Understanding Grinding Wheel Nomenclature
Grinding wheels are essential tools in various manufacturing and industrial processes, designed to shape, sharpen, and finish materials with precision. The efficiency and effectiveness of a grinding wheel can greatly influence the overall performance of machining operations. To ensure that the right wheel is selected for the appropriate task, a clear understanding of grinding wheel nomenclature is crucial. This article provides an overview of the common terminologies associated with grinding wheels and their significance.
Composition of Grinding Wheel Nomenclature
The nomenclature of grinding wheels typically follows a standard set of criteria established by organizations such as the American National Standards Institute (ANSI). This includes several key elements type, size, grit, grade, bond type, and structure. Each of these criteria plays a vital role in defining the wheel's characteristics and applications.
1. Type The type of grinding wheel is often indicated by a letter or a specific code. For instance, a wheel type might include categories such as straight wheels, cup wheels, or segmented wheels. Each type serves distinct purposes; for example, straight wheels are commonly used for surface grinding, while cup wheels are ideal for grinding complex shapes.
2. Size The size of a grinding wheel refers to its diameter and thickness, which are critical factors in determining the wheel’s applicability. Dimensions are typically expressed in inches or millimeters. A wheel's size affects its speed, stability, and how it interacts with the workpiece during the grinding process.
3. Grit Grit size refers to the coarseness or fineness of the abrasive particles on the wheel. Measured using a scale ranging from very coarse (lower grit numbers) to very fine (higher grit numbers), the grit size significantly affects the surface finish of the workpiece. For instance, a wheel with a larger grit size removes material more quickly, but it may not provide as smooth a finish as a finer grit.
grinding wheel nomenclature pdf
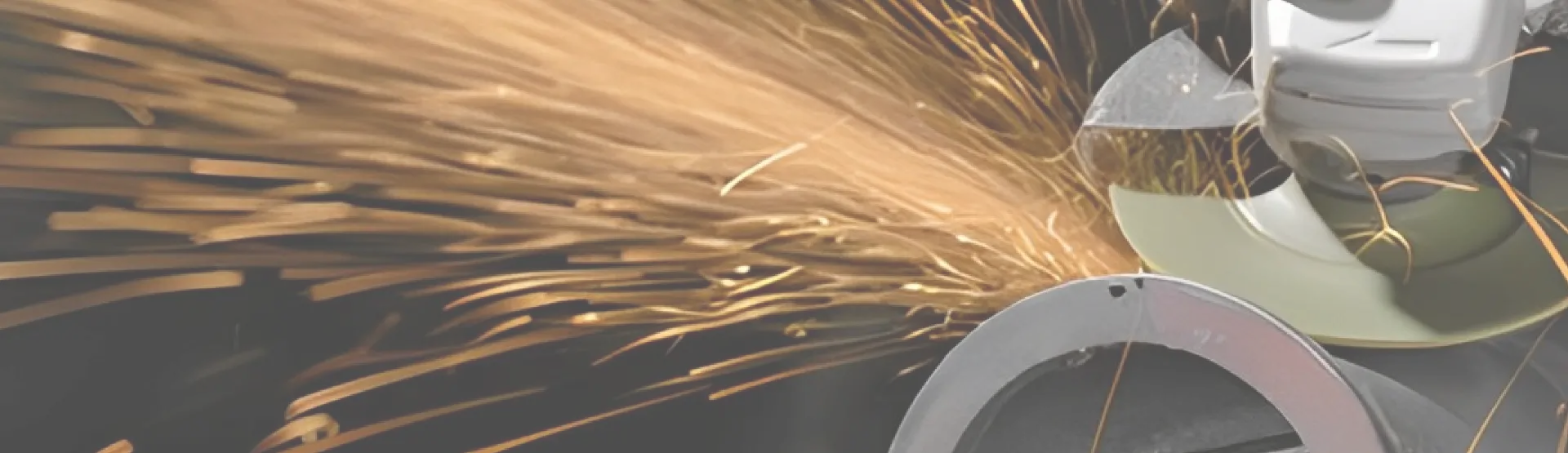
4. Grade The grade of a grinding wheel denotes the strength of the bond holding the abrasive grains together. This is typically classified using letters ranging from A (soft) to Z (hard). A softer grade allows for faster cutting but may wear out more quickly, while a harder grade provides longer life but slower cutting action.
5. Bond Type The bond type indicates the material used to hold the abrasive particles in place. Common bond types include vitrified, resinoid, rubber, and metal bonds. Each bond type has its own characteristics and is suitable for different applications. For example, vitrified bonds are known for their durability and strength, making them suitable for heavy-duty grinding.
6. Structure The structure of the wheel refers to the spacing of the abrasive grains and is denoted by a number. A lower structure number implies a denser wheel, while a higher number indicates a more open wheel. An open structure allows for better chip removal and cooling during the grinding process, which can enhance performance.
Importance of Proper Nomenclature
Understanding grinding wheel nomenclature is pivotal for selecting the right wheel for specific grinding tasks. Using the wrong type of wheel can lead to inefficient machining, poor finishing, and increased tool wear. Additionally, the safety of operators is profoundly influenced by improper wheel selection—using a wheel not suited for the task can lead to dangerous situations, including wheel breakage.
Conclusion
In conclusion, grinding wheel nomenclature is a vital aspect of manufacturing and precision machining. By familiarizing oneself with the components of grinding wheels—type, size, grit, grade, bond type, and structure—users can make informed decisions that lead to enhanced productivity, better-quality finishes, and increased safety in operations. As technology evolves, ongoing education in grinding wheel nomenclature will continue to serve as a foundational skill for professionals in the manufacturing sector.
Post time:Oct - 12 - 2024