Comparing Type 27 and Type 29 Flap Discs A Comprehensive Guide
When it comes to grinding and finishing applications, flap discs are indispensable tools in the metalworking industry. They come in various types, with Type 27 and Type 29 being among the most commonly used. Both types serve the purpose of sanding, grinding, and polishing metal surfaces, but their design and application differ significantly. This article will delve into the differences, advantages, and best uses of Type 27 and Type 29 flap discs, helping you make an informed decision for your specific needs.
Design Differences
The primary distinction between Type 27 and Type 29 flap discs lies in their shape and angle. Type 27 flap discs have a flat profile, which allows for a greater grinding surface area and provides a smoother finish on flat surfaces. This type is particularly effective for surface preparation and finishing applications, where a consistent surface is desired.
In contrast, Type 29 flap discs feature a conical shape that allows for aggressive grinding and is particularly useful for tasks that require more effective contouring. The angled design provides better contact with the surface, making it ideal for weld blending and edge work. The conical shape enables the user to reach into corners and tight spaces, which is a significant advantage in various metalworking applications.
Performance and Applications
Both types of flap discs are filled with abrasive flaps made from materials like zirconia, aluminum oxide, or ceramic. Type 27 discs are generally preferred for flat surface grinding because they minimize the risk of gouging the material. They are often used in applications where finer finishes are necessary, such as in the automotive or aerospace industries.
On the other hand, Type 29 flap discs excel in tasks that require more aggressive material removal and shaping. These discs are commonly used in metal fabrication and welding industries, where efficiency and speed are paramount. The angled design allows the user to apply pressure effectively, which enhances their performance on heavy stock removal tasks.
type 27 vs 29 flap disc
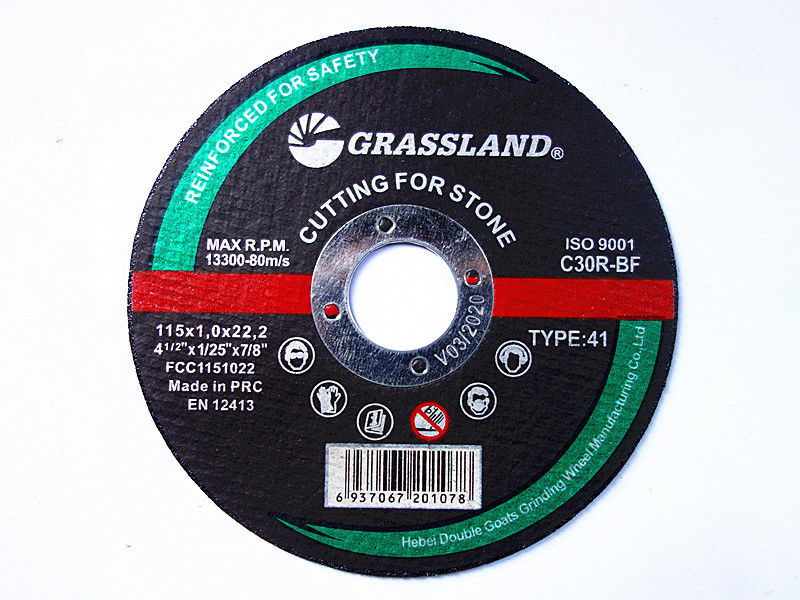
User Experience and Efficiency
Another essential factor to consider is user experience. Type 27 flap discs are typically easier to control, making them suitable for beginners or for applications requiring precision. Their flat design allows for even wear, which can extend the life of the disc when used properly. This feature is particularly important for achieving consistent finishes across multiple components.
Type 29 flap discs, while more aggressive, require a higher skill level to operate effectively. Their conical shape necessitates a proper technique to avoid damaging the workpiece. However, for experienced users, these discs can significantly reduce grinding time and increase overall productivity, making them indispensable for heavy industrial applications.
Conclusion
In summary, choosing between Type 27 and Type 29 flap discs depends largely on the specific requirements of your project. If your work involves flat surfaces whose finish is paramount, Type 27 flap discs are the ideal choice. They offer smooth performance, control, and longevity, making them perfect for finishing tasks.
Conversely, if you need a tool that can handle aggressive material removal and is capable of blending welds and contours, Type 29 flap discs are the way to go. Their design allows for faster work and excellent efficiency, particularly in more demanding scenarios.
Ultimately, understanding the differences in design, performance, and user experience between Type 27 and Type 29 flap discs will help you make the right decision for your metalworking needs. Whether you are a novice technician or an experienced fabricator, having the right tools at your disposal can make all the difference in achieving optimal results. Always remember to assess the specific requirements of your project and choose the flap disc that aligns best with your objectives.
Post time:Dec - 11 - 2024