Understanding Grinding Wheels and Flap Discs Essential Tools for Metalworking and More
In the realm of metalworking, woodworking, and various industrial applications, grinding wheels and flap discs are indispensable tools that facilitate surface preparation, finishing, and sharpening. This article explores the characteristics, uses, and advantages of these two essential items in workshops and production environments.
Grinding Wheels Basics and Applications
Grinding wheels are used primarily for grinding metal, with their coarse texture allowing for effective material removal. They are made with abrasive particles bound together with a bonding agent, forming a rigid wheel. The choice of abrasive material and bonding agent greatly affects the grinding wheel's performance and suitability for specific tasks.
1. Materials Common abrasive materials include aluminum oxide, silicon carbide, and diamond. Each material has unique properties that make it ideal for different types of metal - Aluminum oxide is versatile and commonly used for steel and ferrous metals. - Silicon carbide is best for non-ferrous metals and provides a finer finish. - Diamond wheels are used for grinding hard materials like stone or concrete.
2. Bonding Agents These determine the wheel's grain retention and durability. Vitrified bonds offer strength and stability, while resin bonds provide flexibility and enhanced finish quality.
3. Applications Grinding wheels are prevalent in applications such as - Sharpening tools - Smoothing welds - Shaping metal parts - Polishing surfaces
While effective, grinding wheels often generate significant heat
. Therefore, proper techniques and equipment, including coolants, are essential to prevent damage to both the workpiece and the tool itself.Flap Discs Versatility and Ease of Use
Flap discs are a relatively newer innovation in the world of abrasives, offering several distinct advantages over traditional grinding wheels. They consist of multiple pre-mounted abrasive flaps attached to a backing plate, allowing for both grinding and finishing in a single tool.
grinding wheel flap discs
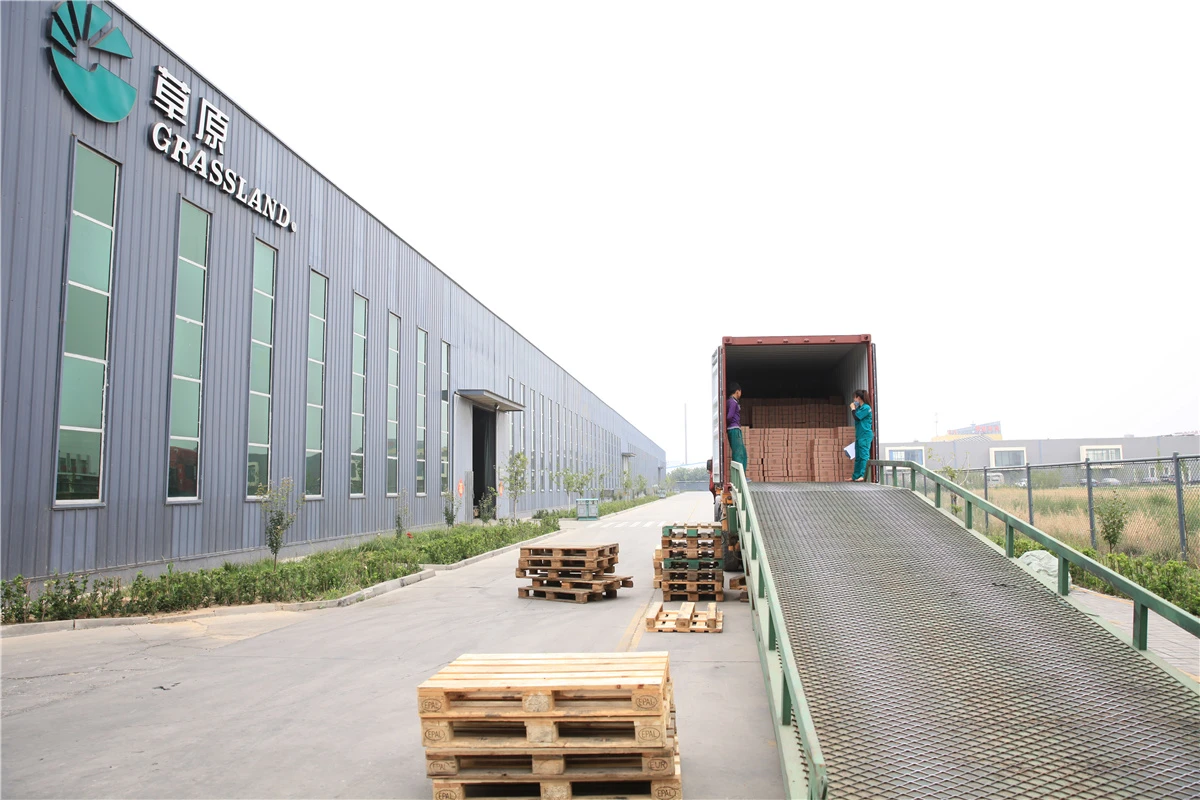
1. Structure The layered design of flap discs provides a larger surface area for material removal while maintaining flexibility, making them more forgiving on uneven surfaces. The overlapping flaps ensure a steady reduction of the workpiece without excessive gouging.
2. Materials Similar to grinding wheels, flap discs can be made from various abrasive materials - Zirconia alumina is known for its durability and is perfect for heavy stock removal and high-pressure applications. - Aluminum oxide flap discs are more suitable for lighter applications and finishing tasks.
3. Applications Flap discs are used for - Deburring and surface grinding - Smoothing edges and corners - Finishing welds - Preparing surfaces for painting or other coatings
Both portable grinders and stationary machines can use flap discs, making them incredibly versatile in a variety of settings, including automotive, aerospace, and metal fabrication industries.
Advantages of Using Grinding Wheels and Flap Discs
When evaluating grinding wheels and flap discs, several factors position these tools as essential components in any workshop
- Efficiency Flap discs remove material quickly while providing a finer finish, reducing the need for additional finishing steps. - Ease of Use The nature of flap discs allows for comfortable use on both flat and contoured surfaces. Their design minimizes user fatigue. - Cost-Effectiveness Given their durability and efficiency, flap discs can be a cost-effective option for many grinding applications compared to traditional wheels. - Safety Both tools come with safety ratings and proper usage guidelines, ensuring that users can operate them with minimal risk of accidents when following best practices.
Conclusion
In conclusion, grinding wheels and flap discs play vital roles in metalworking and other material processing industries. Understanding their distinct characteristics, applications, and advantages enables professionals to choose the right tool for their specific needs. With the right grinding equipment at hand, one can achieve high precision, efficiency, and excellent finishing results in various projects. Whether you are a hobbyist or an industrial tradesperson, mastering the use of these tools will significantly enhance your capabilities and overall output.
Post time:Dec - 17 - 2024