Understanding Masonry Flap Discs A Comprehensive Guide
Masonry flap discs are specialized tools indispensable for professionals and DIY enthusiasts involved in masonry work. They are designed for grinding, blending, and finishing surfaces made of brick, concrete, stone, and other masonry materials. This article aims to explore what masonry flap discs are, their components, applications, benefits, and tips for choosing the right one.
What Are Masonry Flap Discs?
Masonry flap discs consist of overlapping layers, or flaps, of abrasive material attached to a central backing plate. These flaps are usually made from high-quality abrasive materials such as zirconia alumina or ceramic, specifically engineered for heavy-duty grinding. The unique structure of flap discs differentiates them from traditional grinding wheels and makes them a preferred choice for various applications in masonry work.
Components of Masonry Flap Discs
The main components of masonry flap discs include
1. Abrasive Flaps These are the primary working parts of the disc. They are made from different abrasives to cater to various surfaces and finishes.
2. Backing Plate This is the sturdy foundation that supports the flaps. It can be made from fiberglass or resin and is designed to withstand high rotational speeds.
3. Attachment Method Most masonry flap discs come with a threaded, quick-change attachment, allowing for easy installation on power tools.
Applications of Masonry Flap Discs
Masonry flap discs are versatile and can be used for various tasks, including
- Grinding Effective for removing material quickly from hard surfaces, such as concrete and stone. - Finishing Provides a smooth surface finish, which is vital for aesthetic applications, ensuring that the masonry looks clean and professional. - Deburring Efficient for removing the sharp edges of cut masonry, which is crucial for safety and aesthetics. - Surface Preparation Ideal for preparing surfaces before painting or sealing, as they provide a uniform texture.
Benefits of Using Masonry Flap Discs
The use of masonry flap discs comes with numerous advantages
masonry flap disc
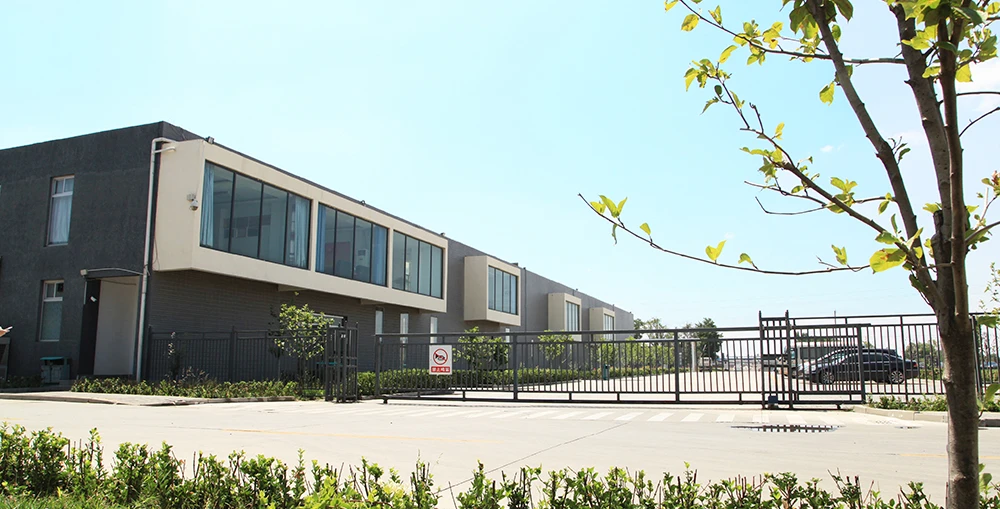
1. Efficiency Flap discs can remove material faster than traditional grinding wheels, which can help in completing tasks more quickly.
2. Versatility They can be used in various applications, from heavy grinding to delicate finishing, making them suitable for multiple jobs on the worksite.
3. Improved Control The design of flap discs allows for better control over the grinding process, reducing the likelihood of gouging or damaging the surface.
4. Dust Reduction Many masonry flap discs are designed to minimize dust generation, contributing to a cleaner workspace and improved visibility during work.
5. Longer Lifespan Due to the design and quality of materials used, masonry flap discs typically last longer than conventional grinding wheels, providing better value for money.
Choosing the Right Masonry Flap Disc
When selecting a masonry flap disc, consider the following factors
1. Abrasive Material Choose a disc made from the right abrasive material suited for your specific task. Zirconia alumina is excellent for heavy grinding, while ceramic is ideal for high-performance applications.
2. Grit Size The grit size determines the coarseness of the disc. Finer grits (higher numbers) are suitable for finishing, while coarser grits (lower numbers) are used for heavy grinding.
3. Disc Diameter Ensure the size of the flap disc is compatible with your power tool. Common sizes range from 4.5 to 7 inches.
4. Backing Plate Type Depending on the job, opt for a durable backing plate that can withstand the necessary pressure and speed.
Conclusion
Masonry flap discs are essential tools for anyone working with masonry materials. Their efficiency, versatility, and ease of use make them a popular choice among professionals and hobbyists alike. By understanding their components, applications, and benefits, users can leverage masonry flap discs for optimal performance in their projects. Always ensure to choose the right disc for the job to maximize productivity and achieve the best results.
Post time:Dec - 21 - 2024