Understanding the Flat Flap Disc An Essential Tool in Modern Grinding and Polishing
In the world of metalworking and fabrication, efficiency and precision are paramount. One of the tools that has revolutionized grinding and polishing is the flat flap disc. These innovative discs combine the practicality of traditional grinding wheels with the versatility of flap sanders. This article aims to explore the features, uses, advantages, and maintenance of flat flap discs, emphasizing their importance in various industrial applications.
What is a Flat Flap Disc?
A flat flap disc is composed of multiple pieces of abrasive material arranged in a fan-like pattern around a central hub. This design allows for a larger surface area to come into contact with the workpiece, making it highly effective for both grinding and finishing tasks. Typically made from materials such as alumina, zirconia, or ceramic, flat flap discs vary in grit size, allowing users to choose the appropriate disc for their specific needs.
Applications in Industry
Flat flap discs have found widespread applications in various industries, including metal fabrication, woodworking, and automotive repair. In metalworking, they are used to smooth out weld seams, remove surface imperfections, and prepare surfaces for painting or coating. In woodworking, flat flap discs help achieve a finer finish on wooden surfaces by enabling effortless sanding and shaping.
Moreover, these discs are excellent for working on contoured surfaces and edges, making them suitable for intricate projects that require precise attention to detail. Their versatility allows them to be used on a range of materials, including steel, aluminum, and even plastic, making them an invaluable tool for artisans and tradespeople alike.
Advantages of Using Flat Flap Discs
One of the primary advantages of flat flap discs is their efficiency
. Due to their design, they can remove material faster than traditional grinding wheels, reducing the time spent on tasks without compromising quality. This enhanced productivity is crucial in industries where time is money, such as manufacturing and automotive repair.flat flap disc
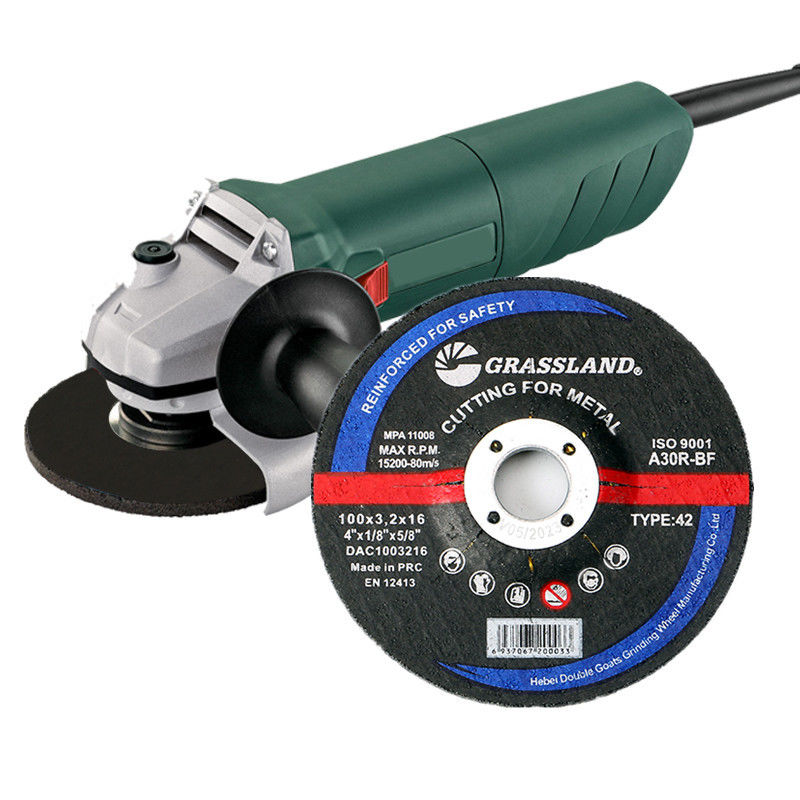
Additionally, flat flap discs produce less heat during operation compared to traditional grinding methods. The reduced heat generation minimizes the risk of damaging the workpiece, particularly when working with heat-sensitive materials like aluminum. This characteristic also leads to longer tool life, as excessive heat can wear down abrasives more quickly.
Another significant benefit is the smoother finish achieved when using flat flap discs. The layered abrasive flaps allow for a controlled removal of material, which results in a polished surface that may require less subsequent finishing. This attribute is especially beneficial in applications where appearance is crucial, such as in the automotive or architectural industries.
Selecting the Right Flat Flap Disc
When choosing a flat flap disc, several factors must be considered. The type of material being worked on, the desired finish, and the required grit size are essential elements that will influence the selection process. Coarser grits (e.g., 40-80) are ideal for aggressive material removal, while finer grits (e.g., 120-600) are suitable for finishing and polishing tasks.
It is also essential to consider the design of the flap disc. Flat flap discs are typically used for flat surfaces, whereas conical flap discs are better suited for edges and corners. Understanding the specific requirements of a project can help in selecting the appropriate disc for optimal results.
Maintenance Tips
To ensure the longevity and effectiveness of flat flap discs, proper maintenance and handling are essential. Users should ensure that the discs are stored in a dry environment, away from direct sunlight or extreme temperatures, as moisture can negatively affect their performance. Maintaining the speed settings on the grinding tool also plays a crucial role—using the correct RPM as recommended by the manufacturer can prevent premature wear of the abrasives.
In conclusion, flat flap discs are a cornerstone tool in the grinding and polishing arena. Their efficiency, versatility, and ability to deliver high-quality finishes make them an essential choice for professionals across various industries. By understanding their applications and maintaining them properly, users can enhance their workflow and achieve outstanding results in their projects.
Post time:Dec - 11 - 2024