Understanding Thin Cutting Discs A Comprehensive Guide
In the world of fabrication and metalworking, the tools and materials we use can make a significant difference in the quality of our work. Among these tools, thin cutting discs have become increasingly popular due to their efficiency and versatility. This article aims to provide a comprehensive understanding of thin cutting discs, their applications, advantages, and how to choose the right one for your projects.
What Are Thin Cutting Discs?
Thin cutting discs, also known as cutting wheels or cutting burrs, are specialized tools designed for cutting through various materials, including metal, stainless steel, aluminum, and even certain types of plastics. Typically, these discs are made from materials like fiberglass, resin, and grit, which allow them to slice through tough materials with ease.
The thickness of these cutting discs generally ranges from 0.8 mm to 3 mm, with ultra-thin discs providing greater precision and faster cuts. This thin profile reduces the amount of material lost during cutting, making them an economical choice for both professional and DIY applications.
Applications of Thin Cutting Discs
Thin cutting discs are remarkably versatile and are employed in a wide range of applications. Some of the most common uses include
1. Metal Fabrication In metalworking shops, thin cutting discs are frequently used for cutting metal sheets, bars, and profiles. Their reduced thickness allows for clean, precise cuts that minimize the need for additional finishing.
2. Construction In construction, thin cutting discs are utilized to cut rebar, masonry, and metal cladding, helping to improve the efficiency of construction projects.
4. Plumbing Plumbers frequently turn to these discs for cutting pipes and fittings made from copper, PVC, or steel.
5. Art and Craft Projects Hobbyists utilize thin cutting discs for intricate cutting tasks in artistic projects, such as metal sculptures or detailed metalworking.
thin cutting disc
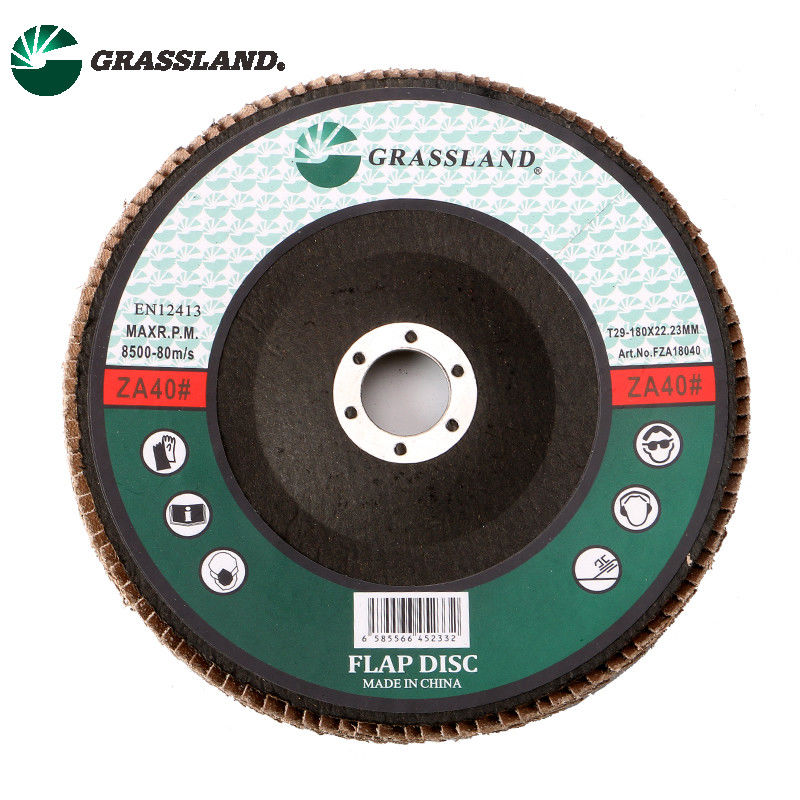
Advantages of Thin Cutting Discs
One of the primary advantages of thin cutting discs is their ability to provide clean and precise cuts while generating minimal heat. This is especially important when working with materials that can warp or melt due to excessive heat generated during cutting. Furthermore, the reduced kerf width—resulting from their thin design—minimizes material waste, making them a cost-effective solution for many projects.
Another advantage is their lightweight nature. Thin cutting discs require less powerful tools, making them easier to handle and reducing the fatigue experienced during extended use. Additionally, their speed and efficiency can significantly enhance productivity, allowing users to complete projects quicker without sacrificing quality.
How to Choose the Right Thin Cutting Disc
Selecting the right thin cutting disc is crucial for achieving the best results. Here are several factors to consider
1. Material Compatibility Ensure that the disc you select is appropriate for the material you will be cutting. Discs are often labeled for specific materials, including metal, tile, or concrete.
2. Thickness Choose a disc thickness that balances precision and cutting speed. Thinner discs are ideal for delicate work, whereas slightly thicker discs may be better for heavy-duty applications.
3. Size Cutting discs come in various diameters. It's important to choose one that fits your angle grinder or cutting tool correctly to avoid any safety hazards.
4. Grit Type The grit of the disc determines its cutting ability and finish. Finer grits are suited for finishing work, while coarser grits are designed for rapid cutting.
5. Brand and Quality Invest in reputable brands known for quality and durability. High-quality discs not only perform better but also last longer, which can save you money over time.
Conclusion
Thin cutting discs are indispensable tools across multiple industries, offering precision, efficiency, and versatility. By understanding their applications, advantages, and how to select the right disc, users can enhance their projects' outcomes, whether in professional environments or DIY endeavors. As technology evolves, these cutting tools are likely to see advancements that will further improve their performance, making them an essential component in the toolkit of anyone who works with materials requiring precision cutting.
Post time:Dec - 07 - 2024