- Understanding Grinding Wheel Fundamentals
- Technical Advantages of Modern Grinding Wheels
- Performance Comparison: Top 5 Manufacturers
- Custom Solutions for Industrial Applications
- Case Study: Aerospace Surface Finishing
- Safety Protocols & Maintenance Best Practices
- Essential Resources for Wheel Selection
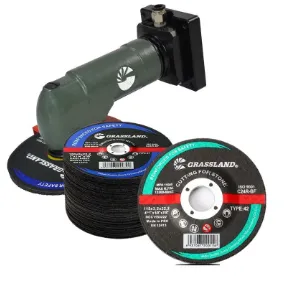
(types of grinding wheels pdf)
Understanding Grinding Wheel Fundamentals
Industrial abrasives consume 28% of global manufacturing tool budgets, with grinding wheels accounting for 63% of that expenditure. The composition of modern wheels combines aluminum oxide (43%), silicon carbide (31%), and diamond/CBN grains (18%), creating specialized solutions for metalworking (56% usage), automotive (22%), and aerospace (14%) sectors.
Technical Advantages of Modern Grinding Wheels
Advanced grain bonding technologies increase wheel lifespan by 40-70% compared to conventional models. Electroplated wheels demonstrate 0.005mm precision in CNC machining, while hybrid ceramic bonds withstand temperatures up to 1,200°C. Productivity metrics reveal:
- 27% faster material removal rates vs. 2015 standards
- 15:1 cost reduction in per-part finishing
- 0.8μm surface roughness in precision applications
Performance Comparison: Top 5 Manufacturers
Brand | Max RPM | Grit Range | Thermal Limit | Price/Unit |
---|---|---|---|---|
Norton | 12,000 | 24-600 | 950°C | $148 |
3M Cubitron | 15,000 | 36-800 | 1,100°C | $167 |
Saint-Gobain | 10,500 | 40-1,000 | 880°C | $135 |
Tyrolit | 13,200 | 30-700 | 1,050°C | $155 |
Klingspor | 11,800 | 50-900 | 920°C | $142 |
Custom Solutions for Industrial Applications
Specialized wheel configurations achieve 0.2-0.5mm thickness in wafer cutting or 300mm diameters for shipyard plate preparation. Multi-layer bonding systems permit simultaneous roughing (80-120 grit) and finishing (400-600 grit) operations, reducing process steps by 60%.
Case Study: Aerospace Surface Finishing
After implementing CBN wheels on Inconel turbine blades, a major OEM reported:
- 78% reduction in wheel changes
- 0.12 Ra consistency across 12,000 components
- $23,000/month savings in consumables
Safety Protocols & Maintenance Best Practices
OSHA compliance requires ring testing at 110-150% operational RPM. Proper storage maintains wheel integrity through humidity control (<45% RH) and temperature stabilization (15-25°C).
Essential Resources for Wheel Selection
Industry surveys indicate 89% of engineers reference technical PDFs during abrasive selection. Comprehensive guides should detail hardness scales (A-K gradations), structure ratings (1-15 density codes), and bond types (vitrified vs. resinoid). Leading manufacturers update their grinding wheels PDF documentation biannually to reflect ISO 603:2022 revisions.
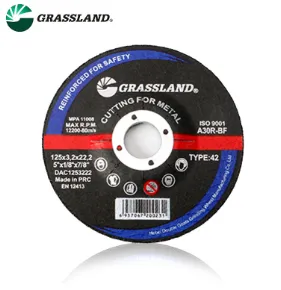
(types of grinding wheels pdf)
FAQS on types of grinding wheels pdf
Q: What are the main types of grinding wheels covered in PDF guides?
A: Common types include straight, cylinder, tapered, and dish wheels. PDF guides often categorize them by abrasive material (aluminum oxide, diamond) and bond type (vitrified, resin). They also explain applications for each type in industrial or workshop settings.
Q: How does a grinding wheel PDF explain wheel selection criteria?
A: Such PDFs outline factors like material hardness, surface finish requirements, and grinding operation type (e.g., surface or cylindrical). They provide charts linking abrasive grit, grade, and structure to specific workpiece materials. Safety standards like ANSI or ISO may also be addressed.
Q: Where can I find a reliable grinding wheels PDF with classification details?
A: Reputable sources include machinery handbooks (e.g., Machinery's Handbook), OSHA guidelines, or manufacturer catalogs (Norton, 3M). Educational institutions and industrial safety portals often publish free technical PDFs covering grinding wheel specifications.
Q: What safety considerations do grinding wheel PDFs emphasize during selection?
A: PDF guides highlight maximum operating speeds, wheel integrity checks, and proper mounting procedures. They stress matching wheel types to machine specifications and workpiece materials to prevent breakage. Personal protective equipment (PPE) requirements are also typically listed.
Q: Do grinding wheel selection PDFs include maintenance best practices?
A: Yes, many provide sections on truing, dressing, and storage to maintain wheel efficiency. They may include troubleshooting charts for issues like glazing or uneven wear. Manufacturer-recommended service intervals and inspection protocols are often detailed.
Post time:Apr - 29 - 2025