Types of Abrasives Used in Grinding
Grinding is a fundamental manufacturing process characterized by the use of abrasives to achieve a desired finish on various materials. Abrasives are materials that can remove material from a workpiece through abrasive action, and they play a crucial role in various industries, including automotive, aerospace, and metalworking. The effectiveness of a grinding operation largely relies on the type of abrasive used. This article will discuss the primary types of abrasives used in grinding, focusing on their characteristics, applications, and benefits.
1. Natural Abrasives
Natural abrasives have been utilized for centuries. Common examples include materials like emery, corundum, and garnet. These abrasives are mined from natural deposits and have various hardness levels, allowing them to be used in different grinding applications.
- Emery is primarily composed of corundum and iron oxide and is often used for polishing metal surfaces. Its coarse grain structure makes it effective for material removal.
- Garnet is another natural abrasive that is known for its hardness and is often used in sandpaper and waterjet cutting due to its sharp edges and durability.
Natural abrasives are advantageous for certain applications, as they are cost-effective and environmentally friendly. However, their supply can be limited and sometimes inconsistent in quality.
types of abrasives used in grinding
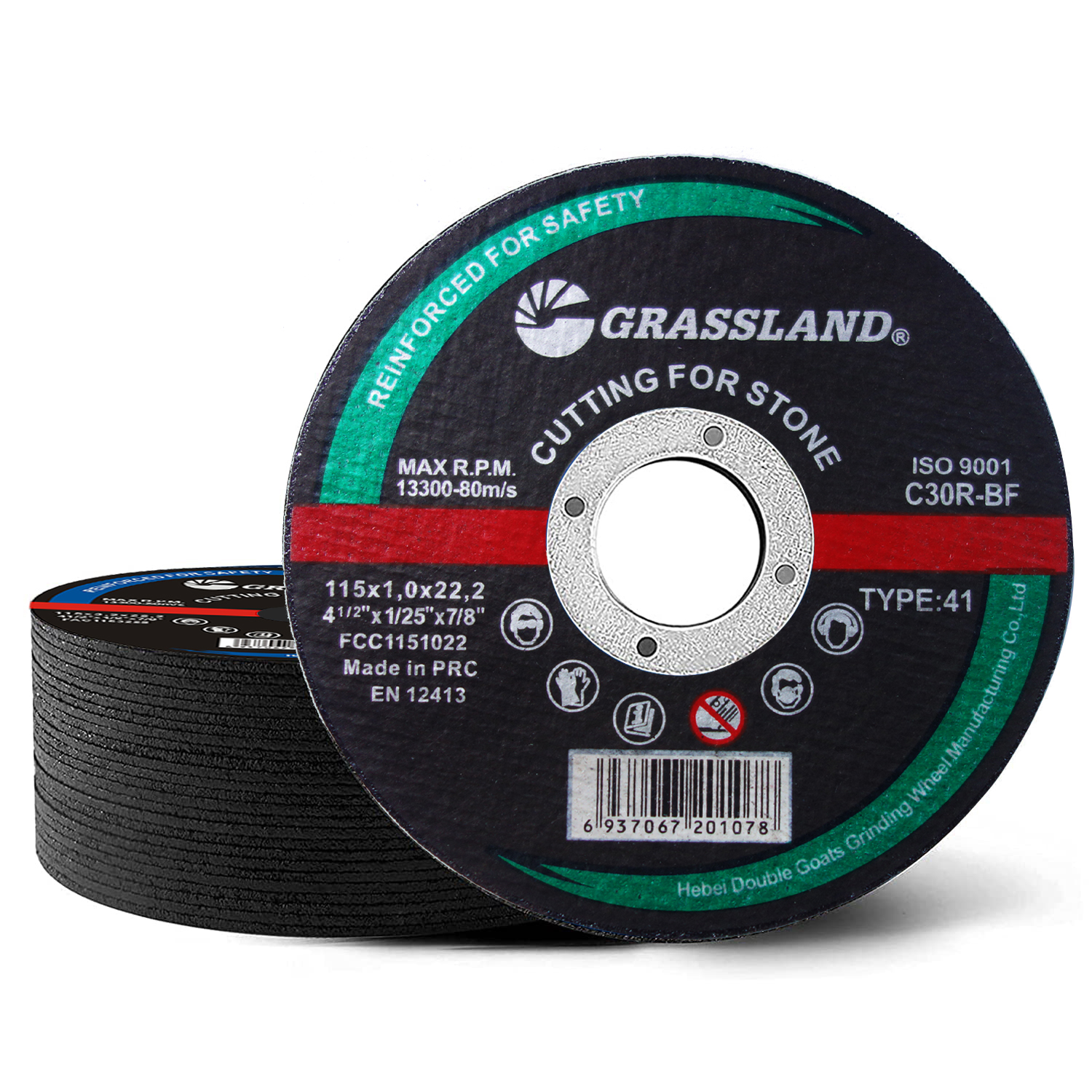
Synthetic abrasives are manufactured materials created to provide consistent performance and quality. They are generally preferred in modern grinding applications due to their enhanced properties and versatility. Some common synthetic abrasives include
- Aluminum Oxide This is one of the most widely used abrasives and comes in various forms such as white aluminum oxide and brown aluminum oxide. White aluminum oxide is ideal for grinding hard materials, while brown aluminum oxide is often used for general-purpose grinding.
- Silicon Carbide Known for its sharpness and hardness, silicon carbide is commonly used for grinding non-ferrous materials, glass, and ceramics. Its superior cutting ability makes it suitable for high-speed applications.
- Cubic Boron Nitride (CBN) This abrasive is second only to diamond in hardness and is primarily used for grinding high-speed steel and hard alloys. CBN tools are particularly advantageous in industrial settings where precision and longevity are key.
- Diamond Synthetic diamond abrasives are used in applications requiring extreme hardness and precision. They are commonly employed in grinding tools for ceramics, composites, and even in semiconductor manufacturing.
Synthetic abrasives offer several advantages over natural ones, such as consistency in shape, size, and hardness, allowing for better control over the grinding process. They also typically have longer lifespans, meaning they require less frequent replacement, which can lead to cost savings in the long run.
3. Conclusion
The choice of abrasive in grinding processes significantly impacts productivity, surface finish, and overall machining efficiency. Natural abrasives, while traditional, are often replaced in many applications by synthetic alternatives that provide superior performance and consistency. As manufacturing technologies continue to evolve, the development of advanced abrasives will likely lead to even greater efficiencies in grinding operations. Understanding the characteristics and applications of different types of abrasives enables manufacturers to select the most appropriate materials for their specific grinding needs, ultimately enhancing product quality and reducing production costs.
Post time:Dec - 21 - 2024