Granite Grinding Wheels The Essential Tool for Stone Fabrication
Granite, with its natural beauty and durability, has become an increasingly popular choice for countertops, flooring, and various other architectural applications. However, working with granite can be challenging due to its hardness, making the quality of the tools used extremely important. One such essential tool in the stone fabrication industry is the granite grinding wheel. This article will delve into the features, types, applications, and maintenance of granite grinding wheels, highlighting their significance in the stoneworking process.
Understanding Granite Grinding Wheels
Granite grinding wheels are specialized tools designed specifically for shaping, smoothing, and finishing granite surfaces. Made from a combination of abrasive materials and bonding agents, these wheels can withstand the intense pressures and temperatures associated with grinding stone. The primary component of a grinding wheel is the abrasive material, which can include diamond, aluminum oxide, or silicon carbide. Among these, diamond is the most effective material for grinding granite due to its superior hardness and longevity.
Features of Granite Grinding Wheels
1. Material Composition Diamond grinding wheels are constructed with a diamond abrasive layer that ensures efficient removal of material while producing a smooth finish. The diamond particles are embedded in a metal or resin bond, which determines the wheel’s aggressiveness and durability.
2. Bond Type The bond type of a grinding wheel greatly influences its performance. Resin bonds provide a softer and more flexible grinding action, ideal for achieving a fine finish on granite surfaces. In contrast, metal bonds are more rigid and are suitable for aggressive grinding and shaping, making them perfect for heavy-duty applications.
3. Grit Size The grit size of the grinding wheel plays a critical role in determining the finish of the processed stone. Coarse grits are used for aggressive material removal, while finer grits are utilized for polishing and achieving a gloss finish. Selecting the appropriate grit size is essential for achieving the desired results.
Types of Granite Grinding Wheels
Granite grinding wheels come in various types, each suited for specific tasks in the stoneworking process
1. Cup Wheels These are used for grinding and shaping the edges of granite slabs. They have a rounded shape that allows for easy maneuverability and access to corners.
2. Flat Wheels Ideal for flat and large surfaces, flat wheels are used for heavy material removal and surface leveling.
3. Polishing Wheels These wheels have finer grits, designed for the final stages of granite processing. They deliver the smooth finish characteristic of high-quality stonework.
granite grinding wheel
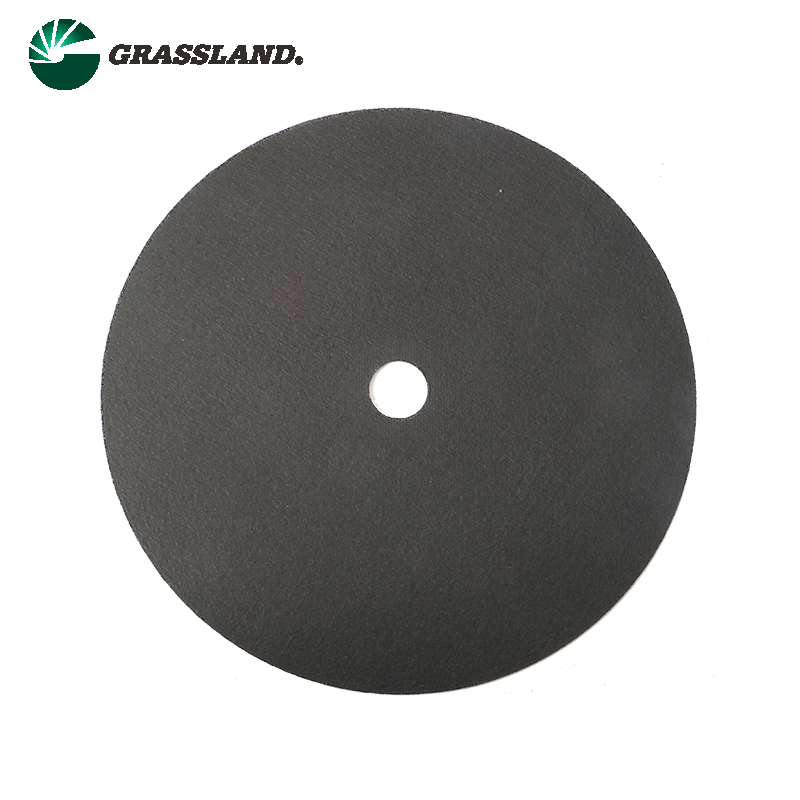
4. Diamond Core Bits While not traditional grinding wheels, these tools are essential for creating holes in granite. They feature diamond segments that are extremely effective at cutting through the tough stone.
Applications of Granite Grinding Wheels
Granite grinding wheels are used in various applications, including
- Countertop Fabrication In the creation of granite countertops, grinding wheels are used to shape the edges and surfaces to precise measurements. They ensure that the slab fits properly within the kitchen or bathroom space.
- Flooring Installation When installing granite tiles, grinding wheels help level the surface and remove any imperfections, ensuring a seamless fit.
- Monument and Headstone Manufacturing Granite grinding wheels are instrumental in shaping and finishing monuments and headstones, allowing for intricate designs and inscriptions.
Maintenance of Granite Grinding Wheels
Proper maintenance of granite grinding wheels extends their lifespan and efficiency. Here are some tips for ensuring optimal performance
1. Regular Inspection Check the wheels for signs of wear and damage. Replace any wheels that show significant signs of wear, as they may produce subpar results.
2. Cleaning After use, clean the grinding wheels to remove any residual stone particles. This prevents clogging and ensures consistent performance.
3. Proper Storage Store grinding wheels in a dry and stable environment to prevent moisture damage and warping.
Conclusion
Granite grinding wheels play an indispensable role in the stone fabrication industry. Their specialized design and robust materials make them well-suited for the unique challenges of working with granite. By understanding the features, types, applications, and maintenance of these wheels, professionals can enhance their stoneworking projects, ensuring high-quality results that highlight the natural beauty of granite. As technology continues to advance, so too will the efficiency and capability of granite grinding wheels, ensuring they remain a fundamental tool in stone fabrication for years to come.
Post time:Oct - 09 - 2024