The Importance of Grinding and Polishing Flap Discs in Metalworking
In the world of metalworking and fabrication, the tools used can significantly impact the quality and efficiency of the final product. One such tool that has gained prominence is the grinding and polishing flap disc. These discs are essential for a variety of applications, including grinding, blending, and polishing metal surfaces. Understanding their features, applications, and benefits can help manufacturers and craftsmen choose the right tools for their projects.
What Are Flap Discs?
Flap discs are abrasive tools made from multiple overlapping layers, or flaps, of abrasive material that are attached to a backing plate. This design allows for a flexible and conformable grinding solution that can adapt to the surface contours of the workpiece. Typically made from materials such as aluminum oxide or zirconia, flap discs are available in various grits to suit different tasks, from heavy grinding to fine polishing.
Applications of Flap Discs
Flap discs are versatile and can be used in various applications, including
1. Metal Fabrication They are ideal for removing welds, fins, and other surface imperfections on weldments and metal fabrications, improving the overall appearance and quality of the metal work.
2. Deburring Flap discs effectively remove burrs and sharp edges from cut or machined parts, ensuring safety and precision in the finished product.
3. Surface Preparation These discs prepare surfaces for painting or coating by providing a clean and smooth finish that enhances adhesion.
Benefits of Using Flap Discs
grinding and polishing flap disc
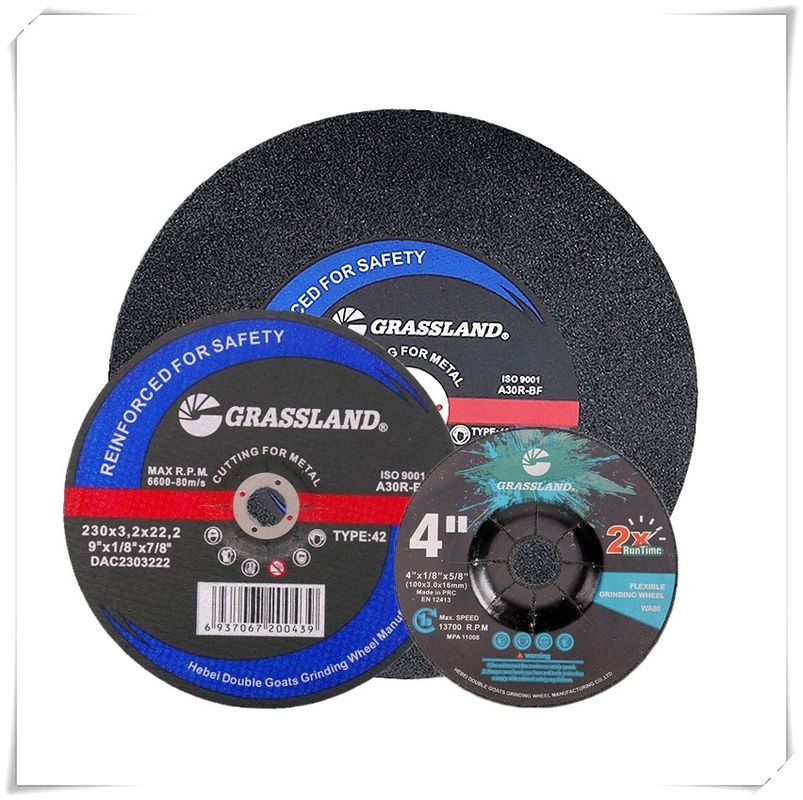
The growing popularity of flap discs in metalworking can be attributed to several key benefits
- Efficiency Flap discs remove material quickly while producing less heat, reducing the risk of warping or damaging the workpiece. Their design allows for faster material removal compared to traditional grinding wheels.
- Versatility With various grits available, flap discs can transition seamlessly from grinding to polishing tasks, making them suitable for a range of applications.
- User-Friendly Flap discs are easy to use, and their flexibility allows for comfortable handling and control. This makes them a preferred choice for both professional fabricators and DIY enthusiasts.
- Durability The layered structure of flap discs tends to provide longer life compared to conventional grinding wheels. They produce less clogging, maintaining efficiency throughout their lifespan.
- Cost-Effectiveness While the initial investment might be higher than traditional abrasives, the durability and efficiency of flap discs often lead to lower overall costs in terms of time and replacement.
Choosing the Right Flap Disc
Selecting the appropriate flap disc depends on several factors, including the material being worked on, the desired finish, and the specific application. It is vital to consider the grit size, type of abrasive material, and the backing plate's characteristics. For instance, coarse grits are suited for heavy grinding tasks, while finer grits are better for polishing and finishing.
Additionally, the shape of the flap disc—such as flat, conical, or depressed center—should align with the specific requirements of the job at hand. This ensures optimal performance while safeguarding the integrity of the workpiece.
Conclusion
Grinding and polishing flap discs are invaluable tools in the metalworking industries, providing efficiency, versatility, and high-quality finishes. By understanding their applications and benefits, individuals can make informed decisions about their use, leading to superior results in their projects. Whether in industrial settings or home workshops, flap discs are an investment worth considering for anyone committed to achieving excellence in metal fabrication.
Post time:Nov - 27 - 2024