Understanding the Importance of Grinding Wheels for Brass
When it comes to machining materials like brass, the choice of an appropriate grinding wheel is crucial for achieving the desired results. Brass, an alloy primarily made of copper and zinc, presents unique challenges in terms of machining due to its physical properties. Selecting the right grinding wheel can enhance productivity, improve finish quality, and prolong the lifespan of tools.
The Characteristics of Brass
Brass is known for its excellent corrosion resistance, good thermal conductivity, and ease of machining. Its applications span various industries, including plumbing, electrical components, and decorative items. However, machining brass can be tricky. If the wrong grinding wheel is used, it can lead to issues such as excessive heat generation, workpiece burning, or poor surface finishes. Therefore, understanding the properties of brass and the nature of its grinding is essential.
Types of Grinding Wheels
Grinding wheels designed for brass can vary significantly in composition, bond type, and grit size. The most common types of grinding wheels used for brass include
1. Aluminum Oxide Wheels These are typically used for grinding non-ferrous metals like brass. They offer good cutting action and are economical, making them a popular choice for many machining tasks.
2. Silicon Carbide Wheels Ideal for hard and brittle materials, silicon carbide wheels provide a sharp cutting edge and are effective for achieving fine finishes on brass. They are particularly suitable for achieving intricate details.
3. Diamond Wheels Though more expensive, diamond grinding wheels are used for high precision and exceptional surface finishes. They are excellent for brass machining where minute tolerances are necessary.
Grit Size and Bond Types
The grit size of the grinding wheel is another critical factor. A larger grit size (e.g., 46 or 60) helps in rapid material removal, which is beneficial for aggressive grinding operations. Conversely, finer grits (e.g., 80 or 120) are better suited for achieving smoother finishes, reducing the risk of surface scratches.
grinding wheel for brass
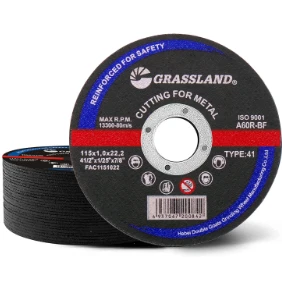
Bond types also play a role in the wheel's performance. Resin bonds are popular for their flexibility and quality finish, making them a good choice for precision work on brass. On the other hand, vitrified bonds provide greater rigidity and are suitable for high-speed applications where longevity is essential.
Cooling and Lubrication
When grinding brass, it's important to consider the cooling and lubrication of the process. Brass can be prone to overheating, which can lead to changes in its physical properties. Using a suitable coolant or lubricant during grinding not only dissipates heat but also prolongs the life of the grinding wheel. Water-soluble oils or synthetic coolants are commonly used, depending on the specific requirements of the machining operation.
Best Practices for Grinding Brass
To achieve optimal results when grinding brass, follow these best practices
1. Select the Right Wheel Choose a wheel that matches the material and desired finish. Consider factors like grit size and bond type.
2. Maintain Proper Speed and Feed Rates Adjust the speed of the grinding machine according to the wheel specifications and the material being machined to avoid overheating.
3. Use Coolants Wisely Apply coolant during the grinding process to prevent heat build-up and ensure a better finish.
4. Monitor Wheel Wear Regularly check the condition of the grinding wheel and replace it when necessary to maintain efficiency and quality.
Conclusion
In summary, selecting the right grinding wheel for brass is a critical component of successful machining. Understanding the properties of brass, along with the types of grinding wheels available, can significantly impact the overall quality and efficiency of the grinding process. By following best practices and paying attention to specifics such as grit size, bond type, and cooling methods, manufacturers can achieve superior results while prolonging the lifespan of their tools. With the right approach, the machining of brass can be both efficient and effective, meeting the rigorous demands of various industries.
Post time:Jan - 01 - 2025