Understanding Grinding Wheel Material Composition
In the realm of industrial machining and manufacturing, grinding wheels play a crucial role. These tools, composed of abrasives and bonding materials, are essential for shaping, finishing, and honing various materials. The composition of grinding wheels significantly influences their performance, durability, and suitability for specific applications. This article delves into the materials that constitute grinding wheels, their properties, and their roles in the grinding process.
The Components of Grinding Wheels
The fundamental components of a grinding wheel include the abrasive material, the bonding agent, and the filler materials. Each of these components contributes to the overall effectiveness and efficiency of the wheel.
1. Abrasive Materials
Abrasive materials are the primary component of grinding wheels. They are responsible for cutting and shaping the workpiece. The choice of abrasive directly affects the wheel’s effectiveness, with common materials including
- Aluminum Oxide Known for its versatility, aluminum oxide is suitable for grinding ferrous metals and is found in a variety of forms, including white, pink, and brown options, each tailored for specific applications. - Silicon Carbide This material offers a cutting action that is superior for non-ferrous metals and hard materials like glass and ceramics. Silicon carbide wheels are often green or black, with the former being more commonly used for harder materials.
- Diamond The hardest known abrasive, diamond is typically used for grinding extremely hard materials. Diamond wheels are often used in specialized applications involving ceramics, stone, and composite materials.
- Cubic Boron Nitride (CBN) CBN is another ultra-hard abrasive primarily used for grinding high-speed steels and superalloys. Its thermal stability makes it a suitable choice for high-speed grinding operations.
grinding wheel material composition pdf
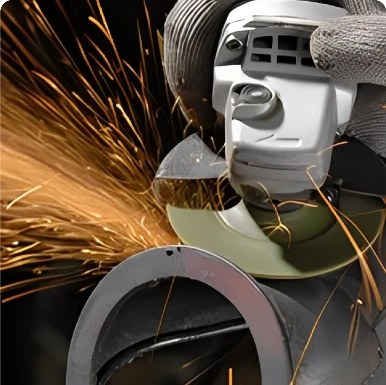
Bonding agents hold the abrasive particles together and provide the structural integrity of the grinding wheel. Various bonding materials are used, each with its unique properties
- Vitrified Bond Made from clay and various materials, vitrified bonds are glass-like and provide excellent rigidity. They are typically used in applications requiring precision and durability.
- Resinoid Bond This synthetic bond provides flexibility and can be formulated to cater to various grinding conditions. Resinoid bonded wheels often produce less heat during grinding, minimizing thermal damage to the workpiece.
- Rubber Bond Known for its ability to conform to the workpiece, rubber bonds are suitable for applications that require a fine finish. These wheels are particularly useful in the grinding of complex shapes.
3. Filler Materials
Filler materials are added to improve the performance characteristics of the grinding wheel. These components can influence the density, porosity, and overall grinding action of the wheel.
Conclusion
The composition of a grinding wheel is a complex interplay of its abrasive materials, bonding agents, and fillers. Understanding these components helps manufacturers select the right grinding wheel for their specific applications. A well-chosen grinding wheel not only improves productivity and efficiency but also enhances the quality of the finished product.
As technology continues to evolve, the development of advanced materials and bonding techniques will likely lead to the creation of more efficient and specialized grinding wheels. This ongoing innovation is essential for meeting the ever-increasing demands of modern manufacturing processes, ensuring that grinding remains an integral part of the industrial landscape.
Post time:Dec - 24 - 2024