Understanding Grinding Wheel Nomenclature
Grinding wheels are essential tools in the field of machining and metalworking. They are employed for various grinding processes, including sharpening, shaping, and finishing materials. To effectively utilize grinding wheels, it is crucial to understand their nomenclature—essentially, a standardized system of terminology that describes the characteristics of grinding wheels. This article will delve into the components of grinding wheel nomenclature, helping users select the appropriate wheel for their specific applications.
Components of Grinding Wheel Nomenclature
The nomenclature of grinding wheels is typically comprised of a series of letters and numbers that convey essential information about the wheel's specifications. The classification system for grinding wheels is standardized by organizations like the American National Standards Institute (ANSI) and the International Organization for Standardization (ISO).
1. Type of Material The first part of the nomenclature often indicates the type of abrasive material used in the wheel. Common abrasives include aluminum oxide (A), silicon carbide (C), and ceramic alumina (CA). Each type of abrasive has properties that make it suitable for specific applications and materials.
2. Grain Size Following the type of material is the grain size, represented by a number. The grain size affects the smoothness of the finish produced by the grinding wheel. Coarser grains (lower numbers) are better for aggressive material removal, while finer grains (higher numbers) provide a smoother finish.
3. Structure The structure of a grinding wheel refers to the spacing between the abrasive grains. It is denoted by another number, which can range from open (indicating a loose structure) to dense (indicating tight packing of the grains). A more open structure is useful for cooling and preventing the wheel from clogging during use.
grinding wheel nomenclature pdf
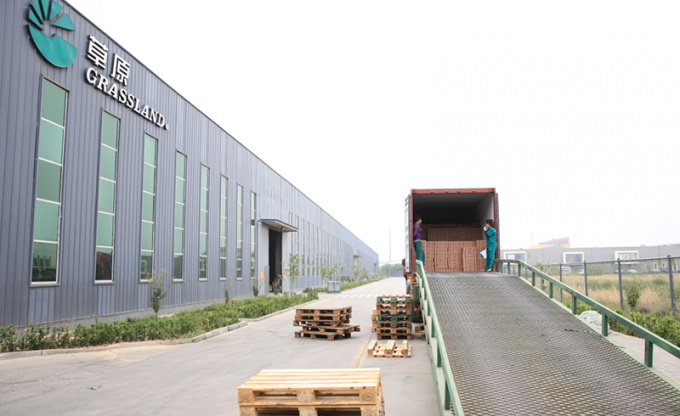
4. Bond Type The bond type is crucial for holding the abrasive grains together. Various bond materials, including vitrified (V), resinoid (R), rubber (B), and metal (M), are specified in the nomenclature. Each bond type affects the wheel's durability, flexibility, and operational temperature limits. For instance, vitrified wheels are known for their strength and resistance to wear at high temperatures.
5. Wheel Diameter and Thickness The diameter and thickness of the wheel are often indicated at the end of the nomenclature. These dimensions are critical for ensuring compatibility with grinding machines and achieving optimal grinding performance. The proper diameter and thickness can enhance cutting efficiency and increase the lifespan of the wheel.
Practical Applications of Nomenclature
Understanding grinding wheel nomenclature is indispensable for machinists and operators. It enables them to choose the correct wheel tailored to specific tasks, such as surface grinding, cylindrical grinding, or tool sharpening. For example, when dealing with harder materials, one might opt for a wheel with a low grain size and a robust bond to withstand the high forces involved.
In addition, correct interpretation of nomenclature plays a vital role in safety. Using the wrong wheel type for a machine or application can lead to wheel failure, which poses hazards to the operator and the machinery. By adhering to the specifications outlined in the nomenclature, operators can mitigate risks and enhance productivity.
Conclusion
In conclusion, the nomenclature of grinding wheels serves as a crucial framework for understanding the various characteristics of these essential tools. By breaking down the elements—abrasive material, grain size, structure, bond type, and dimensions—users can make informed decisions when selecting grinding wheels for their applications. Mastery of grinding wheel nomenclature not only enhances operational efficiency but also promotes safety and effectiveness in machining processes. As industries evolve and demand precision and quality, the importance of understanding grinding wheel nomenclature will continue to grow.
Post time:Sep - 29 - 2024