Grinding Wheels Selection A Comprehensive Guide
Selecting the right grinding wheel is crucial for achieving optimal performance in your grinding operations. Whether you're working in metal fabrication, woodworking, or any other industry that requires precise material removal, understanding the types of grinding wheels available and their specific applications can significantly enhance your productivity and the quality of your work. This article will provide an overview of the factors to consider when selecting grinding wheels, types of wheels, and best practices for their usage.
Understanding Grinding Wheels
Grinding wheels consist of abrasive particles bonded together, usually in a circular shape. These wheels are used for various grinding tasks, such as sharpening, shaping, or finishing materials. The selection of a grinding wheel depends on several factors, including the material being processed, the desired finish, and the type of grinding operation.
Factors to Consider
1. Material Type The material you intend to grind plays a significant role in wheel selection. For instance, harder materials like tool steel require wheels with a harder bond and finer grit. On the other hand, softer materials like aluminum can be effectively ground with softer bonds and coarser grits.
2. Grit Size The grit size of the wheel affects the finish of the workpiece. Coarse grits (roughly 24-60) are suitable for material removal and shaping, while finer grits (around 80-120 and above) are ideal for finishing and polishing. Selecting the right grit size is essential for achieving the desired surface quality.
3. Bond Type The bond material determines how the abrasive particles are held together and affects the wheel's performance. Common types of bonds include vitrified, resin, rubber, and metal. Vitrified bonds are particularly popular for their strength and thermal resistance, making them suitable for high-speed applications.
4. Wheel Structure The wheel's structure refers to the arrangement and spacing of the abrasive grains. A denser wheel with a higher number of grains offers more aggressive grinding action, while a less dense wheel allows for cooler grinding, which is essential for preventing damage to both the workpiece and the wheel itself.
5. Grind Type and Operation Different grinding operations, such as surface grinding, cylindrical grinding, and tool grinding, may require different types of wheels. For example, surface grinding may benefit from wheels designed for flat surfaces, while cylindrical grinding might use wheels suitable for creating a cylindrical finish.
Common Types of Grinding Wheels
1. Alumina Wheels These are versatile wheels made from aluminum oxide and suitable for a variety of metals, including steel and cast iron. They are commonly used in general-purpose grinding.
grinding wheels selection
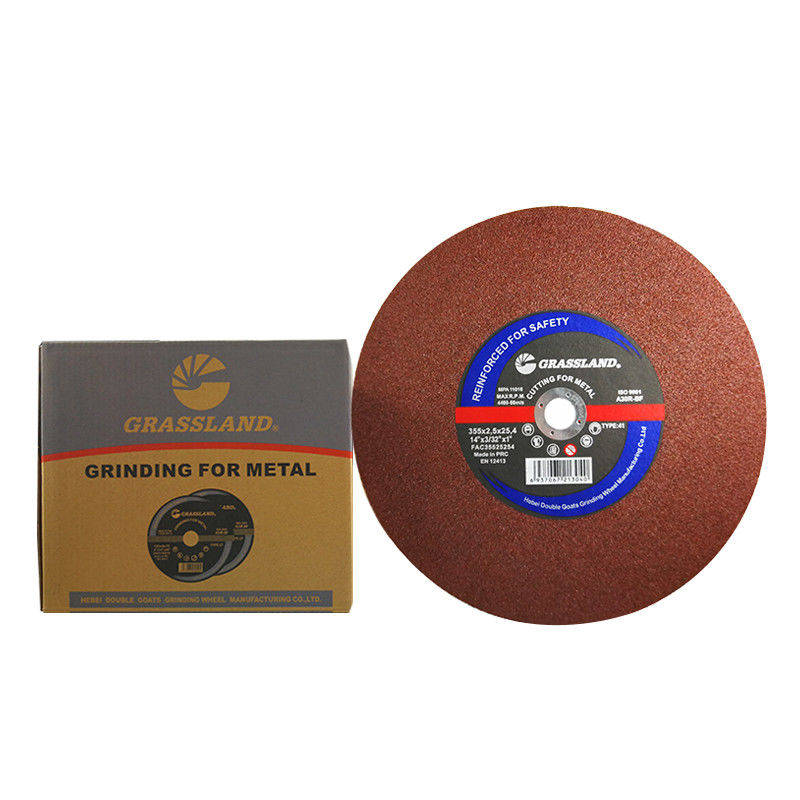
2. Silicon Carbide Wheels These wheels are excellent for grinding non-ferrous metals, ceramics, and glass. Their unique structure allows for effective material removal in harder and more brittle materials.
3. Diamond Wheels Designed for extremely hard materials such as carbide and ceramics, diamond wheels provide exceptional grinding performance and a long lifespan.
4. Cubic Boron Nitride (CBN) Wheels Often used for grinding high-speed steel and hard materials, CBN wheels offer sharp cutting edges and maintain their shape well under high temperatures.
Best Practices for Usage
To maximize the performance and lifespan of your grinding wheels, consider implementing the following best practices
- Proper Mounting Ensure that the wheel is mounted correctly on the grinder, maintaining alignment and balance to minimize vibration during operation.
- Use of Coolants Employing coolants can help reduce heat during grinding, preventing wheel wear and workpiece damage.
- Regular Inspection Frequently inspect grinding wheels for any signs of wear or damage. Replace wheels that show chipping, cracking, or excessive wear to ensure safety and performance.
- Training Operators Ensure that all operators are adequately trained in grinding wheel selection and operation. This knowledge helps in choosing the right tools and promoting efficiency and safety.
Conclusion
Selecting the appropriate grinding wheel is vital for efficiency, safety, and quality in grinding operations. By understanding the factors influencing wheel selection and familiarizing yourself with the different types of grinding wheels available, you can choose the right wheel for your specific application. Implementing best practices will not only enhance your grinding process but also prolong the life of your equipment, resulting in a more productive and cost-effective operation.
Post time:Nov - 15 - 2024