Understanding Flap Wheels for Metal Finishing
In the world of metalworking, precision and quality are paramount. One of the tools that has gained significant popularity for finishing metal surfaces is the flap wheel. This versatile tool is an essential part of any metalworking shop, known for its efficiency in smoothing, polishing, and deburring a variety of metal surfaces. This article will delve into flap wheels specifically designed for metal, exploring their construction, advantages, applications, and how to choose the right flap wheel for your needs.
What is a Flap Wheel?
A flap wheel is made up of multiple overlapping sanding or grinding flaps attached to a central hub. The flaps are usually made from abrasive materials such as aluminum oxide, zirconia, or silicon carbide, which offer different levels of aggressiveness and endurance. Flap wheels come in various sizes, grits, and shapes, making them adaptable to a wide range of applications. They can be used on rotary tools, angle grinders, or bench grinders, providing flexibility in different working environments.
Advantages of Flap Wheels
One of the prominent advantages of flap wheels is their ability to create a smooth finish without leaving deep scratches on the workpiece. Unlike traditional grinding wheels that can be aggressive and detract from the finish quality, flap wheels provide a more refined approach. The design allows for continuous exposure of fresh abrasive material as the flaps wear down, ensuring longer tool life and consistent performance throughout their use.
Flap wheels also offer greater control during operation. Their ability to conform to the shape of the workpiece means they can reach intricate areas that are often challenging with other grinding tools. This feature makes flap wheels ideal for use on curved surfaces, contours, and welds, providing a uniform finish across complex shapes.
Applications of Flap Wheels
flap wheel for metal
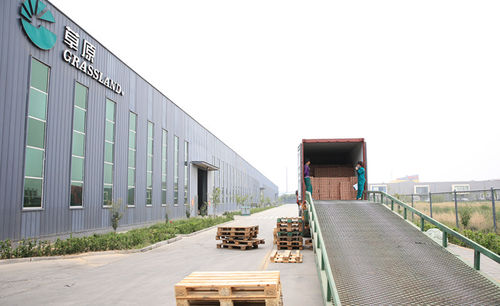
Flap wheels are widely used in various applications, including automotive, aerospace, and manufacturing industries. They are particularly valuable for tasks such as rust removal, surface preparation, paint stripping, and deburring. Fabricators often utilize flap wheels to prep surfaces for welding, ensuring a clean area that promotes stronger welds. Furthermore, flap wheels are suitable for use on a range of materials beyond metal, including wood and plastic, making them invaluable for mixed-material projects.
Choosing the Right Flap Wheel
Selecting the appropriate flap wheel for a specific task involves several considerations. Firstly, assess the material of the workpiece; different abrasive materials respond better to different metals. For instance, aluminum oxide is typically preferred for general-purpose grinding, while zirconia is more suitable for heavy stock removal and tough metals.
The grit size of the flap wheel is another crucial factor. Coarser grits (lower numbers) are effective for initial grinding and material removal, while finer grits (higher numbers) are ideal for finishing and polishing. Depending on the desired finish, workers may start with a coarser grit and then progress to finer grits to achieve the desired surface quality.
The size and shape of the flap wheel should also match the specific application. Larger wheels are suited for flat surfaces, while smaller wheels can handle intricate details. Moreover, the type of tool being used—whether an angle grinder or a rotary tool—will dictate the size and mounting type of the flap wheel.
Conclusion
Flap wheels are a vital tool in the metalworking industry, providing a blend of versatility, efficiency, and quality finishing. Whether it's smoothing rough edges, preparing surfaces for welding, or achieving a high polish, flap wheels adeptly handle various tasks with ease. By understanding their features, benefits, and appropriate application, metalworkers can enhance their productivity and ensure superior results in their projects. Investing in the right flap wheel will undoubtedly make a significant difference in the quality of your metal finishing efforts.
Post time:Nov - 29 - 2024