Understanding Grinding Wheels for Tool Steel
Grinding wheels are a crucial component in the manufacturing and maintenance of tool steel, which is known for its hardness, wear resistance, and ability to retain a sharp cutting edge. Tool steel is often used in the production of cutting tools, dies, and molds, and its properties make it a challenging material to process. Therefore, selecting the right grinding wheel is essential for achieving optimal results.
Types of Grinding Wheels
Grinding wheels can be made from various materials, including aluminum oxide, silicon carbide, and ceramic grains. For tool steel, aluminum oxide wheels (specifically those labeled as White Aluminum Oxide or Pink Aluminum Oxide) are commonly used. These grains offer a superior balance of toughness and hardness, allowing for efficient material removal without excessive wear on the wheel itself.
Ceramic grinding wheels are another option praised for their durability and ability to maintain sharp edges. They generate less heat during the grinding process, reducing the risk of thermal damage to the tool steel being worked on. This characteristic is especially significant, as overheating can lead to changes in the microstructure of the tool steel, compromising its properties.
Wheel Characteristics
When selecting a grinding wheel, several characteristics must be considered. The grit size indicates the wheel's coarseness; finer grits (higher numbers) are suitable for achieving smoother finishes, while coarser grits (lower numbers) are more effective for rapid material removal. Generally, a grit size of 60 to 120 is recommended for grinding tool steel, allowing for a good balance between cutting efficiency and surface finish.
grinding wheel for tool steel
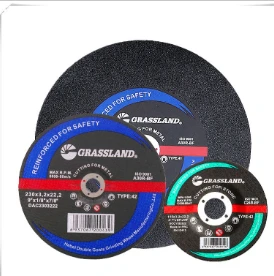
The hardness of the grinding wheel is another critical factor. Grinding wheels are categorized by letters that denote their hardness, ranging from soft (A) to hard (Z). For tool steel, a medium to hard wheel is often preferred. This hardness level allows the wheel to withstand the rigors of grinding tool steel while still providing enough friability to expose fresh cutting edges, enhancing performance.
Bonding Agents
The bonding agent used in the grinding wheel also plays a significant role in its performance. Common types of bonds include vitrified, resin, and rubber. Vitrified bonds are the most prevalent for tool steel grinding due to their ability to handle higher temperatures and provide excellent rigidity. Resin bonds offer more flexibility and are particularly useful when grinding complex shapes or profiles, while rubber bonds are less common and primarily used for specific applications requiring very fine finishes.
Proper Grinding Techniques
To maximize the efficiency of grinding tool steel, operators should employ proper grinding techniques alongside using the right wheel. This includes maintaining a consistent feed rate, ensuring proper coolant application, and keeping the wheel dressed to avoid glaze formation, which can hinder performance. Regularly dressing the wheel not only helps maintain its shape but also ensures that it continues to cut effectively.
Conclusion
In conclusion, the right grinding wheel is paramount when working with tool steel. Understanding the different types of wheels, their characteristics, and proper techniques can significantly enhance the grinding process. By carefully selecting a wheel suited to the specific type of tool steel and its intended use, manufacturers and toolmakers can achieve optimal results, ultimately leading to longer tool life and better performance in a wide range of applications.
Post time:Dec - 17 - 2024