Types of Abrasives Used in Grinding Wheels
Grinding wheels are essential tools in various industries, utilized for cutting, shaping, and finishing materials. The performance and effectiveness of a grinding wheel largely depend on the type of abrasive used. Abrasives are materials that have high hardness and the ability to wear away softer materials through friction. Understanding the different types of abrasives used in grinding wheels is crucial for selecting the right wheel for specific applications.
1. Aluminum Oxide
Aluminum oxide is one of the most commonly used abrasives in grinding wheels. It is known for its toughness and resistance to wear, making it suitable for grinding ferrous metals and various materials. Aluminum oxide can be found in various forms, including white, pink, and brown. Each variation has unique properties; for instance, white aluminum oxide is generally purer and harder, making it ideal for finer applications. Pink aluminum oxide, on the other hand, offers a perfect blend of toughness and friability, making it suitable for a wide range of grinding operations.
2. Silicon Carbide
Silicon carbide is another widely used abrasive, characterized by its sharp edges and high hardness. This material is particularly effective for grinding non-ferrous materials like aluminum and brass, as well as hard materials like ceramics and glass. Silicon carbide grinding wheels are typically green in color, which indicates their hardness and ability to withstand the rigors of demanding grinding tasks. Furthermore, silicon carbide abrasives have a friable nature, allowing them to break down and expose new sharp edges, maintaining a consistent cutting action.
3. Cubic Boron Nitride (CBN)
types of abrasives used in grinding wheels
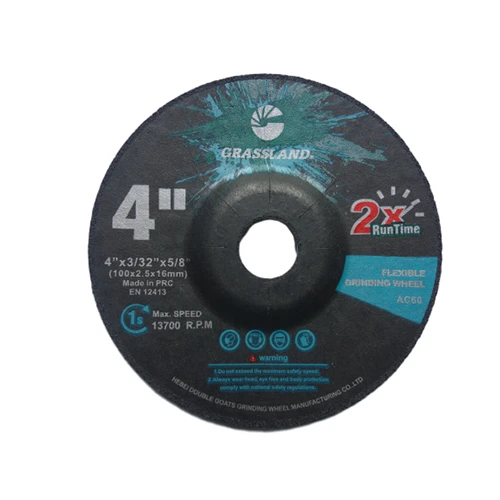
Cubic boron nitride, often referred to as CBN, is recognized as the second hardest material after diamond. CBN abrasives excel in high-temperature applications and are primarily used for grinding hardened steel and superalloys. These grinding wheels are particularly valued in the aerospace and automotive industries due to their durability and ability to maintain shape during rigorous grinding processes. Although CBN wheels are more expensive than other types, their performance in heavy-duty applications often justifies the cost.
4. Diamond
.
Diamond grinding wheels are the premier choice for precision grinding due to their unmatched hardness and wear resistance. They are primarily used for grinding hard materials, including ceramics, glass, and concrete, as well as in specialized applications like sharpening tools. Diamond abrasives are either metal bonded or resin bonded, depending on the application. Metal-bonded diamond wheels are ideal for heavy-duty grinding, while resin-bonded wheels provide a higher level of precision in finer applications.
5. Glass Abrasives
Glass abrasives are an emerging option in the grinding wheel market. Made from recycled glass, these abrasives offer an eco-friendly alternative to traditional materials. While not as common, glass abrasives are valued for their sharpness and ability to produce finer finishes on softer materials. They can be used in deburring and polishing applications, contributing to sustainable practices in the manufacturing industry.
Conclusion
The choice of abrasive in grinding wheels significantly influences the performance and efficiency of machining operations. Aluminum oxide and silicon carbide are the workhorses of the industry, suitable for a variety of materials. CBN and diamond abrasives stand out for specialized tasks, providing unparalleled strength and precision. As technology evolves, new materials like glass abrasives are also gaining traction, promoting sustainability in grinding practices. Understanding these options allows manufacturers to optimize their processes, ensuring superior product quality and efficiency. Whether in automotive, aerospace, or metalworking industries, selecting the right abrasive is critical to achieving the desired results in grinding applications.
Post time:Nov - 30 - 2024