Selecting the Right Grinding Wheels for Your Needs
Grinding wheels are essential tools in machining and manufacturing processes, offering precision, efficiency, and versatility. These tools are widely used for grinding, cutting, and polishing materials, and selecting the right grinding wheel is crucial for achieving optimal results. The choice of a grinding wheel depends on various factors including the material being processed, the desired finish, and the machine’s specifications. This article aims to provide a comprehensive guide to the selection of grinding wheels.
Understanding Grinding Wheel Composition
Before selecting a grinding wheel, it’s important to understand its composition. Grinding wheels typically consist of an abrasive compound, a bond that holds the abrasive particles together, and other additives that enhance performance. The most common abrasive materials include aluminum oxide, silicon carbide, diamond, and cubic boron nitride (CBN). Each of these materials has distinct properties suitable for different applications
1. Aluminum Oxide This is the most common abrasive and is ideal for general-purpose grinding of ferrous metals. It is durable and efficient, making it suitable for various applications.
2. Silicon Carbide Best for non-ferrous metals and hard materials like ceramics and glass, silicon carbide is known for its sharpness and ability to retain cutting edges.
3. Diamond The hardest known material, diamond grinding wheels are perfect for grinding extremely hard materials, including carbides, ceramics, and glass.
Choosing the Right Bond Type
grinding wheels selection
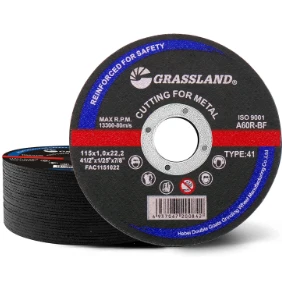
The bond in a grinding wheel affects its performance and how it wears during use. Common bond types include vitrified, resin, metal, and rubber. Vitrified bonds are the most widely used and are known for their strength and thermal stability. Resin bonds offer flexibility and are great for precision grinding applications. Metal bonds are suitable for heavy-duty grinding and high wear resistance, while rubber bonds provide shock absorption for delicate work.
Consider the Wheel Specification
Grinding wheels are categorized by specific metrics such as grit size, hardness, structure, and shape. The grit size indicates the size of abrasive particles in the wheel. A finer grit size results in a smoother finish, while a coarser grit is better for material removal. Wheel hardness affects its resistance to wear; harder wheels are typically used for softer materials, while softer wheels are better for harder materials.
The structure of a wheel refers to the spacing of the abrasive grains and their arrangement; an open structure allows for better chip removal, while a dense structure offers a smoother finish. Additionally, the shape of the wheel should be chosen based on the application. Various shapes like flat, cylindrical, or cup wheels are tailored for specific grinding tasks.
Application and Environment Considerations
Finally, consider the application environment when selecting a grinding wheel. Factors such as the type of grinder, speed, coolant usage, and the physicochemical properties of the material to be ground all play vital roles in the effectiveness of the grinding process. For instance, high-speed operations may require wheels designed for thermal stability to prevent damage.
Conclusion
In conclusion, selecting the right grinding wheel is a complex but essential task that can greatly influence the quality of workpieces and the efficiency of machining processes. By understanding the types of abrasives, bond types, wheel specifications, and application environments, users can make informed decisions that enhance productivity and product quality. Investing time in the proper selection of grinding wheels will ultimately lead to improved performance, reduced costs, and better overall results in manufacturing operations.
Post time:Dec - 11 - 2024