Understanding Grinding Wheel Selection A Comprehensive Guide
Grinding wheels are an essential tool in metalworking and other industries, providing a means to shape, sharpen, and finish materials. Selecting the right grinding wheel is crucial for achieving the desired results and optimizing performance. This article will explore the factors involved in grinding wheel selection, drawing on insights from the grinding wheel selection chart.
1. Wheel Composition
One of the first considerations in selecting a grinding wheel is its composition. Grinding wheels are typically made from abrasive materials such as aluminum oxide, silicon carbide, and ceramic. Each of these materials has unique properties that make them suitable for specific tasks.
- Aluminum Oxide This is the most common type of abrasive used in grinding wheels due to its versatility and durability. It is ideal for grinding ferrous metals and is particularly effective in applications where high material removal rates are required.
- Silicon Carbide This material is harder than aluminum oxide and works well on non-ferrous metals, ceramics, and some plastics. Silicon carbide wheels can produce a finer finish, making them suitable for applications where precision is essential.
- Ceramic Abrasives Known for their high-performance characteristics, ceramic wheels provide superior cut rates and longer life. They are ideal for heavy-duty applications and are commonly used in industries that require aggressive grinding.
2. Grit Size
The grit size of a grinding wheel significantly influences the finish and removal rate. The grit is measured in numbers; the higher the number, the finer the grit.
- Coarse Grit (less than 40) These wheels are ideal for high material removal applications where a rough finish is acceptable. They are frequently used in applications such as grinding welds or shaping rough surfaces.
- Medium Grit (40 to 80) Medium grit wheels offer a balance between material removal and surface finish. They are suitable for general-purpose grinding tasks.
- Fine Grit (100 and above) Fine grit wheels are used for finishing and polishing applications. They are effective in achieving smooth surfaces and precise dimensions.
3. Wheel Hardness
grinding wheel selection chart
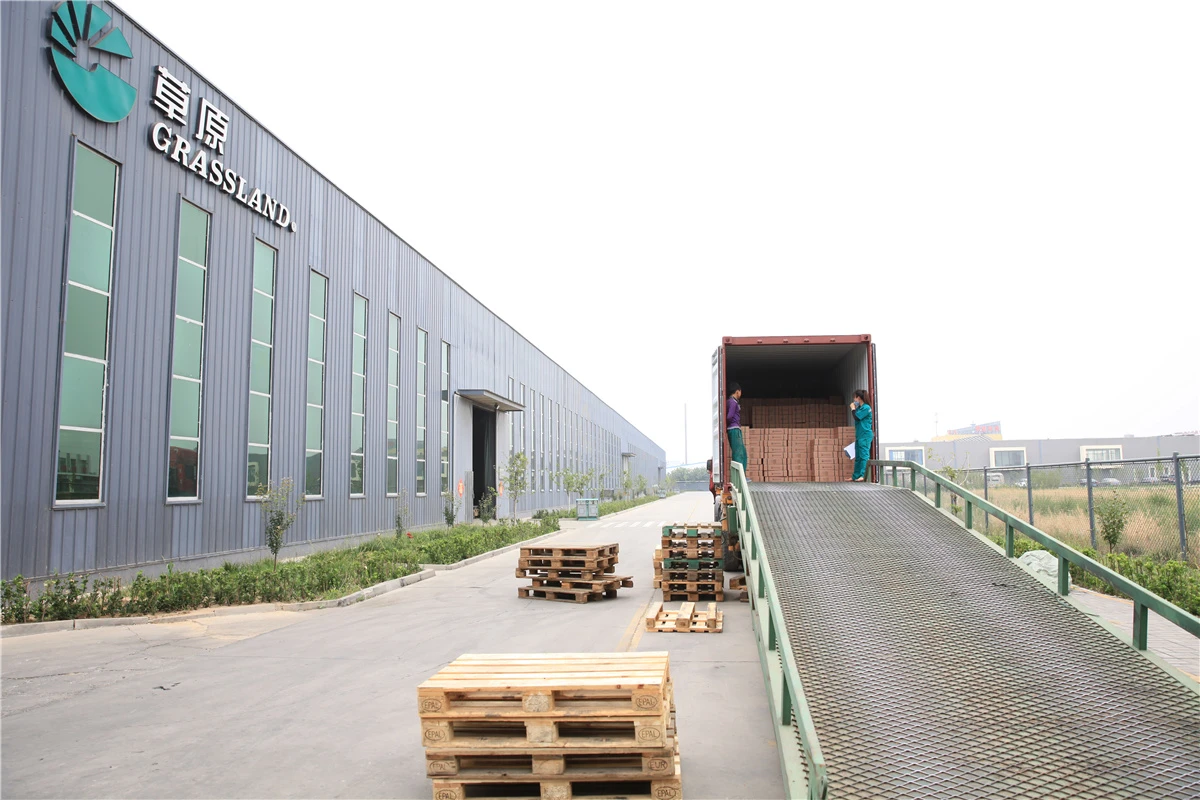
The hardness of a grinding wheel determines how much pressure is required to grind the material effectively
. The hardness scale ranges from A (soft) to Z (hard).- Soft Wheels These wheels are ideal for grinding softer materials or for applications where coolant is used. They tend to wear down quickly, which enables them to expose new abrasive grains frequently.
- Hard Wheels Suitable for harder materials, these wheels provide a longer life and are less aggressive in cutting. However, they may require more pressure to achieve the desired results.
4. Bond Type
The bond is the material that holds the abrasive grains together. Common bond types include vitrified, resin, rubber, and metal.
- Vitrified Bonds These are made from a mixture of clays and are commonly used for high-speed applications due to their rigidity and thermal stability.
- Resin Bonds These provide flexibility and are often used for applications that require a finer finish.
- Rubber and Metal Bonds Typically used in specialized applications, these bonds provide unique properties that can enhance grinding performance for specific materials.
5. Application and Equipment Compatibility
Finally, understanding the specific application and the equipment being used is vital in grinding wheel selection. Different machines have unique speed requirements and operational parameters, which can influence the choice of wheel.
Conclusion
Selecting the right grinding wheel involves understanding various factors, including wheel composition, grit size, hardness, bond type, and application requirements. Consulting a grinding wheel selection chart can aid in making an informed choice, ultimately enhancing productivity and achieving optimal results in grinding processes. By taking the time to evaluate these critical factors, operators can ensure that they use the most effective grinding wheels for their specific needs, leading to improved performance and cost-efficiency in their operations. Whether for industrial applications or DIY projects, the right grinding wheel is an invaluable asset in achieving precision and quality in workpieces.
Post time:Dec - 06 - 2024