The Importance of Grinding and Polishing Flap Discs in Metalworking
In the metalworking industry, the quality of the finished product is paramount. Whether it's for aesthetic appeal or the functionality of components, achieving a smooth and refined surface finish is essential. One of the most effective tools for achieving these results is the grinding and polishing flap disc. These versatile tools are integral in various applications, making them indispensable in workshops and manufacturing settings.
What are Flap Discs?
Flap discs are composite tools made up of multiple layers of abrasive material mounted on a central base disc. They come in different grades of abrasiveness, allowing for a range of grinding and polishing tasks. The flaps, or overlapping layers of abrasive material, provide a significant surface area to work with, ensuring efficient material removal. They are typically made from aluminum oxide or zirconia, which offers durability and effectiveness for various grinding, sanding, and finishing applications.
Applications of Flap Discs
Flap discs are widely used in different metalworking industries, including fabrication, automotive repair, and construction. They can be utilized on various metals, such as steel, stainless steel, and aluminum, making them extremely versatile. The primary applications include
1. Grinding The aggressive nature of flap discs allows for quick material removal. They are often used for surface preparation, removing weld seams, and eliminating rust or corrosion from metal surfaces.
2. Polishing After the grinding process, flap discs can be used for polishing to achieve a smooth, high-gloss finish. This is particularly important in industries where aesthetics are crucial, such as in metal art or high-end automotive finishes.
3. Deburring Flap discs effectively remove sharp edges and burrs from machined parts, improving safety and functionality. This process is vital to ensure that components fit together properly without the risk of injury or damage.
4. Finishing They can be used for final finishing touches, ensuring that the surface meets specifications for smoothness and uniformity.
Advantages of Using Flap Discs
The advantages of flap discs over traditional bonded abrasives are numerous
grinding and polishing flap disc
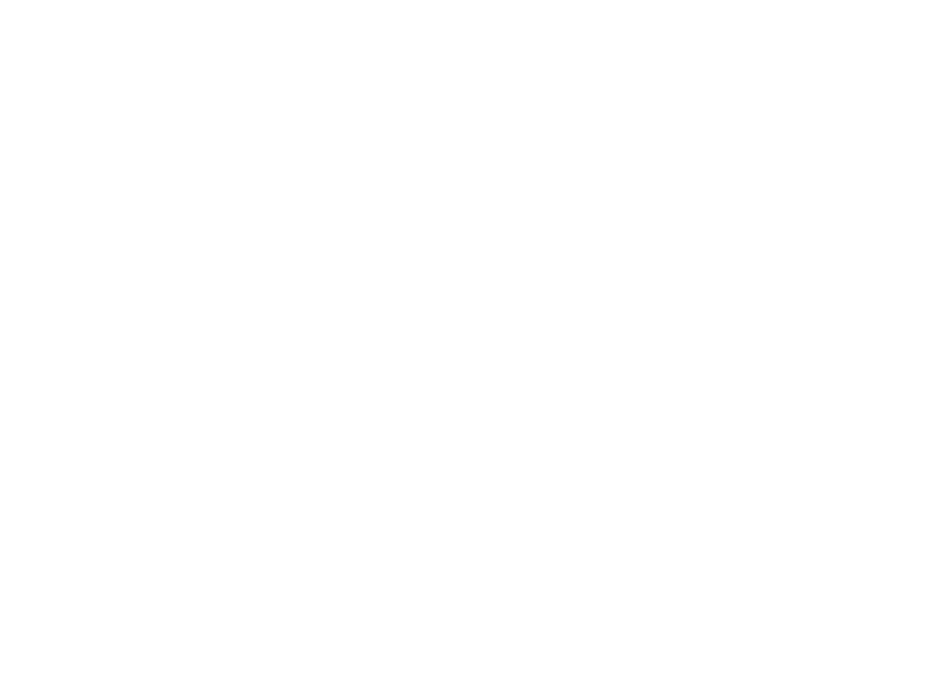
- Versatility Flap discs can perform multiple functions—grinding, polishing, and finishing—making them a one-stop solution for various tasks.
- Consistency The design of flap discs allows for uniform wear and consistent abrasive performance throughout their lifespan. This means operators can achieve consistent results over long periods.
- Low Vibration and Noise Flap discs generate less vibration and noise compared to other grinding tools. This makes them more user-friendly and reduces operator fatigue during prolonged use.
- Enhanced Control The flexibility of flap discs allows them to conform to the contours of the workpiece, providing better control during grinding and polishing tasks.
- Reduced Heat Generation The design helps in dissipating heat during operation, which minimizes the risk of damaging the workpiece from excessive heat buildup.
Choosing the Right Flap Disc
When selecting a flap disc, it is crucial to consider the intended application. Factors such as the material being worked on, the desired finish, and the specific tasks need to be evaluated. Key considerations include
- Abrasive Material Choose between aluminum oxide for general-purpose sanding or zirconia for tougher applications like stainless steel grinding.
- Grain Size The coarser the grain, the more aggressive the cut. For initial grinding, a larger grain size may be ideal, while finer grains are better suited for polishing and finishing.
- Disc Size and Shape The size of the flap disc should match the tool being used (e.g., angle grinder) and the nature of the job. The shape can also determine the reach and effectiveness of the tool in constrained spaces.
Conclusion
In conclusion, grinding and polishing flap discs are invaluable tools in the metalworking industry. Their versatility, efficiency, and ability to provide high-quality finishes make them a go-to choice for professionals. By understanding their applications, advantages, and selection criteria, operators can maximize productivity and ensure that their finished products meet the highest standards of quality. As technology advances and new materials are developed, the role of flap discs will undoubtedly continue to evolve, securing their place as essential tools in every metalworker’s arsenal.
Post time:Dec - 17 - 2024