Understanding Steel Cutting Discs for Angle Grinders
Angle grinders are among the most versatile tools found in workshops and construction sites today. They are capable of performing a variety of tasks, including grinding, polishing, and cutting through different materials. One of the most essential accessories for an angle grinder is the steel cutting disc. This article explores the various aspects of steel cutting discs for angle grinders, giving you a comprehensive understanding of their features, applications, and best practices.
What are Steel Cutting Discs?
Steel cutting discs are circular blades designed specifically for cutting through metal, including steel, aluminum, and other ferrous and non-ferrous materials. Typically made from a combination of abrasives, these discs have a thin profile that allows for precision cuts and minimal material wastage. They are usually bonded with a resin or other binding agents, giving them the strength needed to withstand the forces exerted during cutting.
Types of Steel Cutting Discs
There are several types of steel cutting discs available on the market, each tailored to specific tasks
1. Abrasive Discs These are the most common type, composed of aluminum oxide or silicon carbide. They are effective for general cutting applications and are widely used due to their affordability.
2. Diamond Blades These cutting discs incorporate diamond particles in the bonding material, making them suitable for cutting hard materials, such as stainless steel and reinforced steel. They provide longer life and better performance compared to traditional abrasive discs.
3. Thin Cutting Discs Designed for precise cuts, these thinner discs generate less heat and material loss, making them ideal for delicate projects.
4. Thick Cutting Discs These are more robust and designed for heavy-duty cutting. While they may produce more heat, they are well-suited for larger projects requiring durability.
Selecting the Right Steel Cutting Disc
Choosing the correct cutting disc for your angle grinder is crucial for achieving optimal results
. Here are some factors to considersteel cutting disc for angle grinder
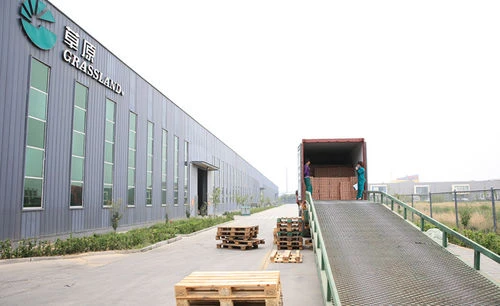
- Material Type Different materials require different discs. For instance, aluminum requires a special aluminum cutting disc to prevent warping and chemical reactions.
- Disc Thickness Thinner discs are suitable for light-duty tasks, while thicker ones are better for heavy-duty applications. Selecting the appropriate thickness helps improve safety and efficiency.
- Grain Size Discs with a finer grain size provide a smoother finish, while coarser grains are better for aggressive cutting.
- Manufacturer Recommendations Always check the manufacturer's guidelines for compatibility with your angle grinder and the type of work you intend to perform.
Safety Precautions
Cutting with angle grinders can be hazardous, so following safety precautions is paramount
1. Wear Personal Protective Equipment (PPE) Always use safety goggles, gloves, hearing protection, and face shields to guard against debris and sparks.
2. Check Discs Regularly Inspect cutting discs for signs of wear, cracks, or damage before use. A defective disc can shatter and cause injuries.
3. Use the Right RPM Ensure that the angle grinder’s RPM rating matches the cutting disc specifications. Using a disc beyond its rated speed increases the risk of breakage.
4. Maintain Proper Technique Always use a two-handed grip for better control, and avoid excessive force, as this can lead to accidents or disc breakage.
Conclusion
Steel cutting discs are invaluable tools for anyone looking to carry out metal cutting tasks with an angle grinder. By understanding the various types, selecting the correct disc for your application, and adhering to safety protocols, you can maximize the tool's performance and longevity while minimizing risks. Whether you are a professional tradesperson or a DIY enthusiast, mastering the use of steel cutting discs can significantly enhance your cutting capabilities, making your projects both more efficient and enjoyable.
Post time:Dec - 28 - 2024