Metal Discs Cut to Size Precision Engineering for Various Applications
In the world of manufacturing and engineering, precision is key. One of the most critical components in numerous industries is the metal disc, which can be used in a variety of applications ranging from automotive parts to precision instruments. Custom metal discs cut to size are essential for achieving the specific requirements of projects, ensuring that each component fits perfectly in its intended application.
The Importance of Customization
Every project has unique specifications—whether it's regarding dimensions, thickness, or material type. Standard metal discs may not meet these specific needs, which is where custom metal disc cutting services come into play. By offering metal discs cut to size, manufacturers can provide solutions tailored to the exact requirements of their clients. This flexibility allows engineers to maintain designs without compromising quality or performance.
Materials Used for Metal Discs
Metal discs can be made from various materials, including aluminum, stainless steel, brass, and copper, among others. Each material offers distinct advantages
1. Aluminum Known for its lightweight properties and corrosion resistance, aluminum discs are ideal for applications where weight is a concern, such as in aerospace and automotive industries.
2. Stainless Steel This is one of the most widely used materials in the manufacturing of metal discs due to its strength and resistance to rust and corrosion. Stainless steel discs are commonly used in food processing, pharmaceuticals, and chemical industries.
3. Brass Known for its excellent machinability, brass discs are often used in electrical applications and are favored for their aesthetic appeal in decorative items.
Understanding the material properties allows manufacturers to recommend the best options for specific applications. Custom metal disc cutting can optimize material use while ensuring that the final product meets performance standards.
metal discs cut to size
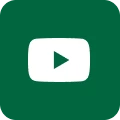
The Cutting Process
The process of cutting metal discs to size involves several techniques, each of which can provide different benefits based on the application. Some of the most common methods include
- Laser Cutting This process offers high precision and is suitable for intricate designs. Laser cutting is ideal for projects requiring tight tolerances and clean edges.
- Waterjet Cutting This method uses a high-pressure stream of water mixed with abrasive substances to cut through metal. Waterjet cutting is advantageous for thicker materials and is often used in industries where heat-sensitive materials are involved, as it doesn't alter the material properties.
- Die Cutting Commonly used for mass production, die cutting utilizes a sharp die to stamp out shapes from sheets of metal. This method is efficient for producing large quantities of uniform discs.
- Plasma Cutting This method is effective for cutting thick metal sheets and provides a fast cutting speed. While the precision is less than laser cutting, it is often more cost-effective for larger projects.
Choosing the correct cutting method is crucial to ensuring the finished discs meet not only the size requirements but also the necessary specifications for their intended use.
Applications of Metal Discs
The versatility of metal discs cut to size means they can be found in numerous applications. In the automotive sector, they are often used for brake components and other critical parts. In manufacturing, they can serve as bases for machinery, protective covers, or even decorative elements in finished products. Additionally, in industries like HVAC, they can function as flanges and fittings.
Conclusion
Custom metal discs cut to size play an indispensable role in modern manufacturing. Their tailored nature ensures that each component meets the precise needs of various applications, enhancing the overall quality and performance of final products. As industries evolve and demand for precision increases, the importance of custom metal disc services will only continue to grow, reinforcing the essential role of engineering and manufacturing in our daily lives.
Post time:Nov - 16 - 2024