The Importance of Selecting the Right Surface Grinding Wheel for Stainless Steel
Surface grinding is an essential machining process used to achieve a smooth finish on flat surfaces. When it comes to grinding stainless steel, the selection of the appropriate grinding wheel is critical for optimizing performance, ensuring surface quality, and maintaining efficiency. This article explores the key factors to consider when choosing a surface grinding wheel specifically designed for stainless steel.
Understanding Stainless Steel
Stainless steel is a versatile material known for its corrosion resistance, durability, and strength. However, its unique properties also pose challenges during machining processes. Due to its toughness and work-hardening characteristics, stainless steel requires specific grinding wheels to avoid issues such as overheating, premature wear, and uneven finishes.
Types of Grinding Wheels
Grinding wheels come in various sizes, shapes, and compositions, each tailored for different applications. The two most common types of wheels for grinding stainless steel are aluminum oxide and cubic boron nitride (CBN) wheels.
1. Aluminum Oxide Wheels - These are the most widely used grinding wheels. They are effective for general-purpose grinding and are available in various grades. For stainless steel, the use of a harder grade of aluminum oxide (such as ceramic aluminum oxide) is recommended, as it provides better durability and can withstand the heat generated during the grinding process.
2. Cubic Boron Nitride Wheels - CBN wheels are ideal for high-speed grinding applications. They possess superior thermal stability and wear resistance, making them suitable for grinding tougher materials like hardened stainless steel. Although CBN wheels are more expensive, their longevity and performance can justify the cost in professional and industrial settings.
surface grinding wheel for stainless steel
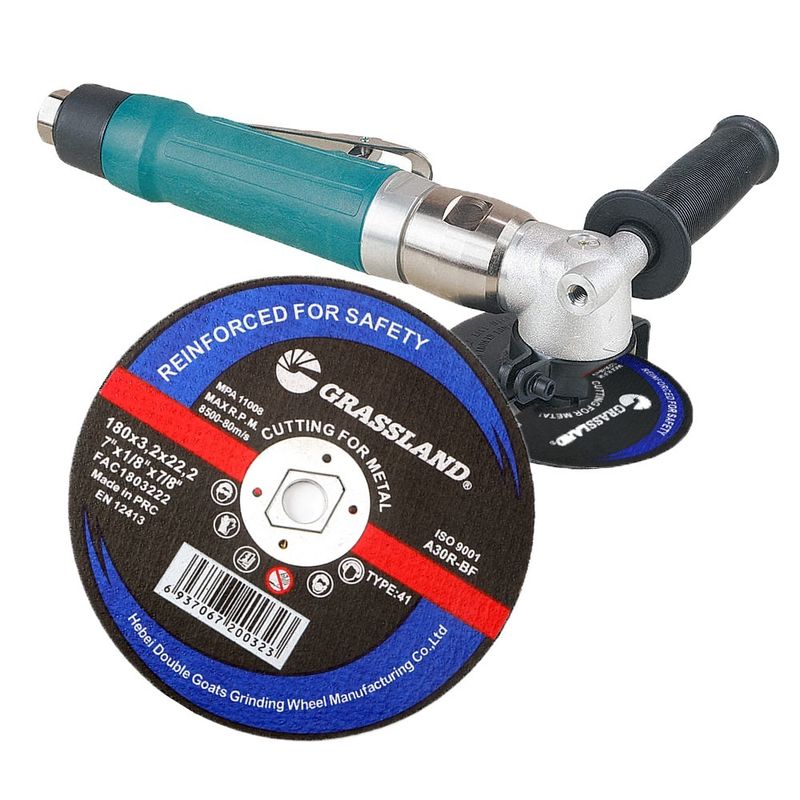
Key Factors to Consider
When selecting a surface grinding wheel for stainless steel, several factors must be taken into account
1. Grit Size - Grit size plays a crucial role in achieving the desired surface finish. Coarser grits (such as 36-60) are suitable for initial material removal, while finer grits (such as 80-120) are better for finishing operations. Selecting the right grit size based on the application can greatly enhance productivity and surface quality.
2. Bond Type - The bond type affects the wheel’s performance and lifespan. Resin bonds are commonly used for stainless steel as they provide good strength and flexibility. Vitrified bonds offer extra rigidity and are excellent for high-speed grinding, making them suitable for precision operations.
3. Wheel Speed - The speed at which the grinding wheel operates is a crucial factor. For stainless steel, it's essential to balance speed and feed rate to minimize heat generation and workpiece damage. Higher speeds may be necessary for achieving a finer finish, but they can also increase the risk of overheating.
4. Coolant Use - Utilizing a coolant during the grinding process is highly beneficial when working with stainless steel. It helps to dissipate heat, reduces friction, and prolongs the life of the grinding wheel. Additionally, proper coolant application can prevent the workpiece from warping, thus ensuring dimensional accuracy.
Conclusion
Choosing the right surface grinding wheel for stainless steel is vital for achieving optimal results in machining operations. By understanding the properties of stainless steel and the specifications of grinding wheels—such as the type of abrasive, grit size, bond type, and operational parameters—manufacturers and machinists can enhance productivity, reduce costs, and improve overall surface quality. Investing time in selecting the correct grinding wheel not only extends tool life but also guarantees superior finishes that meet stringent industry standards. Whether in automotive, aerospace, or general manufacturing, the right grinding solutions are key to efficient machining processes.
Post time:Nov - 28 - 2024