The Principles and Applications of Thin Cut-Off Discs
Thin cut-off discs are essential tools in various industries, particularly in metalworking, construction, and automotive sectors. These discs, designed for precision cutting, offer a range of benefits that improve efficiency and quality in various applications. In this article, we will explore the characteristics, uses, and advantages of thin cut-off discs, as well as the factors to consider when selecting the right disc for your needs.
Understanding Thin Cut-Off Discs
Thin cut-off discs, typically made from abrasive materials such as aluminum oxide or silicon carbide, are engineered to provide a thin profile for precise cuts. Their thickness usually ranges from 0.8 mm to 2.5 mm, allowing for minimal material removal while achieving clean edges. This design helps to reduce heat generation, thereby minimizing warping and damage to the workpiece. Furthermore, their lightweight nature makes them easier to handle and reduces strain on the machinery during operation.
Common Applications
Thin cut-off discs find application in various fields. In metalworking, they are primarily used for cutting steel, stainless steel, and other metals into desired shapes or sizes. Builders and contractors often rely on these discs for rapidly slicing through rebar, metal studs, and piping. In the automotive industry, thin cut-off discs are perfect for tasks such as exhaust system fabrication, engine repair, and bodywork, where precision cutting is critical.
Beyond metalworking, these discs are also utilized for cutting ceramics, plastics, and composites. Their versatility makes them an invaluable asset in workshops, where multiple materials may need to be processed. Additionally, industries such as fabrication, construction, and shipbuilding have integrated thin cut-off discs as a staple in their toolkits.
Advantages of Thin Cut-Off Discs
1. Precision Cutting One of the primary advantages of thin cut-off discs is their ability to make precise cuts. With a thinner blade, less force is required, resulting in cleaner edges that often require minimal finishing work afterward.
thin cut off disc
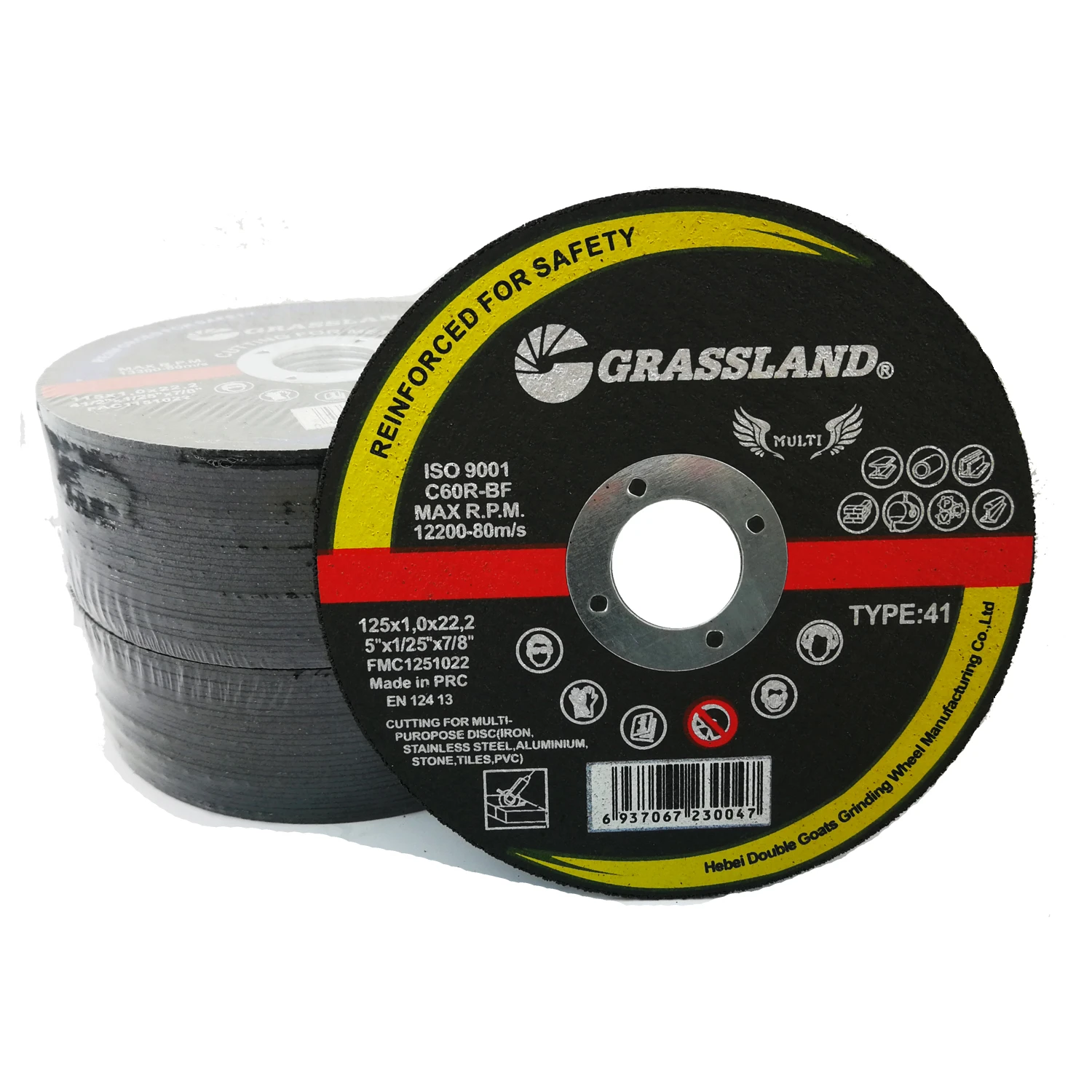
2. Reduced Heat Generation Because of their thin design, these discs generate less friction during cutting, leading to lower heat buildup. This characteristic helps to preserve the integrity of the material being cut, preventing issues such as discoloration or warping.
3. Economical Use of Material The thin edge allows for smaller kerf loss, meaning that less material is wasted during the cutting process. This factor not only saves costs but also maximizes the efficiency of the material being processed.
4. Versatility Thin cut-off discs can be used with a variety of tools, including angle grinders, handheld saws, and stationary machines. Their adaptability makes them suitable for different environments and applications.
5. Speed and Efficiency Thin cut-off discs enable faster cutting speeds compared to thicker alternatives. This efficiency is crucial in time-sensitive projects, where rapid turnaround is required.
Selection Criteria
When choosing a thin cut-off disc, several factors should be considered. These include the type of material to be cut, the thickness of the disc, the grit size of the abrasive material, and the operating speed of the cutting machine. Matching the disc’s specifications to the intended application ensures optimal performance and longevity.
Conclusion
Thin cut-off discs are indispensable tools in many industries, providing the precision and efficiency required for effective material processing. Their advantages, including minimal heat generation and economical material use, make them a preferred choice for professionals. When selecting a cut-off disc, it is essential to consider the specific requirements of your project to maximize performance and achieve the best results. Embracing the capabilities of thin cut-off discs can lead to enhanced productivity and quality in your work, no matter the industry.
Post time:Dec - 12 - 2024