The Importance of Metal Grinding Disks in Metalworking Operations
In the realm of metalworking, one of the key aspects that significantly influences the quality of finished products is the grinding process. At the heart of this process are metal grinding disks, essential tools used in various applications, including sharpening, shaping, and finishing metals. Understanding the significance, types, composition, and proper usage of these disks is crucial for achieving optimal results in metalworking operations.
What are Metal Grinding Disks?
Metal grinding disks, often referred to as grinding wheels or cut-off wheels, are abrasive tools designed to grind, shape, or cut metal surfaces. They are typically made from a combination of abrasive materials and bonding agents. These disks come in various shapes, sizes, and grit levels to suit different metalworking tasks, from heavy-duty grinding to fine finishing.
Types of Metal Grinding Disks
Grinding disks can be categorized based on their construction and intended applications
. The two most common types are1. Depressed Center Grinding Disks These are flat disks designed for grinding and finishing tasks on metal surfaces. Their unique design allows for effective grinding at various angles, making them suitable for blending and surface preparation.
2. Cut-off Disks Thin and flat, cut-off disks are designed specifically for cutting metal materials, such as rods, sheets, or pipes. They allow for precise cuts without generating excessive heat, which can damage the material.
Material Composition
metal grinding disk
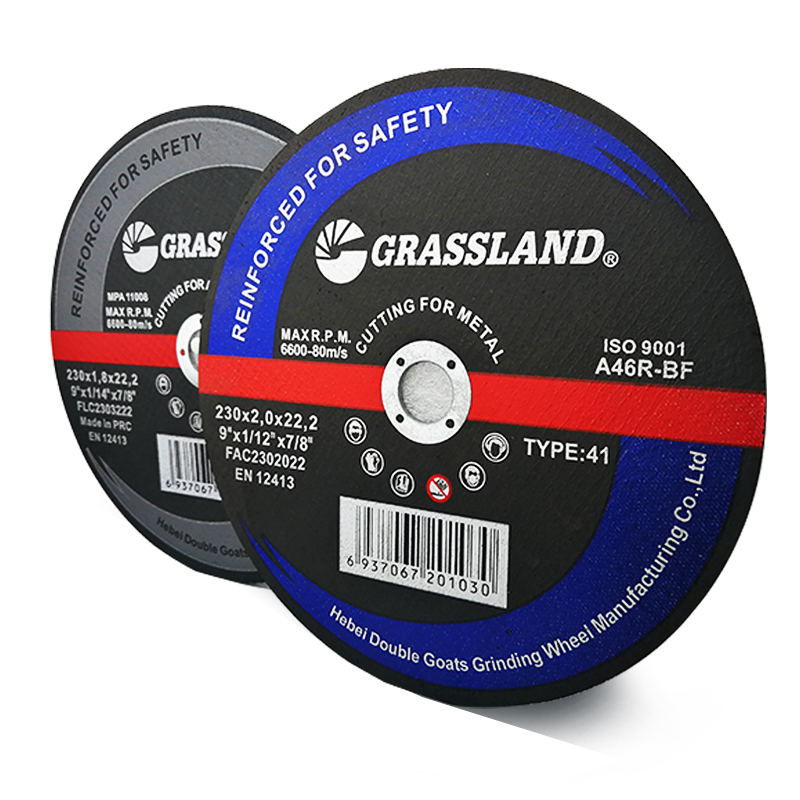
The performance of metal grinding disks largely depends on their material composition. Common abrasive materials include aluminum oxide, silicon carbide, and diamond. Aluminum oxide is widely used for general-purpose grinding, while silicon carbide is preferred for harder materials. Diamond grinding disks are exceptionally effective for cutting and grinding hard metals and ceramics due to their superior hardness.
Grit Size and Its Importance
The grit size of a grinding disk plays a critical role in determining the finish and efficiency of the grinding process. Disks are available in various grit sizes, ranging from coarse (lower numbers) to fine (higher numbers). Coarse grits are ideal for aggressive material removal and heavy grinding operations, while fine grits are used for finishing tasks, providing a smoother surface finish.
Proper Usage and Safety Considerations
Using metal grinding disks requires attention to safety and proper handling techniques. Operators should always wear appropriate personal protective equipment (PPE), including safety glasses, face shields, and hearing protection. It is essential to ensure that the grinding disk is compatible with the tool being used and that it is mounted securely before operation.
Additionally, users should avoid applying excessive pressure, as this can lead to overheating, disk breakage, or reduced service life. Following the manufacturer's guidelines for speed and usage can enhance the performance of the disks and ensure safe operation.
Conclusion
Metal grinding disks are indispensable tools in the metalworking industry, playing a vital role in achieving precise and effective grinding, cutting, and finishing of metal surfaces. By understanding the various types, materials, and proper usage of these disks, metalworkers can optimize their processes, enhance the quality of their products, and ensure safety in their operations. With advancements in technology, the future of metal grinding disks looks promising, with innovations likely to offer even greater efficiency and performance in metalworking applications. As industries continue to evolve, the importance of high-quality grinding tools remains paramount, reinforcing the role of metal grinding disks in modern manufacturing.
Post time:Nov - 20 - 2024