Understanding Grinding Wheels for Stainless Steel Specifications and Selection
Grinding wheels are essential tools in various manufacturing processes, especially when it comes to machining and finishing stainless steel. This durable metal, known for its corrosion resistance and strength, calls for specialized grinding wheels that can effectively handle its unique properties without causing damage. In this article, we will explore the specifications of grinding wheels suitable for stainless steel, helping you make informed decisions for your machining needs.
Types of Grinding Wheels
When selecting a grinding wheel for stainless steel, it’s important to understand the various types available. The most commonly used grinding wheels include
1. Alumina Oxide Wheels These are the most common grinding wheels and are suitable for general-purpose grinding. Aluminum oxide wheels are versatile and work well on ferrous metals, including stainless steel, but with limitations in producing finer finishes.
2. Zirconia Alumina Wheels These wheels are designed for heavy-duty grinding operations. They feature a more durable abrasive that allows for faster grinding and longer life, making them ideal for stainless steel.
3. Ceramic Wheels Known for their high performance and longevity, ceramic wheels are suitable for precision grinding of stainless steel. They generate less heat and provide excellent surface finishes.
4. Diamond Wheels While traditionally used for hard materials, diamond wheels can be utilized for specific applications involving stainless steel, particularly where high precision is required.
Key Specifications to Consider
When selecting a grinding wheel for stainless steel, several specifications must be evaluated
grinding wheel for stainless steel specification
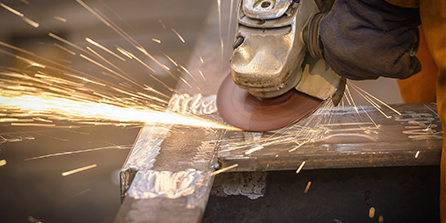
1. Abrasive Material The choice of abrasive material is crucial. For stainless steel, zirconia alumina and ceramic abrasives are recommended due to their ability to withstand higher temperatures and resist wear.
2. Wheel Size Grinding wheels come in various diameters and thicknesses. Depending on the application (surface grinding, cylindrical grinding, etc.), the right size must be chosen to ensure optimal performance.
3. Bond Type The bond holds the abrasive grains together. The most common types are vitrified and resin bonds. Vitrified bonds offer excellent stability and are best for heavy-duty grinding, while resin bonds are more flexible and can be ideal for fine finishing.
4. Grit Size Grit size indicates the coarseness of the grinding wheel. A finer grit size (e.g., 60-120) is typically used for finishing operations, while a coarser grit size (e.g., 24-60) is suited for stock removal.
5. Hardness The hardness of a grinding wheel affects its performance. Softer wheels wear faster and are suitable for hard materials, while harder wheels can be used for softer materials or when a finer finish is desired.
6. RPM Rating Ensure that the grinding wheel can operate at the machine's speed. The RPM (Revolutions Per Minute) rating should be matched with the grinder’s capabilities to prevent accidents or wheel failure.
Safety Considerations
When using grinding wheels, especially on stainless steel, safety is paramount. Always wear proper personal protective equipment (PPE) such as goggles, gloves, and hearing protection. Ensure that the grinding wheel is correctly mounted and that the grinder is stable before starting the operation. Regularly inspect the wheel for any signs of damage or wear, as a compromised wheel can lead to serious injuries.
Conclusion
Choosing the right grinding wheel for stainless steel is a critical decision that impacts the quality and efficiency of machining processes. By understanding the different types of wheels, their specifications, and safety considerations, you can optimize your grinding operations and achieve superior results. Whether you are involved in manufacturing, repair, or crafting, investing in the right grinding wheel tailored for stainless steel will enhance your productivity and product quality. Remember to consider the specific needs of your project, and don’t hesitate to consult with suppliers for expert recommendations.
Post time:Oct - 06 - 2024