The Grinding Wheel Manufacturing Process
Grinding wheels are essential tools in various industries, serving as abrasive products used for cutting, grinding, and finishing materials. The manufacturing process of grinding wheels is intricate and demands precision at every stage to ensure optimal performance and durability. This article explores the primary steps involved in the grinding wheel manufacturing process, the materials utilized, and the quality control measures that ensure the final product meets industry standards.
Materials Used in Grinding Wheel Manufacturing
The foundation of a grinding wheel begins with the selection of appropriate raw materials. The most common materials used include abrasives, bonding agents, and fillers.
1. Abrasives These are the primary materials that perform the cutting action. Common abrasives include aluminum oxide, silicon carbide, and diamond. Each type of abrasive offers unique properties, making them suitable for specific applications. For instance, aluminum oxide is often used for general-purpose grinding, while diamond abrasives excel in cutting hard materials like ceramics and glass.
2. Bonding Agents The bonding agent holds the abrasive grains together while also adhering them to the wheel’s core. The most frequently used bonding materials include resin, vitrified ceramics, and rubber. Resin bonds are popular due to their flexibility and ability to withstand high temperatures, while vitrified bonds provide superior strength and performance in high-stress applications.
3. Fillers Fillers enhance the performance of the grinding wheel. They help to control the wheel's structure, affecting porosity and durability. Common fillers include calcium carbonate and silica.
The Manufacturing Process
The process of manufacturing grinding wheels consists of several key steps
grinding wheel manufacturing process pdf
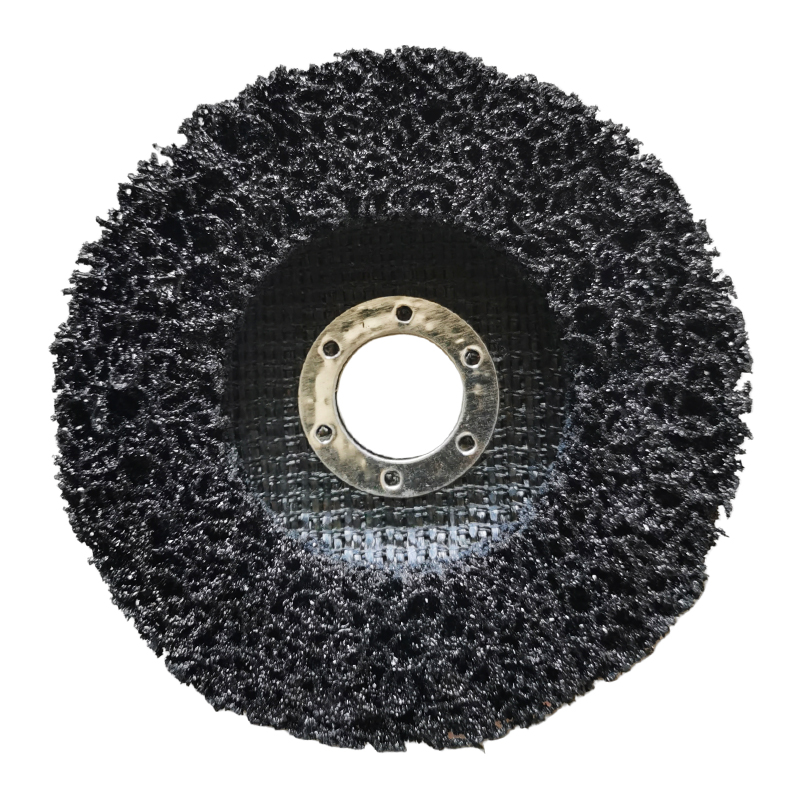
1. Mixing The first step involves blending the abrasives, bonding agents, and fillers in the required proportions. This mixture must be homogeneous to ensure consistent quality across the grinding wheel.
2. Molding After the mixing phase, the blended material is placed into molds to form the desired shape of the grinding wheel. Depending on the type of wheel being produced, the molds may vary in size and design. The molding process is critical, as it determines the wheel's final dimensions and shape.
3. Pressing Once the mixture is in the mold, it undergoes pressing, which applies immense pressure to compact the materials tightly. This step is crucial for ensuring the structural integrity of the grinding wheel. Various pressing methods, such as cold pressing and hot pressing, can be used, depending on the bonding material employed.
4. Drying The pressed wheels are then subjected to a drying process to remove any moisture. This step is particularly important for resin-bonded wheels, as excess moisture can interfere with the curing process.
5. Curing This process varies depending on the bonding material. For resin-bonded wheels, curing typically involves heating the wheel in an oven, which activates the resin and allows it to bond firmly with the abrasive particles. Vitrified wheels usually undergo a kiln firing process, where they are subjected to high temperatures, transforming the binding material into a glass-like structure that solidifies the wheel.
6. Trimming and Grinding After curing, the grinding wheels often require trimming to achieve uniform thickness and ensure that the edges are sharp. This may also involve additional grinding processes to refine the wheel’s surface and improve cutting efficiency.
7. Quality Control Before the wheels are packaged and shipped, rigorous quality control tests are conducted. Measurements for thickness, diameter, and balance are taken to ensure they meet the specifications. Additionally, performance tests may be conducted to evaluate the wheel's cutting efficiency and durability.
Conclusion
The manufacturing process of grinding wheels involves a meticulous combination of material selection, mixing, shaping, and quality control. Each stage is vital to producing a high-performance product that meets the needs of various applications. With advancements in technology and materials science, grinding wheels continue to evolve, improving efficiency and effectiveness in industrial processes. Understanding these processes not only helps manufacturers produce better products but also aids end-users in selecting the right type of wheel for their specific needs.
Post time:Oct - 02 - 2024