Understanding the Differences Between Type 27 and Type 29 Flap Discs
When it comes to metalworking, using the right tools can significantly influence the quality of work. Among these tools, flap discs are extensively utilized for grinding, blending, and finishing metal surfaces. The two most common types of flap discs are Type 27 and Type 29, each designed for specific applications and offering unique advantages. This article aims to elucidate the differences between these two types, helping professionals make informed decisions based on their unique needs.
Design and Structure
The primary distinction between Type 27 and Type 29 flap discs lies in their design. Type 27 flap discs feature a flat configuration, with flaps that are oriented parallel to the disc face. This flat design makes them ideal for flat surfaces and applications where a smooth finish is desired. They are particularly effective for grinding and finishing on flat surfaces, providing an even application of material removal.
On the other hand, Type 29 flap discs have a slightly conical or angled shape. This design allows for more aggressive grinding and is excellent for contouring and carving out materials. The angled flaps of Type 29 discs provide a better surface area contact, enabling them to reach into grooves and contoured surfaces more efficiently. Therefore, Type 29 flap discs are particularly advantageous for tasks that involve edges or contours that require more aggressive material removal.
Applications
Both types of flap discs are versatile and can be used in various applications, but they shine in specific areas
.Type 27 flap discs are often used for finishing applications, including weld blending, surface preparation, and paint removal. Their flat shape allows for a smoother finish on wood, metal, and plastic surfaces. They are perfect for tasks that demand a delicate touch, such as working with thin materials that could be damaged by aggressive grinding.
type 27 vs type 29 flap disc
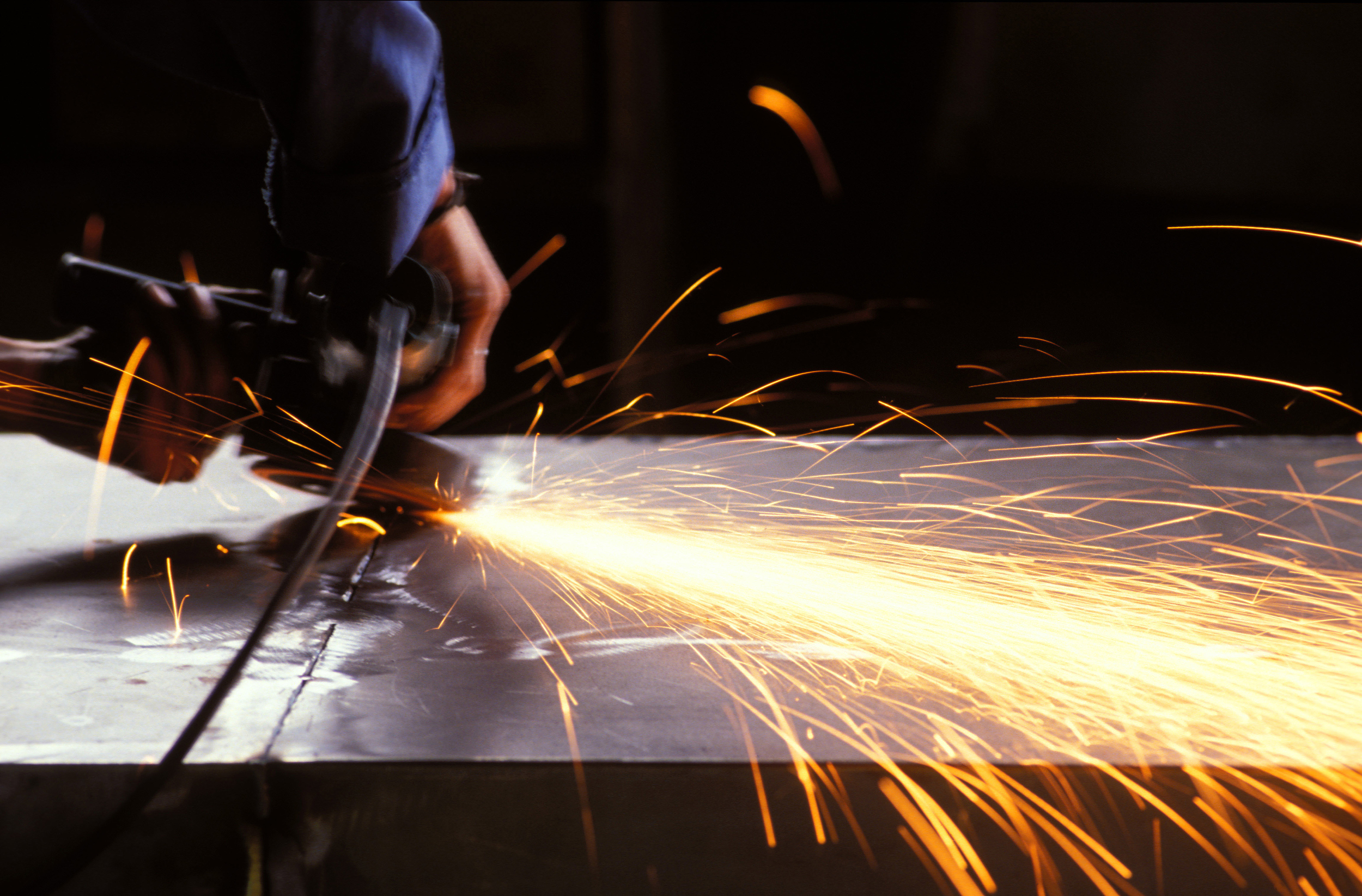
Conversely, Type 29 flap discs are built for heavy-duty grinding tasks. They are commonly utilized in the fabrication industry for tasks like weld grinding, removing heavy stock, and surface shaping. The angled configuration allows them to tackle rough surfaces and heavy materials effectively, making them suitable for metal fabrication, automotive repair, and similar industries.
Material Compatibility
Both types of flap discs can utilize various abrasive materials, including zirconia, aluminum oxide, and ceramic. However, the material choice can further optimize their performance.
Type 27 discs are often preferred for softer materials, where a finer finish is required. Aluminum oxide flaps are particularly useful for general purpose grinding of steel, while ceramic flap discs offer enhanced durability for tougher grinding tasks.
In contrast, Type 29 flap discs are typically favored when working with harder materials. Zirconia flap discs are popular for their aggressiveness and lifespan, making them perfect for steel and stainless steel applications. The conical design, paired with high-quality abrasive materials, allows these discs to perform efficiently even with heavy-duty applications.
Final Thoughts
In summary, the choice between Type 27 and Type 29 flap discs ultimately depends on the specific needs of the task at hand. Type 27 flap discs are ideal for finishing and general-purpose tasks requiring a smooth surface, while Type 29 flap discs excel in aggressive grinding and contouring applications. Understanding these differences will empower metalworking professionals to select the appropriate flap disc, optimizing their performance and achieving high-quality results.
Both types of flap discs play crucial roles in the metalworking industry, and selecting the right one can enhance productivity, reduce finishing times, and ensure that projects meet the desired quality standards. By considering the application, desired finish, and the materials involved, professionals can make informed choices that lead to successful outcomes in their metalworking endeavors.
Post time:Dec - 11 - 2024