Types of Abrasives in Grinding
Grinding is a crucial manufacturing process that involves the removal of material from a workpiece to achieve desired shapes, dimensions, and surface finishes. At the heart of this process are abrasives, which are tough materials used to wear away, grind, or finish workpieces. Understanding the different types of abrasives in grinding is essential for selecting the right abrasive for a specific application. This article delves into the various types of abrasives used in grinding, outlining their characteristics, applications, and advantages.
1. Natural Abrasives
Natural abrasives have been used for centuries and are derived from naturally occurring materials. The most common types include
- Aluminum Oxide (Alumina) Found in nature as corundum, this abrasive is used extensively due to its durability and strength. It is well-suited for grinding metals and is available in various grades, from coarse to fine.
- Silicon Carbide This abrasive is known for its sharpness and hardness. It is often used for grinding hard materials like glass and ceramics. Silicon carbide abrasives are also suitable for non-ferrous metals, making them versatile for various applications.
- Garnet A natural mineral, garnet is used primarily for finishing surfaces. Its hard, crystalline structure makes it ideal for sanding applications in woodworking and paint removal.
2. Synthetic Abrasives
The advancement of materials science has led to the development of synthetic abrasives, which are engineered for superior performance. These include
- Aluminum Oxide (Synthetic) Similar to natural aluminum oxide but manufactured under controlled conditions. Synthetic aluminum oxide is more uniform and available in various forms such as fused and calcined, allowing for specific grinding applications.
- Cubic Boron Nitride (CBN) Known for its exceptional hardness, CBN is used for grinding hardened steels and superalloys. Its heat resistance makes it suitable for high-speed grinding applications, outperforming traditional abrasives in efficiency.
- Diamond The hardest known material, diamond abrasives are typically used in applications requiring extreme precision, such as in grinding ceramics, glass, and other hard materials. Diamond tools can be found in various forms, including wheels, segments, and saw blades.
types of abrasives in grinding
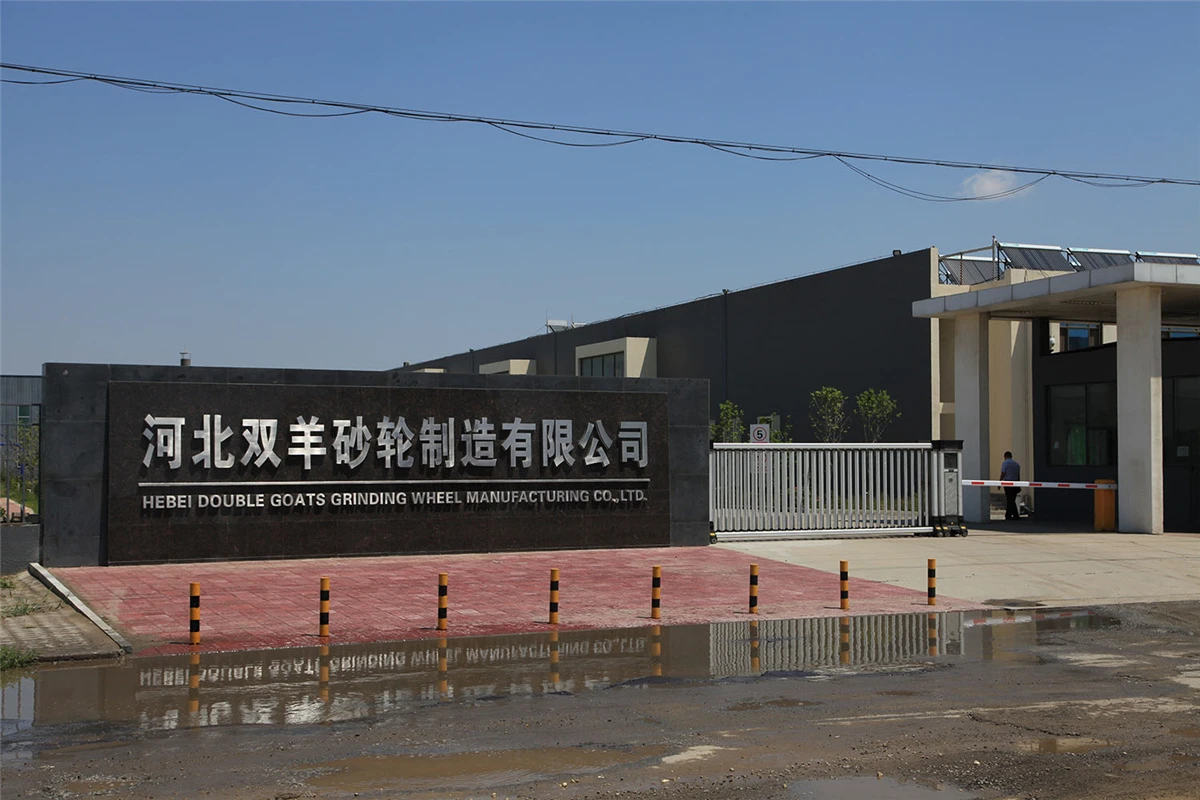
3. Types of Grinding Wheels
Abrasives are often used in grinding wheels, which are composed of abrasive particles bonded together. The type of bond used determines the wheel's performance.
- Vitrified Bond This type uses a glass-like bond that holds abrasives strongly together. Vitrified wheels are known for their rigidity and are widely used for high-speed grinding of metals.
- Resin Bond These wheels use synthetic resins to bond the abrasives, providing flexibility and resilience. They are ideal for precision grinding applications, where a smooth finish is essential.
- Metal Bond Used primarily for diamond and CBN abrasives, metal bond wheels provide excellent durability and are effective in high-performance grinding applications.
4. Applications of Abrasives in Grinding
Abrasives play a pivotal role in various industries, including automotive, aerospace, metal fabrication, and woodworking. They are used in processes such as
- Surface Grinding For achieving flat surfaces and precise dimensions on workpieces. - Internal Grinding Used to machine the internal surfaces of holes, ensuring accuracy and smooth finishes.
- Cylindrical Grinding Employed to grind cylindrical workpieces, enhancing their dimensional accuracy.
- Centerless Grinding A method where the workpiece is held between two rotating wheels, commonly used for producing small diameter parts.
Conclusion
The selection of the appropriate type of abrasive is vital for achieving optimal results in grinding processes. Natural abrasives offer traditional performance, while synthetic abrasives provide improvements in precision and versatility. Understanding the various types of abrasives and their respective applications allows manufacturers to choose the right tools for their specific needs, enhancing productivity and product quality in their grinding operations. As technology continues to evolve, the development of advanced abrasives will further shape the future of grinding techniques in various industries.
Post time:Oct - 11 - 2024