The Versatility and Utility of Sandpaper Flap Discs
Sandpaper flap discs are innovative abrasives designed to enhance efficiency in sanding, grinding, and finishing tasks across various applications. Characterized by overlapping layers of sandpaper positioned on a backing plate, these discs offer a unique combination of flexibility, durability, and versatility, making them indispensable tools in both industrial and DIY settings.
Structure and Design
The design of sandpaper flap discs contributes significantly to their effectiveness. Unlike traditional grinding wheels, flap discs are made of multiple layers of abrasive material, which can be made from aluminum oxide, zirconia alumina, or ceramic grains. These materials provide different degrees of hardness and durability, allowing users to select the right flap disc for their specific application. The disc's construction ensures that as the outer layers wear down, new abrasive layers are revealed, maintaining consistent performance over time.
Applications
One of the most appealing aspects of sandpaper flap discs is their wide range of applications. They can be used for stock removal, surface preparation, blending, and finishing on various materials, including metal, wood, and plastic. In metalworking, flap discs are preferred for their high-rate material removal compared to conventional grinding wheels. They are especially effective on stainless steel and aluminum, where reducing the risk of gouging and maintaining a smooth finish are critical.
In woodworking, these discs facilitate the controlled sanding of wooden surfaces, allowing for finer finishes without deep scratches. Their flexibility allows them to conform to contours and edges, making them ideal for working on intricate designs. Moreover, flap discs are commonly used in fabrication, automotive repair, and construction, proving their versatility across diverse industries.
Advantages
sandpaper flap disc
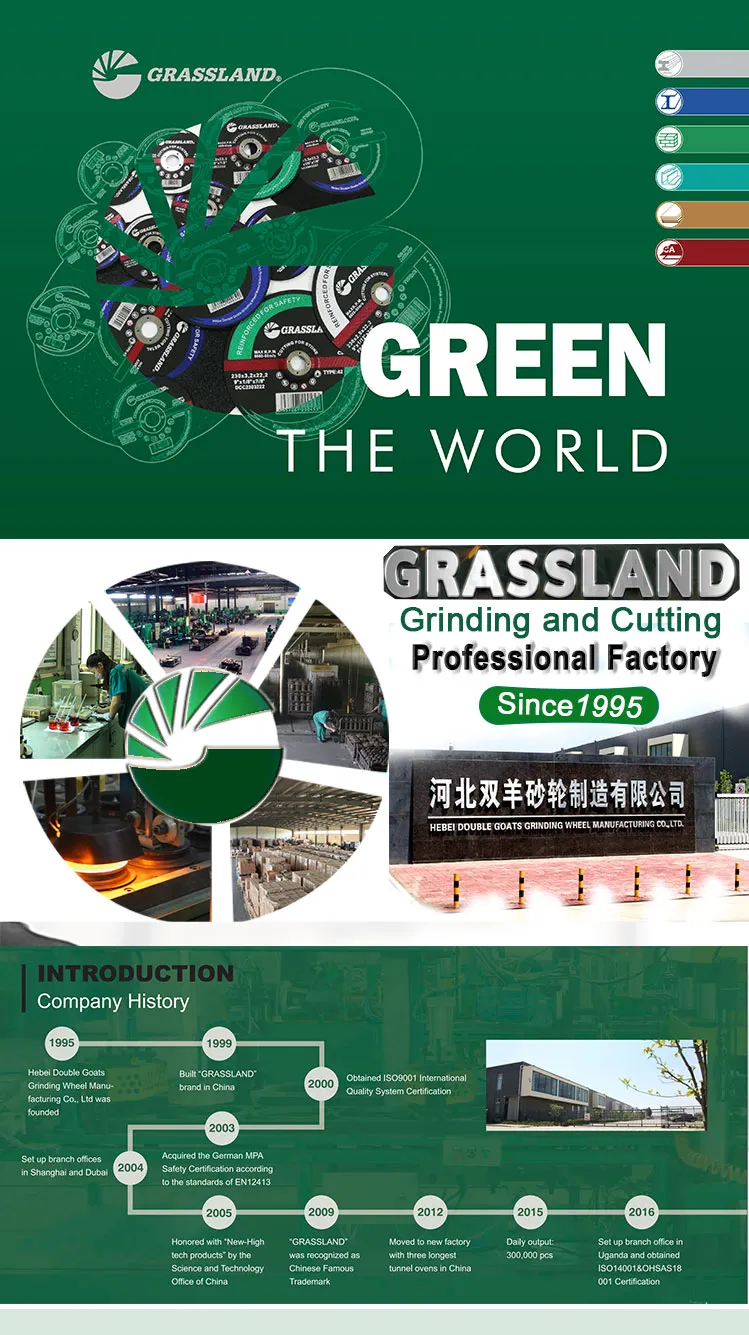
The advantages of using sandpaper flap discs are manifold. One of the most significant is their efficiency; users often achieve better results in less time. The multi-layer structure allows for an extended lifespan, reducing the frequency of disc changes and maximizing productivity. Additionally, flap discs produce less heat compared to traditional grinding wheels, minimizing the risk of warping or damaging the workpiece.
Another notable advantage is the improved surface finish achieved by flap discs. Because they blend rather than grind, they provide a smoother surface with fewer deep scratches. This quality is especially important in projects where aesthetics and surface integrity matter, such as in furniture making or metal art.
Choosing the Right Flap Disc
Selecting the appropriate flap disc involves considering several factors, including the material being worked on, the desired finish, and the power of the tool being used. Discs come in varying grits, from coarse to fine, allowing users to adjust their approach based on the task at hand. Coarser grits (like 40 or 60) are ideal for heavy material removal, while finer grits (up to 120 or more) are suitable for polishing and finishing tasks.
Furthermore, different shapes and designs of flap discs are available. The flat flap disc is ideal for flat surfaces, while conical or tapered designs allow for better access to corners and tight spaces. Understanding these options can significantly enhance the quality of work and efficiency in projects.
Conclusion
In summary, sandpaper flap discs have revolutionized sanding and grinding tasks, combining durability, efficiency, and versatility into a single tool. Their innovative design, coupled with a wide array of applications, makes them a favorite among professionals and DIY enthusiasts alike. Whether you are engaged in metalworking, woodworking, or general maintenance, flap discs are an invaluable asset that can streamline your work and enhance the quality of your projects. Investing in the right flap disc will not only improve performance but will also ensure a more satisfying finish to your endeavors.
Post time:Oct - 08 - 2024