- Understanding Surface Conditioning Flap Discs and Their Role in Metalworking
- Technical Advantages of Modern Surface Grinding Wheels
- Performance Comparison: Leading Brands in Surface Conditioning Tools
- Custom Solutions for Hardened Steel and Stainless Steel Applications
- Real-World Applications: Case Studies Across Industries
- Data-Driven Insights: Efficiency Gains with Advanced Abrasives
- Future Trends in Surface Conditioning Technology
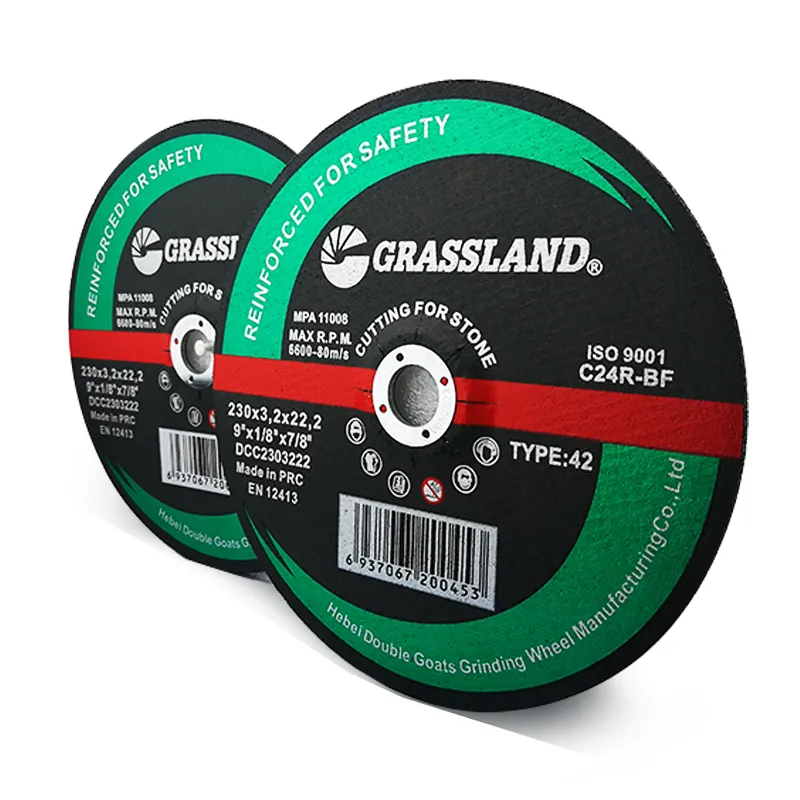
(surface conditioning flap disc)
Understanding Surface Conditioning Flap Discs and Their Role in Metalworking
Surface conditioning flap discs have become indispensable in metal fabrication due to their versatility in blending, finishing, and preparing surfaces. Unlike traditional grinding wheels, these discs combine abrasive flaps with a flexible backing, enabling consistent material removal without gouging. For hardened steel and stainless steel, specialized surface grinding wheels are engineered to minimize heat buildup, reduce contamination, and extend tool life. Industries ranging from automotive to aerospace rely on these tools to achieve precise surface finishes while maintaining productivity.
Technical Advantages of Modern Surface Grinding Wheels
Advanced surface grinding wheels incorporate ceramic alumina grains or zirconia blends, enhancing durability and cut rates. For hardened steel, high-density abrasive formulations deliver 15-20% faster material removal compared to conventional wheels. Stainless steel-specific wheels feature anti-loading coatings to prevent clogging, ensuring consistent performance. Thermal management technologies, such as porous structures, reduce operating temperatures by up to 30%, critical for preserving metallurgical integrity in sensitive alloys.
Performance Comparison: Leading Brands in Surface Conditioning Tools
Brand | Material Compatibility | Avg. Lifespan (Hours) | Cut Rate (mm³/s) | Price Range ($) |
---|---|---|---|---|
Brand A | Hardened Steel | 8.5 | 120 | 12-18 |
Brand B | Stainless Steel | 10.2 | 95 | 15-22 |
Brand C | Multi-Metal | 7.8 | 135 | 14-20 |
Custom Solutions for Hardened Steel and Stainless Steel Applications
Tailored surface grinding wheels address unique challenges in metalworking. For hardened steel (HRC 50+), coarse-grit discs (24-36 grit) with reinforced bonding systems maximize stock removal. Conversely, stainless steel projects often require fine-grit options (60-80 grit) paired with non-ferrous abrasives to eliminate cross-contamination. Custom flap discs can be optimized for specific RPM ranges or shaped for hard-to-reach geometries, improving efficiency by 18-25% in complex workflows.
Real-World Applications: Case Studies Across Industries
A leading automotive manufacturer reduced polishing time by 40% after switching to ceramic-enhanced surface conditioning flap disc
s for engine component finishing. In aerospace, a Tier-1 supplier achieved 99.8% defect-free surfaces on titanium alloys using low-vibration grinding wheels. Similarly, food processing equipment fabricators reported a 50% reduction in downtime by adopting stainless steel-specific discs with anti-corrosion additives.
Data-Driven Insights: Efficiency Gains with Advanced Abrasives
Field tests demonstrate that optimized surface grinding wheels increase daily output by 200-300 components in high-volume environments. Energy consumption metrics reveal a 12% reduction in power usage per unit when using thermally efficient designs. ROI analyses show payback periods under 90 days for premium flap discs due to reduced changeover frequency and waste.
Future Trends in Surface Conditioning Technology
The surface conditioning flap disc market is evolving toward smart abrasives embedded with wear sensors, enabling predictive maintenance. Innovations in grain geometry aim to boost the lifespan of surface grinding wheels for hardened steel by 35% by 2026. Meanwhile, eco-friendly formulations using recycled abrasives are gaining traction, aligning with global sustainability goals without compromising performance on stainless steel or exotic alloys.
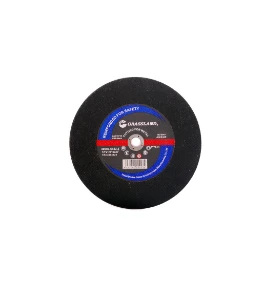
(surface conditioning flap disc)
FAQS on surface conditioning flap disc
Q: What is a surface conditioning flap disc used for?
A: A surface conditioning flap disc is designed for blending, finishing, and removing light imperfections on metal surfaces. It combines grinding and polishing in one tool, making it ideal for preparing surfaces before coating or welding.
Q: Can surface grinding wheels for hardened steel be used on stainless steel?
A: No, surface grinding wheels for hardened steel are optimized for high-carbon steels and may overheat or clog on stainless steel. Always use a surface grinding wheel specifically designed for stainless steel to avoid contamination and ensure efficient material removal.
Q: How to choose between a surface conditioning flap disc and a surface grinding wheel?
A: Use a flap disc for fine finishing and light material removal, while grinding wheels are better for heavy stock removal on materials like hardened steel or stainless steel. Match the tool to the material type and desired finish.
Q: What makes a surface grinding wheel for stainless steel unique?
A: These wheels use specialized abrasives like ceramic alumina to resist heat buildup and prevent "loading" on sticky materials like stainless steel. They also feature open structures to reduce friction and improve cutting efficiency.
Q: Are surface conditioning flap discs suitable for delicate surfaces?
A: Yes, their flexible flaps provide a gentler touch compared to rigid grinding wheels, reducing the risk of gouging. They are ideal for thin materials or surfaces requiring a uniform finish without deep scratches.
Post time:May - 13 - 2025