Understanding Masonry Flap Discs A Comprehensive Guide
Masonry flap discs are essential tools in the realm of construction and masonry work, specifically designed to provide effective grinding, blending, and finishing of various materials. Unlike traditional grinding wheels, flap discs are constructed from layers of abrasive material (usually aluminum oxide or zirconia) attached to a central disc. This unique design allows for flexibility and greater surface contact, making masonry flap discs ideal for working on uneven surfaces such as brick, concrete, stone, and even certain types of metals.
The Anatomy of a Masonry Flap Disc
A masonry flap disc consists of several key components. The first is the backing plate, often made from fiberglass or metal, which provides structural integrity. Attached to this plate are overlapping flaps of abrasive material that wear down as they are used, continually exposing fresh material. Flap discs come in various sizes, typically ranging from 4 to 7 inches in diameter, and can be used on both handheld grinders and mounted grinders.
The grit size of the abrasive material also varies, allowing users to choose a disc that meets their specific needs. Coarse grits (36-60) are excellent for aggressive material removal and heavy grinding, while finer grits (80-120) are better suited for polishing and finishing surfaces. Understanding the properties of these discs can greatly enhance the quality of work and efficiency on the job site.
Applications in Masonry and Beyond
Masonry flap discs are particularly versatile. In masonry applications, they are used for grinding down rough edges, smoothing surfaces, and removing paint and coatings from brick and stone. They can efficiently tackle challenging surfaces where traditional grinding wheels may falter, due to their ability to conform to the shape of the material being worked on.
Beyond masonry, these flap discs are effective in other domains, including metalworking, woodworking, and automotive applications. In metalworking, they can be used for deburring, surface preparation, and finishing stainless steel or aluminum surfaces. Their flexibility makes them a favorite among professionals and hobbyists alike, as they provide a balance between material removal speed and surface finish quality.
masonry flap disc
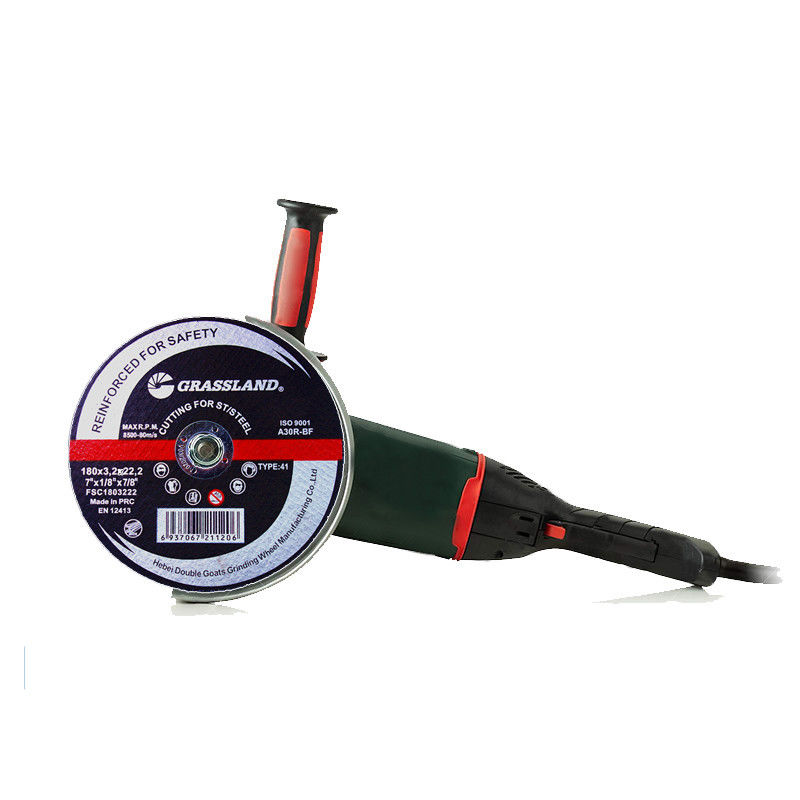
Choosing the Right Flap Disc
Selecting the appropriate masonry flap disc requires consideration of several factors. The material being worked on is the primary determinant. For most masonry applications, discs made from zirconia abrasives are preferred due to their durability and aggressiveness. However, if working on softer materials, aluminum oxide may provide a better finish without excessive wear on the disc.
Another vital aspect to consider is the angle of the flap disc. Discs are available in two primary configurations flat and conical. Flat flaps are suitable for surface grinding and finishing, while conical flaps are better for edge work and contouring. Choosing the right angle can improve efficiency and the quality of finish on the workpiece.
Safety Considerations
While using masonry flap discs, safety is paramount. Operators should always wear personal protective equipment (PPE), including safety goggles, gloves, and hearing protection. It is crucial to ensure that the grinder is in good condition and that the flap disc is mounted correctly. Operators should also be mindful of the work surface, maintaining a stable and secure position to prevent accidents.
Conclusion
Masonry flap discs are a game-changer for anyone involved in masonry work, providing efficiency and versatility that traditional grinding wheels cannot match. By understanding their construction, applications, and selection criteria, users can maximize the performance of their tools and achieve superior results in their projects. As with any tool, adherence to safety guidelines is essential to ensure a safe working environment. With the right flap disc in hand, the possibilities for masonry work are virtually limitless.
Post time:Sep - 30 - 2024