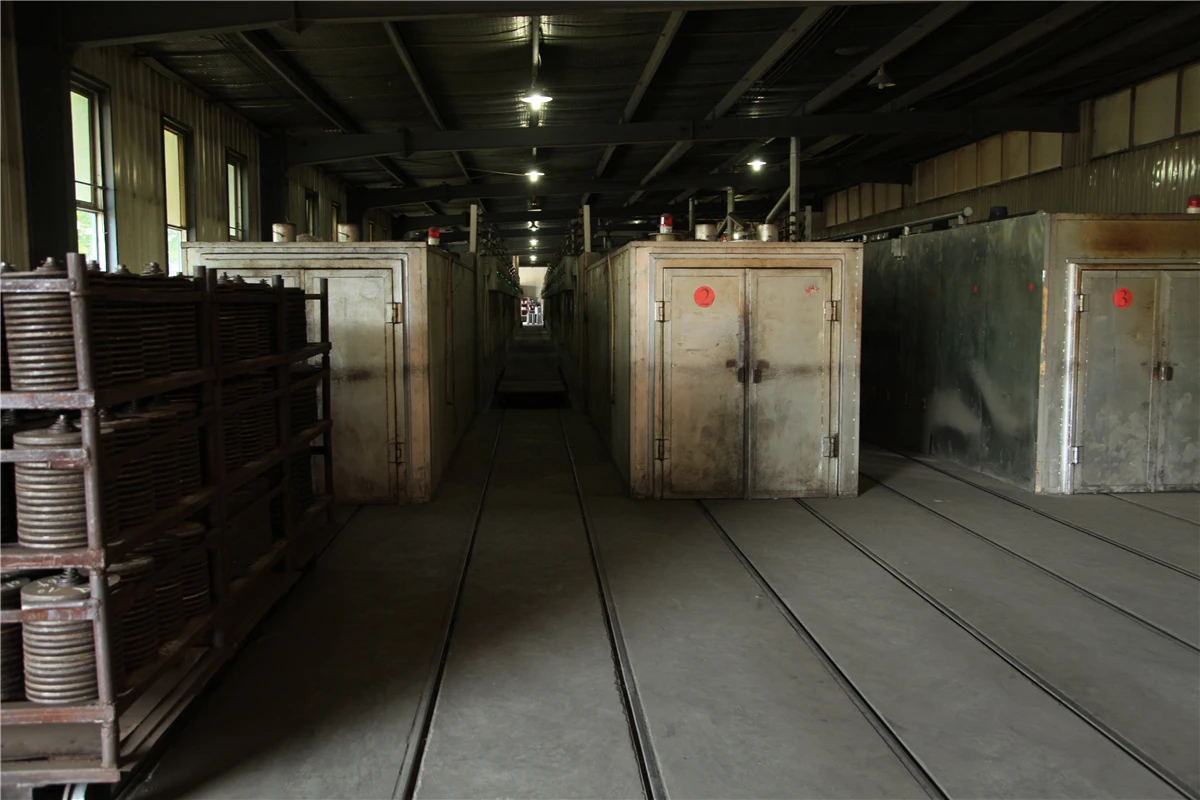
3. Fine Flap Wheels These discs provide a smoother finish and are often used for polishing and final surface preparation. Fine flap wheels are perfect for achieving a satin-like finish on materials such as stainless steel and aluminum.
Applications of Flap Wheel Discs
The applications for flap wheel discs are vast. In metalworking, they are primarily used for deburring, blending, and finishing metal parts. In woodworking, they help in sanding curves and contours that traditional sanders may struggle to reach. Additionally, flap wheel discs are effective in cleaning and finishing intricate designs in jewelry making, providing artisans with a tool that enhances their precision.
Moreover, flap wheels can be used for both dry and wet sanding processes. When paired with a suitable backing pad, they can also be utilized on bench grinders and angle grinders, further expanding their versatility. This adaptability makes flap wheel discs a fundamental tool in not only industrial settings but also in DIY and craft applications.
Advantages of Using Flap Wheel Discs
One of the primary advantages of using flap wheel discs is their efficiency. They remove material faster than traditional sanding methods while providing a consistent finish. Furthermore, the flexibility of the flaps reduces the likelihood of damaging surfaces, allowing for more controlled and precise work.
Additionally, the longevity of flap wheel discs is noteworthy. As they wear down, the continuous exposure of fresh abrasive material ensures that the discs remain effective for extended periods. This durability translates to cost savings for users, as flap wheel discs require less frequent replacement.
Conclusion
In summary, flap wheel discs are essential tools in the surface finishing industry, catering to a variety of applications across multiple sectors. Their unique design, versatility, and efficiency make them an invaluable asset for achieving smooth and polished surfaces. Whether in industrial environments or home workshops, flap wheel discs continue to prove their worth as effective and reliable abrasive tools. Understanding their types and applications can significantly enhance any project that demands high-quality finishing.
Post time:Oct - 07 - 2024