The Use of Masonry Cut-Off Wheels on Metal An Overview
When it comes to metalworking, precision and efficiency are two paramount factors that manufacturers and craftsmen alike strive to achieve. Among various tools and accessories available, masonry cut-off wheels have gained popularity in applications involving metal. While these wheels are primarily designed for cutting through masonry, they can also be effectively used on metal under specific conditions. This article explores the unique characteristics of masonry cut-off wheels, their advantages, limitations, and best practices for usage on metal.
Understanding Masonry Cut-Off Wheels
Masonry cut-off wheels, often made of abrasive materials such as corundum or silicon carbide, are designed to slice through hard materials like brick, concrete, and stone. Their coarse grain structure allows them to generate enough force to break through tough surfaces with minimal risk of blunting. However, this same feature can also be advantageous when used on softer metals, particularly ferrous and non-ferrous materials.
Advantages of Using Masonry Cut-Off Wheels on Metal
1. Cost-Effectiveness Masonry cut-off wheels tend to be more affordable than specialized metal cut-off wheels. For hobbyists or small workshops that encounter occasional metal-cutting tasks, these wheels can be a budget-friendly alternative.
2. Durability The abrasive composition of masonry wheels gives them durability when cutting hard materials. This means that they can handle tougher jobs, providing longevity on heavy-duty tasks.
3. Versatility The ability to cut through both masonry and metal makes these wheels versatile tools for professionals who deal with a variety of materials in their work. This characteristic can be particularly advantageous in renovation projects where different materials coexist.
4. Availability Masonry cut-off wheels are widely available and can be found in most hardware stores. This accessibility is crucial for quick projects where specialized tools may not be readily obtainable.
Limitations to Consider
masonry cut off wheel on metal
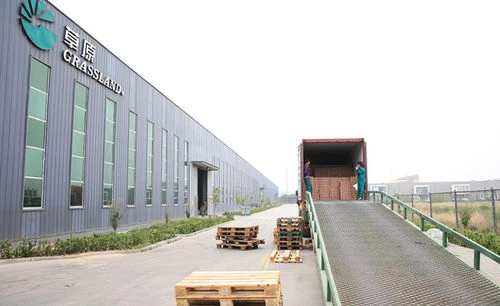
While masonry cut-off wheels can cut through metal, they are not without limitations.
1. Heat Generation One significant drawback is the amount of heat generated during cutting. The abrasive material can cause overheating, which can warp the metal or change its properties. It’s essential to manage the cutting process carefully, possibly by using water or oil to cool the metal.
2. Cutting Speed Masonry cut-off wheels usually operate at slower cutting speeds compared to metal-specific wheels. This can result in longer cutting times, which may not be ideal for high-volume projects.
3. Finish Quality The finish left behind by masonry wheels may not be as smooth as that achieved by metal cut-off wheels. Depending on the project requirements, additional finishing processes may be necessary.
4. Limited Material Compatibility While they can handle some softer metals, masonry cut-off wheels are not suitable for all types of metal, particularly harder varieties such as stainless steel or alloys.
Best Practices for Using Masonry Cut-Off Wheels on Metal
To make the most of masonry cut-off wheels when working with metal, consider the following guidelines
- Speed and Pressure Control Use the wheels at lower speeds and apply gentle pressure to avoid overheating and damaging your material. - Cooling Techniques Employ cooling methods, such as water or air cooling, to dissipate heat during cutting. - Protective Equipment Always use appropriate protective gear, including goggles and gloves, to shield yourself from sparks and debris. - Testing Before starting on your main project, conduct a test cut on scrap metal to gauge performance and adjust techniques accordingly.
Conclusion
Masonry cut-off wheels offer a unique alternative for metal cutting tasks, especially in cost-sensitive and versatile work environments. Understanding the advantages and limitations, along with implementing best practices, can significantly enhance their effectiveness when working with metal. As always, balancing precision and safety should remain a priority in all metalworking projects.
Post time:Dec - 05 - 2024