Understanding Grinding Wheel Nomenclature
Grinding wheels are essential tools in metalworking, shaping, and finishing operations, helping to achieve precise dimensions and smooth surfaces on various materials. A key to effectively utilizing these tools lies in understanding their nomenclature, which provides vital information about their composition, structure, and intended use. This article will explore the components of grinding wheel nomenclature, aiding operators in selecting the right wheels for their applications.
Composition of Grinding Wheels
Grinding wheels are primarily composed of two components the abrasive material and the bonding agent. The type of abrasive used affects the wheel's cutting performance, durability, and heat resistance. Common abrasives include aluminum oxide, silicon carbide, and diamond, each suited for different types of materials and finishing requirements.
Aluminum oxide wheels, for instance, are versatile and often used for grinding steels and general-purpose applications. Silicon carbide wheels are more effective on non-ferrous metals and brittle materials like ceramics. A diamond wheel, known for its hardness, is ideal for grinding hard materials such as carbide and other high-strength alloys.
The bonding agent holds the abrasive particles together, influencing the wheel's resilience and performance. Bond types include vitrified, resinoid, and rubber, with vitrified bonds offering high strength and thermal resistance, making them suitable for precision grinding. Resinoid bonds are often used for high-speed applications, while rubber bonds provide flexibility and are useful for contouring tasks.
Decoding Grinding Wheel Specifications
When selecting a grinding wheel, one must decipher its specifications, which are usually denoted using a standardized nomenclature. This system classifies wheels based on four primary criteria type, dimensions, abrasive grain size, and hardness.
1. Type – The type of grinding wheel indicates its shape and design. Common types include straight wheels, depressed center wheels, and cup wheels, each tailored for specific applications.
grinding wheel nomenclature pdf
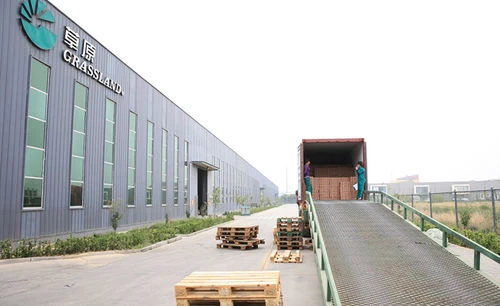
2. Dimensions – Wheel dimensions are listed as diameter and thickness, typically expressed in inches or millimeters. For example, a wheel labeled “6 x 1 x 1” indicates a diameter of 6 inches, a thickness of 1 inch, and a hole size of 1 inch.
3. Abrasive Grain Size – Grain size affects the surface finish and material removal rate. It is indicated by a number which correlates to the coarseness or fineness of the wheel—lower numbers denote coarser grains, suitable for faster material removal, while higher numbers correspond to finer grains for smoother finishes.
4. Hardness – The hardness rating of the wheel determines how much pressure is needed to grind effectively. Hardness is usually represented by letters, where less hard (soft) wheels allow for greater wear and are suitable for grinding harder materials, while harder wheels maintain their form longer.
Application-Specific Considerations
Choosing the right grinding wheel is crucial for optimizing performance and achieving desired results in specific applications. Factors such as the material being ground, the machining operation, and the desired finish must all be considered.
For instance, when grinding stainless steel, a wheel with a finer grit size (e.g., 120) can provide a smooth finish and reduce the risk of heat buildup, which might otherwise tarnish the surface. Conversely, for roughing operations on cast iron, a coarse wheel (e.g., 46 grit) would be more effective.
Conclusion
Understanding the nomenclature of grinding wheels significantly enhances one’s ability to select the appropriate wheel for a specific grinding application. By considering the composition, specifications, and intended use of the grinding wheel, operators can improve efficiency, output quality, and tool longevity. As advances in abrasive technology continue to evolve, staying informed about wheel nomenclature will be key to making the most of these indispensable tools in modern manufacturing and metalworking processes. Whether one is a seasoned operator or a newcomer to the field, a solid grasp of grinding wheel nomenclature lays the groundwork for effective and precise machining.
Post time:Dec - 11 - 2024