T27 vs T29 Flap Discs A Comprehensive Comparison
When it comes to metal fabrication and surface preparation, flap discs have become an indispensable tool in the arsenal of craftsmen, fabricators, and DIY enthusiasts alike. Among the plethora of options available in the market, two of the most commonly discussed types are T27 and T29 flap discs. Each type serves its purpose effectively, but understanding the differences between them can greatly enhance the results of your work.
Understanding Flap Discs
Before delving into the specifics of T27 and T29 flap discs, it’s essential to understand what flap discs are and how they work. Flap discs are a type of abrasive tool consisting of multiple overlapping sanding flaps attached to a backing plate. These flaps are made from sandpaper or other abrasive materials, designed primarily for grinding, polishing, and finishing applications. The choice between different types, such as T27 and T29, involves considerations of the materials being worked on, the desired finish, and the angle of work.
T27 Flap Discs
T27 flap discs are characterized by their flat surface profile. This design makes them particularly effective for operations requiring a smoother finish and a more controlled grinding process. The T27 profile allows for precision abrasive action, making them ideal for grinding flat surfaces and achieving a scratch-free finish. They are best suited for use on materials such as steel and other metals that need a fine, even finish. Moreover, T27 discs are popular for applications involving weld removal and surface preparation as they can reach into corners and contours effectively without compromising the workpiece integrity.
One of the significant advantages of T27 flap discs is their versatility. They can be used at a wide range of angles, though they are most effective when used at a 0-15 degree angle to the surface. This position allows for maximum contact area and effective material removal with minimal risk of gouging the workpiece.
T29 Flap Discs
t27 vs t29 flap disc
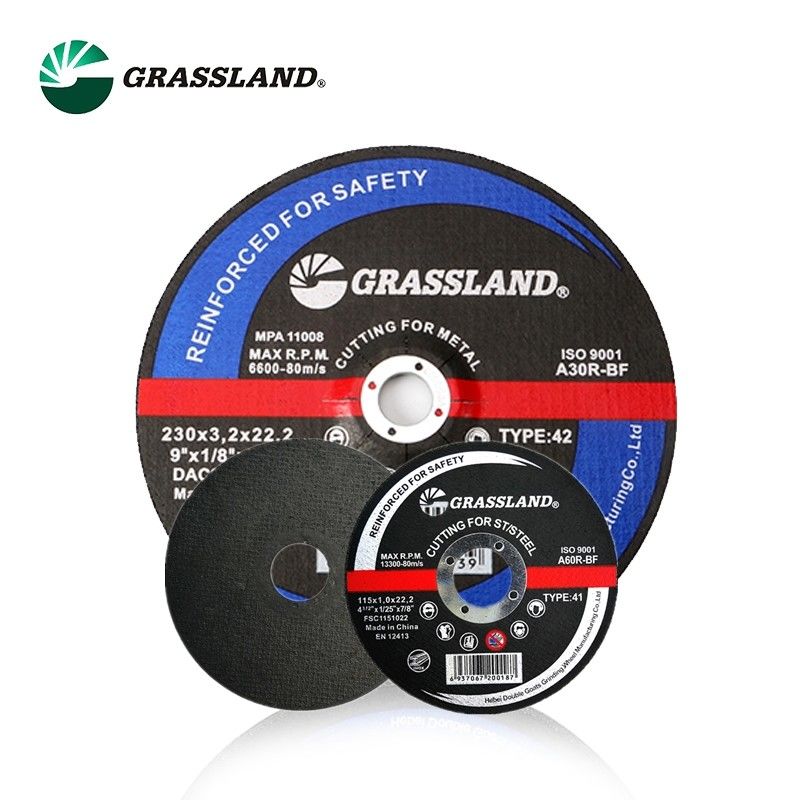
In contrast, T29 flap discs are distinguished by their conical shape. This design allows for a more aggressive grinding action and is particularly effective in applications where material removal speed is prioritized. The angled flaps of T29 discs enable them to be used at a more pronounced angle, typically between 15-25 degrees. This allows the operator to apply more force without risking the integrity of the workpiece, making T29 discs the go-to choice for heavy-duty grinding and stock removal.
T29 flap discs shine in applications where quick material removal is crucial, such as in fabrication environments where welds need to be ground down flat or in heavy metalworking tasks. They can produce a deeper cut and are often used in conjunction with more robust power tools.
Making the Right Choice
When deciding between T27 and T29 flap discs, it is crucial to consider the specific requirements of your task. If you are looking for a finish that is smooth and refined, or if your work involves working with delicate metals or finishing applications, T27 flap discs are the way to go. Conversely, if your project involves significant material removal, such as in initial grinding or heavy-duty weld cleaning, T29 discs would serve better.
Moreover, it’s important to consider the workpiece material. While both T27 and T29 discs can be used on a variety of metals, the thickness and density of the material can influence performance. For tougher materials, T29 discs will likely provide a better result, whereas T27 discs may be preferable for more delicate applications.
Conclusion
In summary, T27 and T29 flap discs each have unique characteristics that suit different types of work. Understanding the distinctions between these two types can significantly impact the efficiency and quality of your craftsmanship. Whether you are polishing a surface to a smooth finish or removing heavy material, choosing the right flap disc for the job is key to achieving optimal results. Ultimately, investing time in selecting the right disc will not only enhance your current projects but also improve your overall skill as a metalworker.
Post time:Dec - 05 - 2024