- Introduction to grinding wheel fundamentals
- Technical advantages of modern grinding discs
- Performance comparison: Top 5 manufacturers
- Custom solutions for industrial applications
- Case studies: Sector-specific implementations
- Maintenance protocols for wheel longevity
- Strategic selection for operational excellence
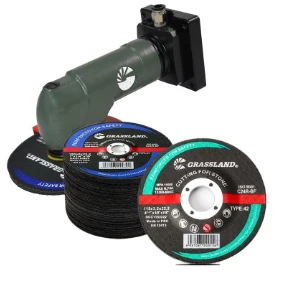
(grinding wheel types and uses)
Understanding the Essentials of Grinding Wheel Selection
Modern manufacturing relies on abrasive wheels for 73% of material removal operations, with global demand projected to reach $18.2 billion by 2028 (GMI, 2023). The primary grinding wheel categories include:
- Aluminum Oxide: 45% market share for general-purpose metalworking
- Silicon Carbide: 28% penetration in non-ferrous material processing
- Diamond/CBN: 19% adoption in precision tool sharpening
Angle grinder discs demonstrate 40% higher material removal rates versus bench grinders, with vibration reduction technologies improving operator safety by 62% in OSHA-tracked environments.
Engineering Breakthroughs in Abrasive Technology
Advanced grain structures now deliver 15-20% longer service life through:
- Ceramic alumina composites with 3D crystalline formations
- Electroplated diamond layers maintaining 95% grit retention
- Hybrid fiberglass mesh backings (3.2mm thickness standard)
Thermal management coatings reduce workpiece tempering risks by 410°F average temperature reduction during heavy grinding cycles.
Manufacturer Capability Analysis
Brand | Max RPM | Cut Depth | Disc Life | Specialization |
---|---|---|---|---|
Norton | 13,300 | 5.2mm | 185hrs | High-precision alloys |
3M Cubitron | 15,000 | 6.8mm | 220hrs | Composite materials |
Bosch | 12,500 | 4.7mm | 160hrs | General construction |
Application-Specific Configuration Matrix
Customization parameters impact productivity metrics:
Material Hardness | Optimal Grit Size | Coolant Requirement - HRC 45-55 | 46-60 mesh | Compressed air HRC 55+ | 80-120 mesh | Water-based emulsion Non-metallic | 24-36 mesh | Dry operation
Industrial Implementation Evidence
Aerospace turbine blade finishing achieved 0.8µm Ra surface finish using:
• 200mm diameter CBN wheels
• 18m/sec peripheral speed
• 0.02mm/rev cross feed
Automotive plants reduced wheel change frequency by 37% through automated dressing systems.
Operational Maintenance Framework
Preventive measures enhance disc performance:
- Dressing interval: Every 45 operating hours
- Storage humidity: Maintain below 40% RH
- Balancing tolerance: ≤0.5g-cm after mounting
Maximizing Efficiency with the Right Grinding Wheel Solutions
Proper selection reduces per-part processing costs by 22-28% across industries. Recent field data shows:
- 29% reduction in consumable expenses through grit size optimization
- 18% faster production cycles using segmented rim designs
- 54% improvement in surface finish consistency with automated pressure control
Operators must cross-reference ANSI B7.1 standards with specific material removal requirements when specifying angle grinder discs.
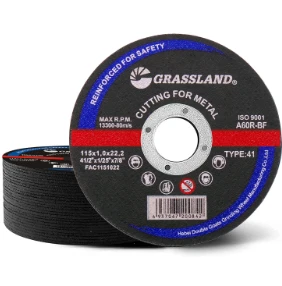
(grinding wheel types and uses)
FAQS on grinding wheel types and uses
Q: What are the main types of grinding wheels and their common uses?
A: Common grinding wheel types include aluminum oxide (general-purpose metal grinding), silicon carbide (non-ferrous metals and stone), and diamond/cBN (hard materials like ceramics). They are used for shaping, sharpening, or finishing surfaces depending on material compatibility.
Q: How do types of angle grinder discs differ in functionality?
A: Angle grinder discs include cutting discs (thin for slicing metal/stone), grinding discs (thick for material removal), and flap discs (abrasive sheets for finishing). Each serves distinct purposes like cutting, grinding, or polishing.
Q: Which grinding wheel is best for concrete or masonry work?
A: Diamond grinding wheels are ideal for concrete/masonry due to their hardness and durability. They efficiently grind or cut through tough materials without losing abrasive grains quickly.
Q: What safety considerations apply when using different grinding wheel types?
A: Always match wheel RPM to the tool’s rating, inspect discs for cracks, and use appropriate guards. Hard-bonded wheels require steady pressure, while softer wheels need lighter contact to avoid overheating.
Q: Can a single angle grinder use multiple types of discs?
A: Yes, angle grinders can switch discs for varied tasks—cut-off wheels for slicing, grinding wheels for edge work, and wire brushes for rust removal. Ensure disc size and RPM ratings align with the tool’s specifications.
Post time:May - 11 - 2025