How to Use Flap Discs A Comprehensive Guide
Flap discs are versatile and efficient tools commonly used in metalworking, woodworking, and other industries that require surface finishing and polishing. These discs consist of multiple layers of abrasive material bonded together, creating a flap-like structure that conforms to the surface being worked on. Not only do they provide a smooth finish, but they also have the capability to grind and blend surfaces. In this article, we’ll guide you through the essentials of using flap discs effectively and safely.
Understanding Flap Discs
Flap discs are available in various sizes, grits, and materials, each tailored for specific applications. The grit size indicates the coarseness of the abrasive material, with lower numbers (e.g., 40 or 60) being more aggressive for heavy grinding and higher numbers (e.g., 80 or 120) suitable for finer finishing. Common materials for flap discs include aluminum oxide, zirconia alumina, and ceramic, each providing different cutting qualities and longevity.
Choosing the Right Flap Disc
When selecting a flap disc, consider the material you will be working on. For instance, zirconia alumina is ideal for metal applications due to its durability and heat resistance, while aluminum oxide is excellent for wood and softer materials. The angle of the flap disc (usually 0 to 15 degrees) should also match the application's requirements. A flatter disc is better suited for finishing tasks, while a more angled disc can handle more aggressive grinding.
Safety Precautions
Before you begin using a flap disc, it's important to prioritize safety. Always wear appropriate personal protective equipment (PPE) such as safety goggles, gloves, and a dust mask to protect yourself from flying debris and dust. Ensure that your work area is clean and well-lit. Double-check that the flap disc is compatible with your grinder, and inspect it for any defects or wear before use.
Preparing the Tool and Workpiece
how to use flap disc
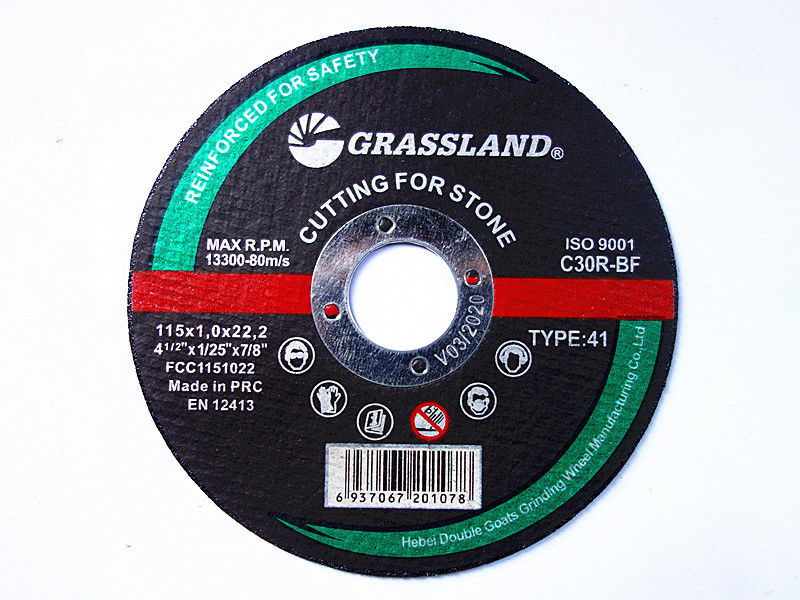
To use a flap disc effectively, mount it securely onto an angle grinder. Make sure to follow the manufacturer’s instructions for installation. Once the disc is in place, adjust the tool's speed based on the material you are working with. For harder materials, a slower speed is often more effective, preventing overheating and extending the life of the disc.
Before starting, it is advisable to clean the workpiece of any rust, paint, or debris to ensure optimal adhesion and effectiveness of the flap disc. Secure the workpiece if necessary to prevent movement during grinding.
Operating the Flap Disc
When you begin working with the flap disc, position the grinder at a comfortable angle to the surface, typically between 15 and 30 degrees. This angle allows for more efficient material removal while minimizing the risk of gouging or damaging the surface. Use smooth, even strokes to ensure a consistent finish. It's important not to apply excessive pressure, as this can lead to uneven wear of the disc and potentially damage the workpiece.
For best results, move the grinder in a circular or sweeping motion across the surface, allowing the flap disc to do the work. If you are blending or finishing a surface, try to maintain a consistent speed and pressure for an even appearance. Take breaks periodically to check your progress and the condition of the flap disc.
Finishing Up
Once you have achieved the desired surface finish, turn off the grinder and allow the disc to come to a complete stop before setting it down. Clean the workpiece to remove any dust or debris generated during the process. Inspect the flap disc for wear and replace it as needed.
In conclusion, flap discs are powerful tools that can enhance your finishing and grinding projects when used correctly. By choosing the right disc, prioritizing safety, and employing proper techniques, you can achieve excellent results and prolong the life of your tools. Whether you are a professional or a DIY enthusiast, mastering the use of flap discs will undoubtedly improve the quality of your work.
Post time:Dec - 05 - 2024