Types of Abrasives in Grinding Wheels
Grinding wheels are crucial tools in metalworking, used for shaping, sharpening, and finishing materials with precision. They consist of varying types of abrasives that determine their effectiveness in different applications. Understanding these abrasives is essential for selecting the right grinding wheel for specific tasks, ensuring efficiency and quality in the final product. This article explores the various types of abrasives found in grinding wheels, their unique properties, and applications.
1. Aluminum Oxide (Al2O3)
Aluminum oxide is one of the most common abrasives used in grinding wheels. It is known for its versatility and durability, making it suitable for various applications. This abrasive comes in different grades, ranging from coarse to fine, allowing for a wide range of grinding operations. aluminum oxide is particularly effective for grinding ferrous metals, such as steel and cast iron. Its sharpness and toughness enable it to maintain effective cutting performance over extended periods, making it a favorite among machinists and metalworkers.
2. Silicon Carbide (SiC)
Silicon carbide is another popular abrasive, known for its sharp cutting ability and hardness. It is typically used for grinding non-ferrous materials, such as aluminum, brass, and ceramics. Silicon carbide wheels can be found in a variety of colors, with black and green being the most common. The green variety is particularly effective for harder materials, while the black is used for softer substances. Silicon carbide offers excellent performance in wet grinding applications because it can withstand the heat generated in the process, making it ideal for projects where cooling is essential.
3. Cubic Boron Nitride (CBN)
types of abrasives in grinding wheel
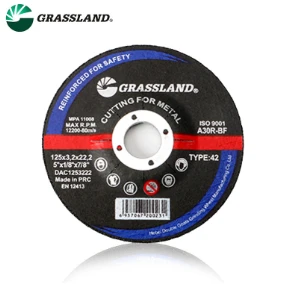
Cubic boron nitride is one of the hardest known materials, making it suitable for high-performance grinding applications. CBN wheels are commonly used in precision grinding of hard materials, including tool steels, high-speed steels, and superalloys. They are known for their thermal stability, which allows them to perform well under extreme temperatures. Unlike aluminum oxide and silicon carbide, CBN is not reactive with ferrous metals, resulting in less wear to the wheel and a longer lifespan. These properties make CBN wheels a popular choice in industries where precision and durability are paramount, such as automotive and aerospace engineering.
Diamond abrasives are renowned for their unparalleled hardness and are the best choice for grinding hard materials, including ceramics, glass, and composite materials. Diamond wheels are available in various configurations, including bonded wheels, segmental wheels, and tools. Their exceptional cutting ability allows for fine finishing and high precision, making them invaluable in applications such as tool sharpening and finishing surfaces in the manufacturing sector. However, diamond grinding wheels tend to be more expensive than other types, warranting their use in specialty applications that prioritize efficiency and quality.
5. Natural Abrasives
Natural abrasives, such as garnet, emery, and flint, have historically been used for various grinding applications. Although they have largely been replaced by synthetic abrasives, they still find use in specific instances, such as sandpaper or in applications where a more traditional or eco-friendly approach is desired. Natural abrasives are often used in applications that require a softer touch or less aggressive grinding, such as finishing or polishing.
Conclusion
The choice of abrasive in grinding wheels critically affects the efficiency and quality of grinding operations. Understanding the properties of different types of abrasives—aluminum oxide, silicon carbide, cubic boron nitride, diamond, and natural abrasives—enables manufacturers and metalworkers to select the appropriate tools for their specific applications. As technology advances, the development of new abrasive materials continues to enhance grinding efficiency, offering greater versatility and performance. Selecting the right grinding wheel not only optimizes the production process but also ensures the longevity and quality of the finished product, ultimately fulfilling the demands of various industrial applications.
Post time:Dec - 11 - 2024