Understanding Radial Flap Disc A Versatile Tool for Surface Finishing
In the realm of industrial tooling, efficiency and versatility are key factors that determine the choice of equipment. One such innovative tool that has gained significant traction in recent years is the radial flap disc. This unique abrasive tool has transformed surface finishing and polishing applications across various industries. In this article, we will explore the features, advantages, and applications of radial flap discs.
What Is a Radial Flap Disc?
A radial flap disc is an abrasive tool designed for surface preparation and finishing. It consists of multiple layers of abrasive flaps that are bonded to a central backing plate. These flaps are arranged radially, which allows for a more efficient cutting action and improved surface coverage. Typically, radial flap discs are made from a variety of materials, including aluminum oxide, zirconia, and ceramic, making them suitable for a range of applications from metalworking to woodworking.
The design of the radial flap disc not only enhances its performance but also promotes durability. The flaps are flexible, which enables them to conform to the contours of the workpiece, providing a uniform finish. This adaptability makes radial flap discs ideal for working on irregular surfaces and achieving consistent results.
Advantages of Radial Flap Discs
The radial flap disc offers several advantages over traditional grinding wheels and abrasive belts. One of the most notable benefits is its ability to provide a cooler cutting action. The design of the disc allows for better ventilation during the grinding process, which reduces heat buildup. This is particularly important when working with heat-sensitive materials, as excessive heat can lead to warping or damage.
Another significant advantage is the ease of use. Radial flap discs can be mounted easily on standard backing pads, making them user-friendly for various power tools, including angle grinders and die grinders. This versatility means that operators can switch between different discs quickly, thereby increasing productivity.
radial flap disc
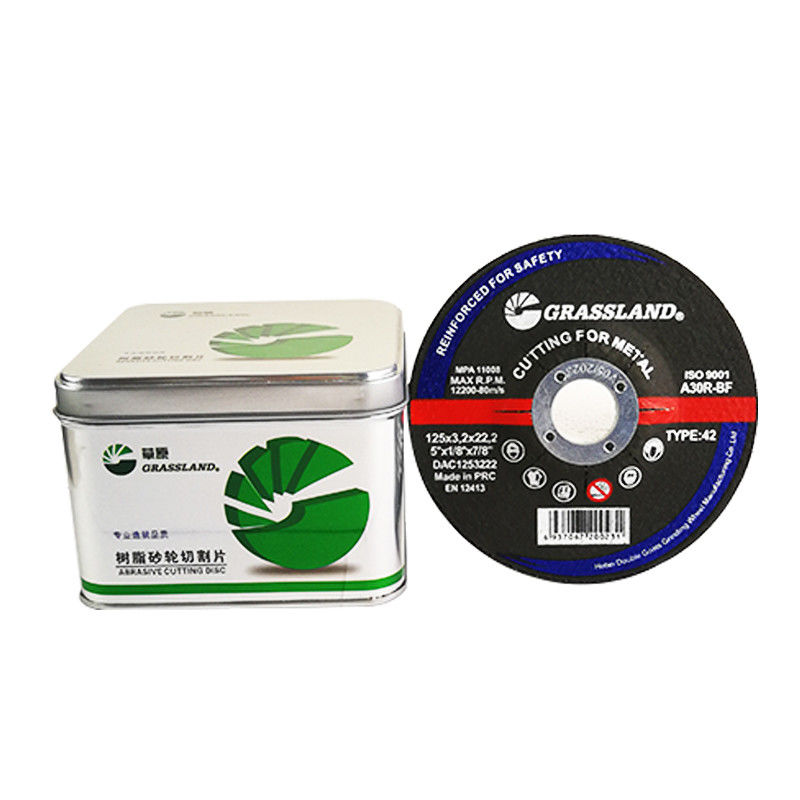
Moreover, radial flap discs are designed to wear evenly, promoting a longer lifespan compared to other abrasive tools. Users can expect a consistent performance throughout the life of the disc, which ultimately leads to cost savings. The effective utilization of abrasive material also reduces the frequency of disc replacements, minimizing downtime.
Applications of Radial Flap Discs
Radial flap discs find applications in a multitude of industries due to their versatility. In metalworking, they are commonly used for deburring, grinding, and finishing stainless steel, aluminum, and other metals. The ability to achieve a fine finish without altering the base material properties is a significant advantage in creating aesthetically pleasing and functional products.
In woodworking, radial flap discs can be used for sanding and shaping wooden surfaces. They provide an excellent finish while minimizing the risk of damaging the wood, making them an essential tool for carpenters and woodworkers.
Additionally, the automotive industry benefits from the use of radial flap discs for resurfacing parts, removing rust, and preparing surfaces for painting. Their efficiency and the quality of the finish they provide contribute to improved overall performance in automotive repair and maintenance.
Conclusion
The radial flap disc exemplifies innovation in abrasive technology, proving itself to be a crucial tool across various industrial applications. Its unique design offers benefits such as cooler cutting action, extended durability, user-friendliness, and versatility, making it a favorite among professionals in metalworking, woodworking, and automotive industries. As industries continue to seek efficient solutions for surface finishing, the radial flap disc will undoubtedly remain a valuable asset in achieving high-quality results. Whether you are a seasoned professional or a hobbyist, investing in a reliable set of radial flap discs can significantly enhance your operational efficiency and the quality of your finished products.
Post time:Dec - 12 - 2024