Understanding the Cutting Disk Performance for Metal Processing
In the realm of metal processing, ensuring efficient and effective cutting is crucial for achieving high-quality results. A key component in this process is the cutting disk, which serves as the primary tool for slicing through various metallic materials. Understanding the performance of these disks, often measured in terms of rendimiento or efficiency, can significantly impact productivity, cost management, and overall machining effectiveness.
What is Cutting Disk Performance?
Cutting disk performance can be defined as the ability of a cutting disk to efficiently cut through metal while maintaining quality and precision. This performance is typically measured by several factors, including cutting speed, durability, and the quality of the cut surface. The efficiency of a cutting disk is affected by its design, the materials from which it is made, and the specific conditions under which it is used.
Factors Influencing Cutting Disk Performance
1. Material Composition The type of material used in manufacturing cutting disks plays a crucial role in performance. Common materials include high-speed steel (HSS), carbide, and diamond. Each of these materials offers different levels of toughness, heat resistance, and wear resistance. For instance, diamond cutting disks are particularly effective for hard metals, offering high precision and longer durability.
2. Disk Design The design of the cutting disk, including its thickness, diameter, and tooth configuration, also affects its performance. Thicker disks tend to be more durable, while thinner disks can provide cleaner cuts. Additionally, the spacing and shape of the teeth on the disk must be optimized to ensure effective metal removal and minimize friction.
3. Cutting Speed and Feed Rate The relationship between cutting speed and feed rate is critical in determining rendimiento. Cutting speed refers to how fast the cutting disk moves through the material, while feed rate is the speed at which the disk advances into the material. Balancing these two parameters is essential; too high a feed rate can lead to overheating and premature wear, while too slow can decrease productivity.
rendimiento disco de corte para metal
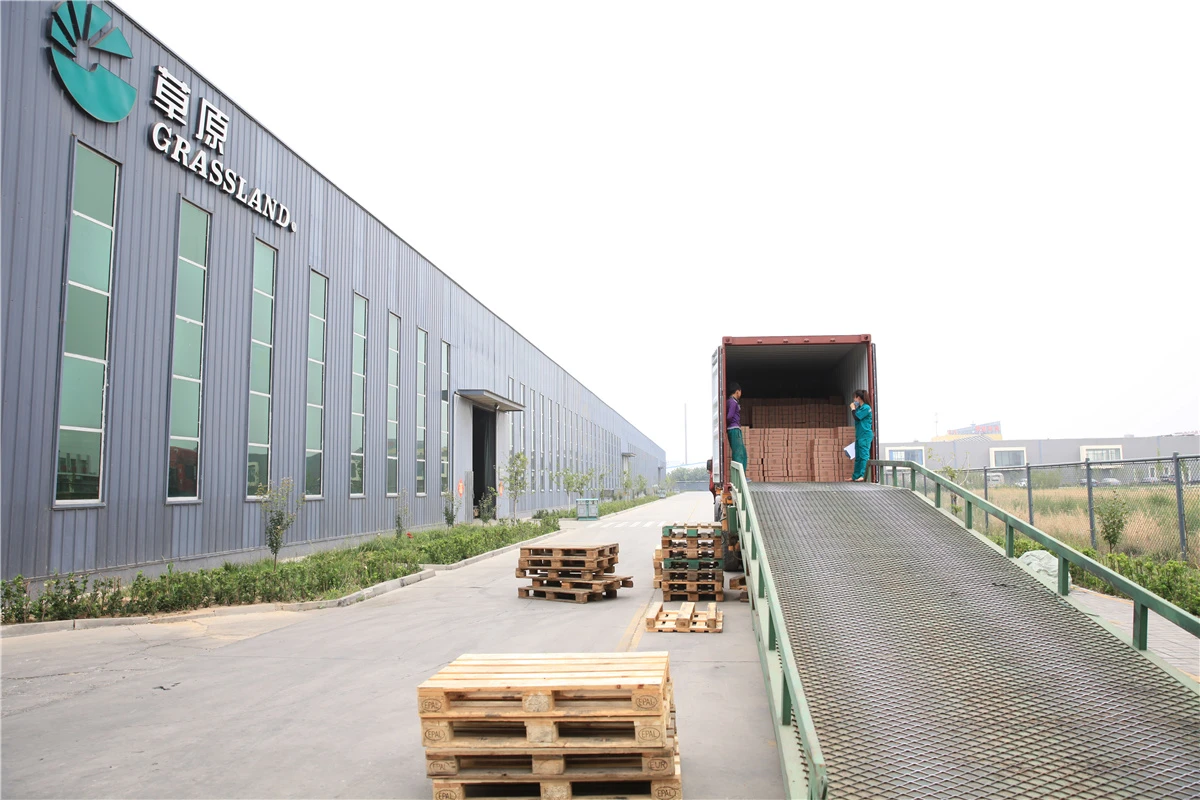
4. Cooling Methods Effective cooling reduces the heat generated during cutting, prolonging the life of the disk and improving cut quality. Employing proper coolant fluids or even air cooling techniques can significantly enhance rendimiento by maintaining lower operational temperatures.
5. Metal Type and Thickness Different metals require different cutting approaches. For example, cutting softer metals like aluminum can be done at higher speeds compared to harder steels. Similarly, thicker materials may require adjustments in both speed and pressure to avoid damaging the disk or producing poor-quality cuts.
Maximizing Cutting Disk Performance
To maximize cutting disk rendimiento, operators should adhere to several best practices
- Regular Maintenance Regular inspection and maintenance of cutting disks can prevent premature wear and ensure optimal performance. Replacing worn-out disks promptly is crucial for maintaining efficiency. - Proper Tool Selection Choosing the right type of cutting disk for the specific metal being worked on can drastically affect performance. Understanding the specifications of different disks and their ideal applications is essential.
- Optimizing Cutting Conditions Experimenting with different cutting speeds, feed rates, and cooling methods can lead to improvements in performance. Operators should document their settings and results to identify optimal conditions.
Conclusion
In conclusion, understanding and optimizing the rendimiento of cutting disks for metal processing is essential for achieving high-quality results with minimal downtime. By considering material composition, disk design, cutting parameters, and maintenance practices, operators can enhance performance, reduce costs, and improve overall productivity in metal machining operations. Emphasizing efficiency in this domain will not only lead to better outputs but also ensure the longevity and reliability of cutting equipment being used.
Post time:Oct - 03 - 2024