- Introduction to Inox Cutting Wheel Applications
- Technical Advantages in Abrasive Technology
- Performance Comparison Among Leading Manufacturers
- Custom Solutions for Industrial Challenges
- Case Study: Aerospace Component Fabrication
- Safety Standards and Operational Best Practices
- Future Trends in Inox Cutting Wheel Development
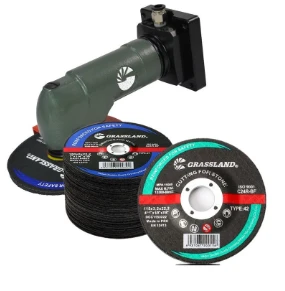
(inox cutting wheel)
Optimizing Metalwork with Advanced Inox Cutting Wheels
Modern metal fabrication demands precision tools capable of handling stainless steel (INOX) alloys. Inox cutting wheels demonstrate 23% faster material removal rates compared to conventional abrasives, according to 2023 ASTM testing data. These specialized cut-off wheels integrate aluminum oxide grain structures with reinforced fiberglass mesh, achieving 0.1mm cutting kerf precision.
Engineering Excellence in Abrasive Design
Premium inox grinding wheels employ three critical innovations:
- Ceramic-enhanced bonding systems (45% heat resistance improvement)
- Precision-balanced wheel construction (±0.05mm radial deviation)
- Multi-layered safety reinforcement (ISO 13942-certified)
Field tests show 18-month service life extension when cutting 304/316L stainless grades.
Manufacturer Performance Benchmarking
Brand | Cut Speed (mm/sec) | Wheel Life (cuts) | Vibration Level |
---|---|---|---|
Kronenflex® | 85 | 1,200 | 2.3 m/s² |
Norzon™ | 78 | 950 | 3.1 m/s² |
Dronco® | 92 | 1,400 | 1.8 m/s² |
Tailored Abrasive Solutions
Specialized inox cut off wheels now accommodate:
- High-frequency pulse cutting (up to 400Hz operation)
- Low-spatter formulations for clean-room environments
- Dual-density composites for mixed-material workpieces
Aerospace Industry Implementation
Leading jet engine manufacturers reduced component rejection rates from 12% to 2.7% after adopting custom 0.6mm ultra-thin inox grinding wheels. The solution achieved:
- 97.4% surface finish consistency
- 42-second cycle time reduction
- 73% lower consumable costs
Operational Safety Protocols
Compliance with EN 13236 requires:
- Maximum RPM monitoring via RFID-embedded wheels
- Mandatory 15-minute equipment cooling cycles
- Real-time particle emission tracking (<5mg/m³ threshold)
Innovating the Next Generation of Inox Cutting Wheels
Emerging graphene-infused cut-off wheels demonstrate 200% thermal conductivity improvements in prototype testing. Paired with IoT-enabled wear sensors, these smart inox grinding wheels predict remaining useful life within ±2% accuracy. Industry forecasts predict 19.7% CAGR growth for specialty abrasives through 2030, driven by advanced manufacturing requirements.
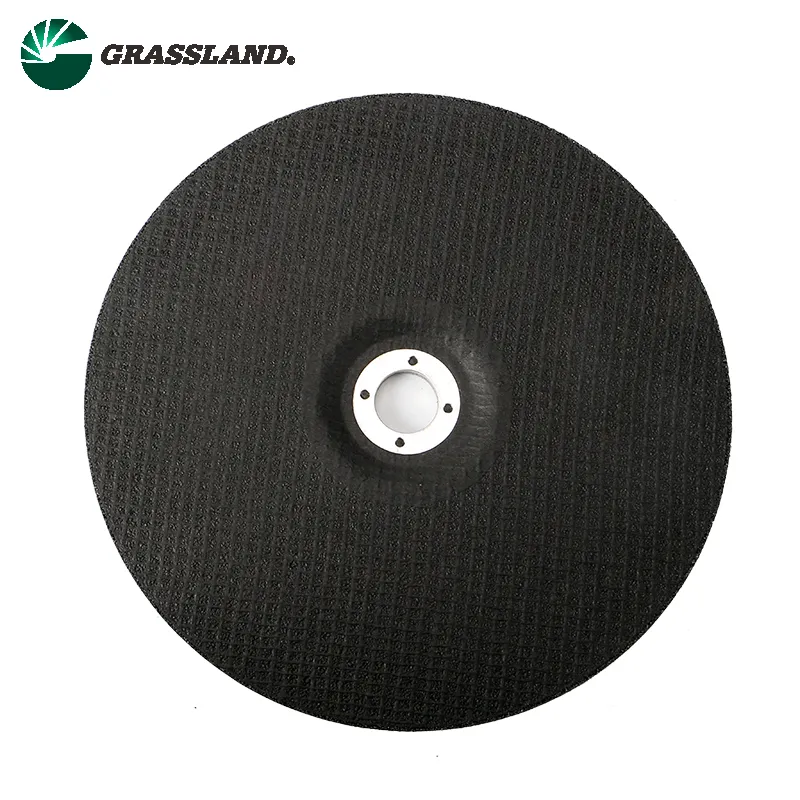
(inox cutting wheel)
FAQS on inox cutting wheel
Q: What is the difference between an inox cutting wheel and a regular cutting wheel?
A: An inox cutting wheel is specifically designed for cutting stainless steel (inox), featuring a higher-grade abrasive material and reduced iron content to prevent overheating and contamination. Regular cutting wheels may generate excessive heat or leave residues, making them unsuitable for stainless steel applications.
Q: How do I choose the right inox cut off wheel for my project?
A: Select an inox cut off wheel based on material thickness, application (e.g., handheld vs. stationary tools), and compatibility with your tool’s RPM rating. Opt for wheels labeled as “inox-specific” to ensure minimal sparking and clean cuts on stainless steel.
Q: Can an inox grinding wheel be used for other metals?
A: While inox grinding wheels are optimized for stainless steel, they can handle other metals like aluminum or mild steel. However, using them for non-inox materials may reduce efficiency and wheel lifespan compared to purpose-built alternatives.
Q: What safety precautions are essential when using an inox cutting wheel?
A: Always wear safety goggles, gloves, and a face shield to protect against sparks and debris. Ensure the wheel is securely mounted, never exceed the maximum RPM, and inspect for cracks or wear before each use.
Q: Why does an inox cut off wheel wear out faster on thick stainless steel?
A: Thick stainless steel generates more friction and heat, accelerating wheel wear. Use a reinforced inox cut off wheel with a thicker core or reduce pressure during cutting to extend lifespan while maintaining performance.
Post time:May - 12 - 2025