Selection of Grinding Wheels Key Considerations for Optimal Performance
Grinding wheels are fundamental tools in the metalworking industry, serving a pivotal role in shaping, finishing, and enhancing the properties of materials. The effective choice of a grinding wheel can significantly impact the efficiency of the grinding process, the quality of the finished product, and the longevity of the tool itself. Therefore, understanding the various factors that influence the selection of grinding wheels is crucial for operators and engineers alike.
1. Understanding Grinding Wheel Composition
Grinding wheels are composed of abrasive particles held together by a bonding agent. The abrasives used may include aluminum oxide, silicon carbide, ceramic, or diamond, each offering distinct properties suited for specific applications. For instance, aluminum oxide is often used for grinding ferrous metals due to its durability, while silicon carbide is more effective for non-ferrous materials, including glass and ceramics. When selecting a grinding wheel, it is essential to match the wheel's abrasive material with the type of workpiece material to achieve optimal grinding efficiency.
2. Wheel Specification and Marking
Each grinding wheel is classified and marked based on several parameters, including width, diameter, and thickness. The specification also includes the wheel's grade, structure, and bond type. The grade reflects the hardness of the wheel—harder wheels provide better wear resistance but may require more force to grind, while softer wheels wear out more quickly but can produce a finer finish. Structure indicates the spacing between the abrasives, influencing the wheel's cutting action and ability to dissipate heat. Understanding these specifications helps in choosing a wheel that suits the intended grinding operation.
3. Application and Operation Considerations
selection of grinding wheel pdf
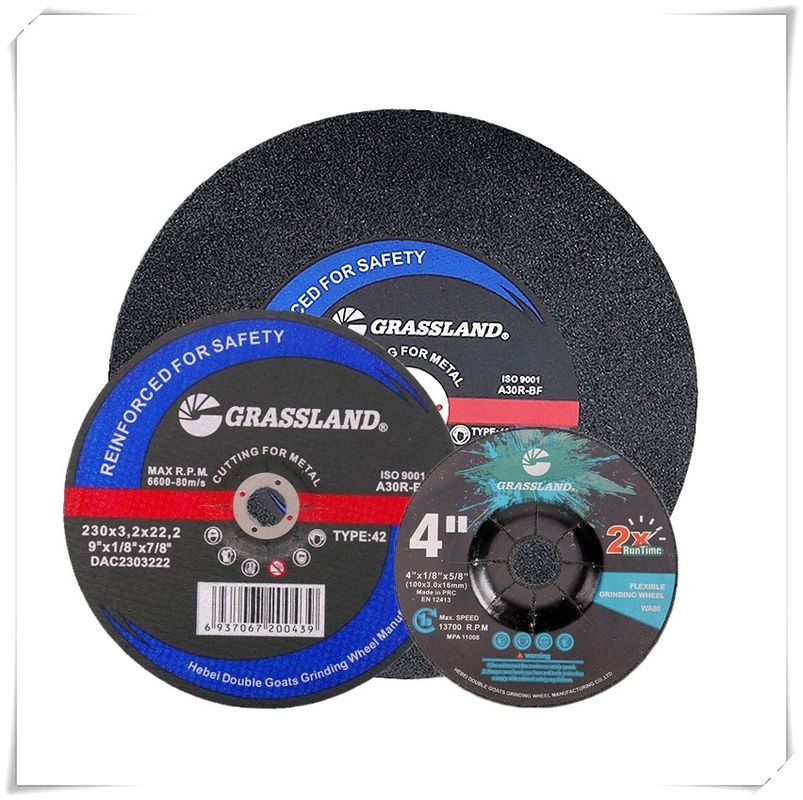
The type of grinding operation—surface grinding, cylindrical grinding, or internal grinding—will dictate the choice of wheel. For example, surface grinding requires wheels with a fine grit for achieving smooth finishes, whereas cylindrical grinding may benefit from coarser wheels to balance cutting speed and surface finish. It's also important to consider the machine's capability and the operating speed, as using a wheel with a speed rating lower than the machine's maximum can lead to safety hazards.
4. Safety Regulations and Standards
Safety is paramount in grinding operations. Selecting a wheel that complies with relevant safety standards—such as those established by the American National Standards Institute (ANSI) and the Occupational Safety and Health Administration (OSHA)—is imperative. These standards dictate the maximum allowable speeds, materials used, and testing procedures for wheels, ensuring that grinding operations are conducted safely and effectively. Operators should always inspect grinding wheels for any defects prior to use and adhere to safety guidelines during the grinding process.
5. Cost-effectiveness and Longevity
While the initial cost of grinding wheels can vary widely, considering the cost-effectiveness of the wheels in terms of performance and lifespan is critical. A wheel that lasts longer and maintains its cutting efficiency may prove more economical over time, even if its upfront cost is higher. Regular monitoring of wheel wear and replacing wheels as needed can maintain productivity and avoid costly downtime.
6. Conclusion
The selection of grinding wheels is a multifaceted decision that requires thorough consideration of the abrasive material, wheel specifications, application requirements, safety standards, and overall cost-effectiveness. By understanding these factors, operators can make informed choices that enhance productivity, improve product quality, and ensure safety. As grinding technology continues to evolve, staying updated on advancements in wheel technology and materials will further aid in optimizing grinding operations in various industrial settings. In summary, choosing the right grinding wheel is not merely a matter of preference; it is crucial for the success and efficiency of manufacturing processes, affecting both output quality and operational safety.
Post time:Nov - 26 - 2024