Types of Bonds in Grinding Wheels
Grinding wheels are essential tools in various industrial and manufacturing processes, primarily used for material removal through the grinding technique. Understanding the types of bonds used in grinding wheels is crucial for selecting the appropriate wheel for specific applications. Bonds serve as the adhesive material that holds the abrasive grains together, providing structural integrity and performance characteristics. This article explores the primary types of bonds used in grinding wheels, including vitrified, resin, metal, and ceramic bonds.
1. Vitrified Bond
Vitrified bonds are one of the most common types of bonding materials used in grinding wheels. They are made from feldspar and clay that are fused together at high temperatures to form a glass-like structure. Vitrified bonded wheels are known for their excellent hardness and strength, which allows them to withstand high grinding pressures and maintain their shape even under intense conditions.
The key advantages of vitrified bonds include their high resistance to heat, low wear, and the ability to produce finer finishes compared to other bond types. These wheels are typically used for precision grinding applications, such as in the manufacturing of tools, dies, and precision components. However, their brittleness can be a drawback, as they may break under excessive shock or impact.
2. Resin Bond
Resin bonded wheels are another popular choice, primarily made from synthetic resins that offer greater flexibility compared to vitrified bonds. These wheels can provide a more aggressive cutting action due to the resilience of the bond material, which helps in dissipating heat and reducing glazing during grinding. As a result, resin bonded wheels are particularly effective for metal grinding, polishing, and finishing applications.
One of the notable advantages of resin bonds is their ability to produce a softer grinding wheel, which can enhance the surface finish of the workpiece. Additionally, they can be designed to wear evenly, maintaining consistent grinding performance throughout their life. However, resin bonded wheels generally have a lower temperature tolerance compared to vitrified wheels, making them less suitable for high-heat applications.
types of bond in grinding wheel
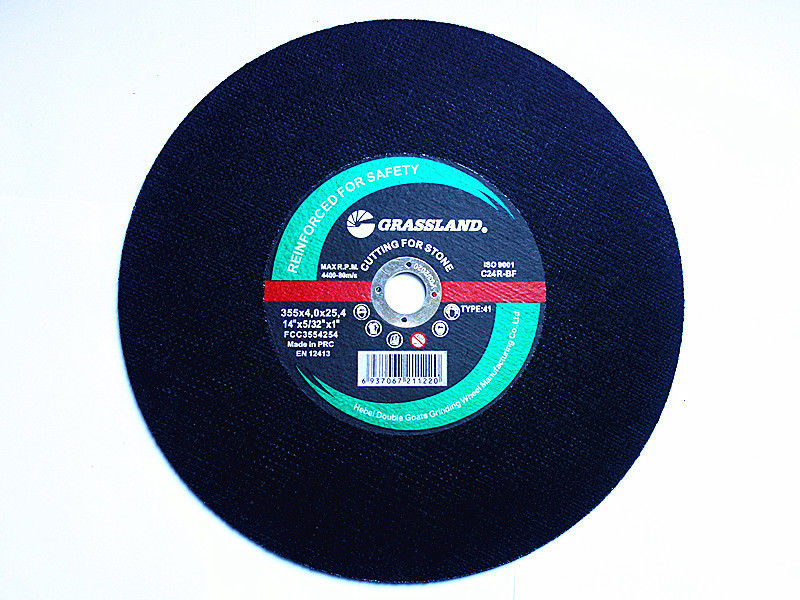
3. Metal Bond
Metal bonded grinding wheels involve the use of metal as the bond material, often incorporating bronze, nickel, or other metals to create a robust, durable wheel. These wheels are specifically designed for heavy-duty applications, such as grinding hard materials, including ceramics and composites. The metal bond’s strength enables it to withstand high abrasive forces, making it ideal for industries that require significant material removal.
Metal bonded wheels are characterized by their long lifespan and consistency in performance. They can be used in applications that generate high heat without compromising the structure of the wheel. However, they may not provide as fine a finish as resin or vitrified bonded wheels, making them more suitable for rough grinding processes rather than precision finishing.
4. Ceramic Bond
Ceramic bonded wheels represent a relatively newer advancement in grinding technologies. These wheels utilize a unique type of ceramic material as the bond and offer an exceptional balance of resilience and hardness. Ceramic bonds are particularly advantageous in high-speed grinding environments due to their thermal stability and low thermal expansion.
The key benefit of ceramic bonded wheels is their self-sharpening capability. As the wheel wears down, the grinding action exposes new, sharp abrasive grains to the surface, ensuring continuous cutting performance. This feature makes ceramic bonds ideal for applications requiring high precision and surface integrity, such as aerospace and automotive manufacturing.
Conclusion
Choosing the right type of bond in grinding wheels is critical for achieving optimal grinding performance. Vitrified bonds offer hardness and precision, resin bonds provide flexibility and surface finish, metal bonds excel in durability and heavy-duty applications, and ceramic bonds deliver self-sharpening capabilities for high-speed grinding. Understanding these bond types allows manufacturers and machinists to select the appropriate grinding wheel for their specific needs, ultimately enhancing efficiency and productivity in various industries. Whether it be for rough grinding or precision finishing, the right bond selection is essential for successful grinding operations.
Post time:Nov - 25 - 2024